事例(生産)
事例1:より効率の高いコージェネレーションシステム(CGS)*1への更新
プロジェクターに搭載されている高温ポリシリコンTFT液晶パネルや、PrecisionCoreマイクロTFPプリントヘッドなどを製造する諏訪南事業所は、エプソンの国内事業所の中でも電力使用量が多い事業所です。2001年より1台のCGSを導入し、電力使用量の約40〜60%を工場内で発電し使用してきましたが、2014年5月に、より高効率な3台のCGSへの置き換えを実施したことで、燃料となる天然ガスの使用量とCO₂排出量を削減することができました。また、複数台稼働となったことでメンテナンス性が向上し、電力の安定供給が可能になりました。
*1 コージェネレーションシステム(Co-Generation System):熱源より電力と熱を生産し供給するシステムの総称
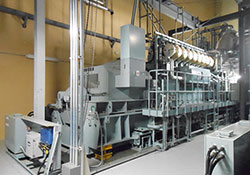
CGS設備概要
発電出力 | 台数 | 型式 | 燃料 | |
---|---|---|---|---|
新規 | 2,270kW | 3台 | ガスエンジン | 天然ガス |
従来 | 7,200kW | 1台 | ガスタービン(二流体方式) | 天然ガス |
年間効果量(ガスタービン式からガスエンジン式に更新した効果)
天然ガス削減量:約1,480,000 Nm³
CO₂削減量:約4,900 トン
CGSのメリット
発電所から供給される従来のシステムでは、利用されない廃熱や送電ロスが60%あるのに対し、CGSによる分散型発電は廃熱を15~30%に抑えることができます。また、電気エネルギーのほかにも、30%ほどの廃熱を熱エネルギーとして冷暖房等に有効利用でき、省エネにつながります。
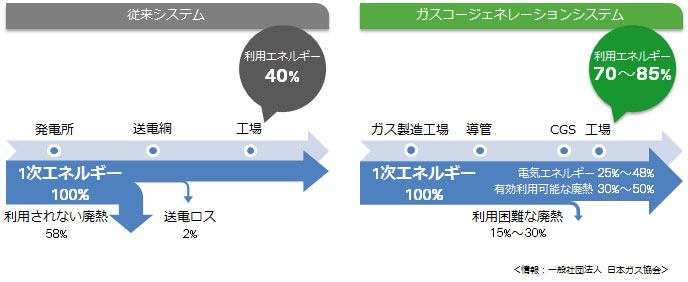
事例2:見える化による空調管理のCO2削減
Epson Portland Inc.(EPI/米国)は、エプソンのインクカートリッジを米州市場向けに製造する重要な拠点の一つです。品質レベルの確保のためクリーンルームを必要とすることから、空調および生産に関わる工場設備機器に毎年700万kWh以上の電力を使っていました。
そこで、消費エネルギーを減らし環境負荷低減に取り組むために、2011年に非営利団体である「Energy Trust of Oregon」の協力を得て、空調機器の新しいモニタリングシステムを導入しました。
これにより、インクカートリッジの生産エリア内の室内温度を継続的に計測し記録することが可能となりました。その記録を基に空調システムに改良を加えた結果、クリーンルーム内の設定室温より外気温の方が低い場合、内部の暖まった空気を自動的に排気し、外の涼しい空気を取り込むことで、空調システムを頻繁に稼働させることなく温度調整を行えるようにしました。この施策で年間100トン以上のCO₂削減につながりました。
EPIはこのシステムを導入した後も、毎年のようにさまざまな省エネ施策を実施し続けることで、2014年までに累計655トンのCO₂を削減することができました。