Case Study - Customer Environmental Impact Mitigation
We sell products and services that transform the way our customers work. In so doing, we are minimizing their environmental impacts while also raising their operational efficiency and productivity.
- Our innovative products and services make our customers' jobs and lives easier and more enjoyable while also shrinking their environmental footprints.
- Our products and services enable new business processes and offer outstanding economic and environmental value.
Office
Shrinking the Environmental Footprint of Offices with a Combination of Performance and Efficiency
Epson's business inkjet printers employ our original Heat-Free Technology to eject ink without heat. This technology achieves outstanding low power consumption performance.
Our business inkjet printers with built-in PrecisionCore lineheads (WorkForce Enterprise WF-C series and AM-C series) are products with both a high-level printing performance of 40 to 100 pages per minute (ppm) and low power consumption. The WF-C21000 achieves a printing speed of 100 ppm1. This printing speed approximately doubles productivity in contrast to the printing speed of 50 ppm for general laser printers used in offices.
1 For single-sided A4 sheets. WF-C20750 series: 75 ppm / AM-C series: 40, 50 and 60 ppm
Ideas for the Office
Businesses are more sensitive than ever to environmental issues. Many try to save energy by adjusting their thermostat settings or adopting LED lighting. What they may overlook is that printers and MFPs account for about 10% of total power consumed in a typical office.
We see an opportunity to help them further cut their energy use and costs. Epson inkjet printers draw very little power when printing because ink droplets are ejected by the action of piezoelectric elements that contract under only a tiny applied voltage. In contrast, laser printers require heat–and a lot of electricity–to fuse toner to paper.
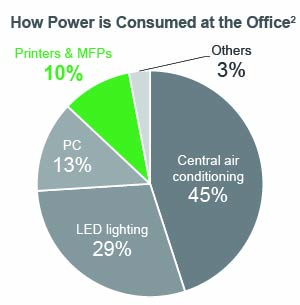
2 Epson research based on data from commissioned survey conducted in March 2018 by SOMPO Risk Management & Health Care Inc.
Power Consumed per Page
The graph below shows the estimated energy consumed per page. The figures, which are based on typical electricity consumption (TEC) values provided by the ENERGY STAR®, may be used as a guide to compare products running at different speeds. The graph indicates the superior energy efficiency of Epson WorkForce Enterprise series compared to typical A3 color laser office MFPs.
Power Consumed per Page
The graph below shows the estimated energy consumed per page. The figures, which are based on typical electricity consumption (TEC) values provided by the ENERGY STAR®, may be used as a guide to compare products running at different speeds. The graph indicates the superior energy efficiency of Epson WorkForce Enterprise series compared to typical A3 color laser office MFPs.
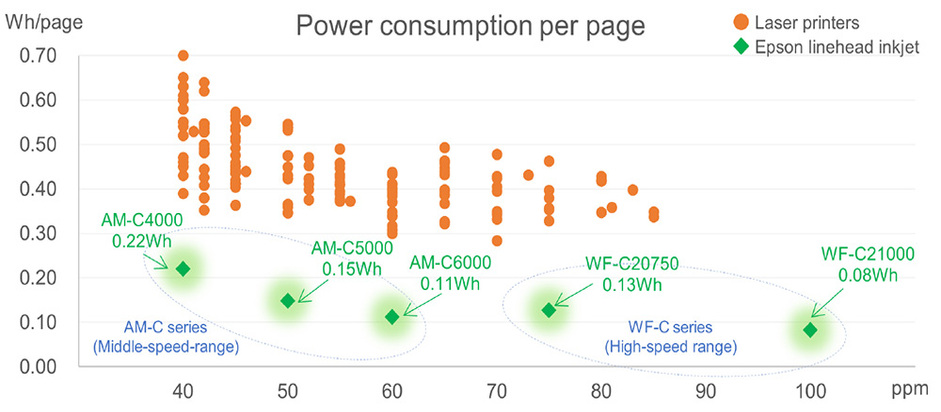
* Comparative simulation of power consumption per page. All A3 color MFPs with outputs of 40-100 ppm (excluding Digital Front End) which is posted on energystar.gov as of September 11, 2023. Our per page calculations are based on TEC measurement.
Reduces Annual Electricity Consumption
WorkForce Enterprise printers are equipped with PrecisionCore Heat-Free Technology and use no heat in the printing process. That means they consume far less power than laser printers, which in turn reduces their running costs. According to the results of an independent study, AM-C5000 may consume, on average, 80% less electricity per year than comparable competing color laser multifunction printers.
* Keypoint Intelligence-Buyers Lab was commissioned by Epson to evaluate the WorkForce Enterprise AM-C5000 (50ppm) for Europe. Test data is from May 2023. Epson selected four competitor's models from worldwide top five best-selling vendor3 in the 41-50 ppm color laser multi-function printer class. Devices were tested in default mode as per Keypoint Intelligence's proprietary standard energy consumption test methods. Calculations were based on a weekday workload of 2 x 4 hours printing + 16 hours in sleep/standby mode, and weekend energy use of 48 hours in sleep/standby mode. A total of 69 pages of workload test pattern using DOC, XLS, PPT, HTML, PDF files and Outlook email messages were printed six times in each four-hour printing period.
3 Source: IDC's Worldwide Quarterly Hardcopy Peripherals Tracker 2023Q1, Units Share by Company
Recognized for Excellence in Energy Efficiency and Conservation
ラインインクジェット複合機LMシリーズ*4は、新しい回路ユニットの導入によりスリープおよび動作時の電力消費が低減し、さらなる省エネ性能を実現したことなどが評価され、一般財団法人省エネルギーセンターが主催する2023年度「省エネ大賞」(製品・ビジネスモデル部門)の資源エネルギー庁長官賞を受賞しました。(2023年12月)
*4 WorkForce Enterprise LM-C6000/C5000/C4000
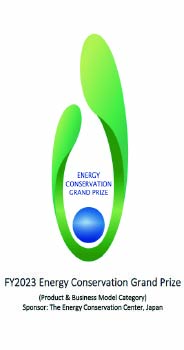
Seiko Epson received the Agency for Natural Resources and Energy Commissioner's Award (Product & Business Model Category) for their new MFPs4 under the fiscal 2023 Grand Prize for Excellence in Energy Efficiency and Conservation awards program organized by the Energy Conservation Center, Japan. Among other things, the new MFPs were recognized for their higher energy efficiency compared with the previous models for the reason such as the introduction a new circuit unit reduces power consumption in sleep mode and during operation. (December 2023)
4 WorkForce Enterprise LM-C6000/C5000/C4000 linehead inkjet multifunction printers.
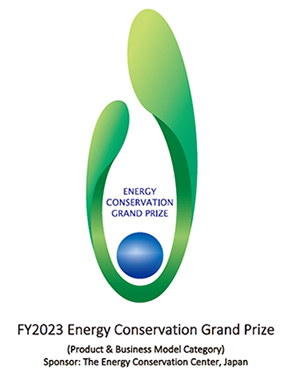
Eco Features
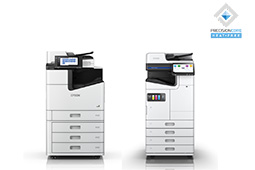
- Inkjet multi-function printers with linehead enabled by Epson PrecisionCore and Heat-Free Technology take the combination of print performance and energy efficiency to the next level.
- Epson WorkForce Enterprise series demonstrates superior energy efficiency than a typical A3 color laser office MFPs.
- The maximum power consumption is below 320W5, making it suitable for use with the common 100V, 15A outlets found in typical office settings.
5 WF-C21000 series: 320W, WF-C20750 series: 300W, AM-C series: 190W
ラインインクジェット複合機の商品情報はこちらにご覧ください。
An Eco-Conscious Office Created by Combining Inkjet Printers with an Office Papermaking System
Epson is proposing eco-conscious office solutions that benefit the environment.
Epson wrings the maximum benefit for customer from solutions that combine inkjet printers, which employ Epson's proprietary Heat-Free Technology to reduce office power consumption, waste, and printing costs, with dry process office papermaking systems, which efficiently recycle paper to conserve water and forest resources. In addition to allowing a more environmentally friendly way to take advantage of the convenience of paper, an in-office paper recycling ecosystem delivers customer value by reducing costs and strengthening information security.
Epson installed 16 PaperLabs at its nine main sites in Japan. Through the local recycling of paper for local consumption, Epson is looking to reduce the amount of new paper purchased by the Epson Group. Furthermore, the Eco-Conscious Office Center in EPSON SQUARE MARUNOUCHI serves as a model for a metro office. It demonstrates to visitors that a greener office can be achieved anywhere.
Epson is giving potential customers a concrete idea about how they can improve their environmental performance by publicly disclosing our paper recycling operations and recycling data.
Raising Meeting Productivity with Interactive Communication
Epson's interactive projectors increase the productivity of interactive meetings, deliver more effective presentations, and even contribute to a smaller environmental footprint.
EB-1485Fi
(known as the BrightLink 1485Fi in certain markets)
Reduce Your Environmental Footprint with Videoconferencing
Connect your existing videoconferencing system to the projector, and use the projector's multi-location interactive and split-screen functions to display your videoconference on one side of the screen and your presentation on the other, to achieve virtual face-to-face collaboration.
This interactive projector can reduce the need for travel and reduce your environmental footprint.
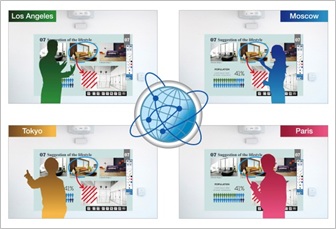
Multi-location Interactive Function
- Share your PC screen with up to four locations.
- Participants in all locations can annotate a presentation and save the content to their PCs.
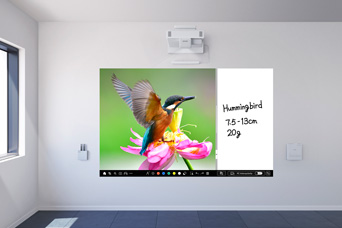
Split Screen Function
- Achieve virtual face-to-face collaboration while sharing whiteboard and PC screen images.
- Clearly display different content on a split screen that measures up to 100 inches.
Use as a Copyboard
The all-in-one interactive projector with copyboard, electronic blackboard, and other common whiteboard functions saves both resources and installation space. Directly annotate up to 20 sheets' worth of projected data and images, no PC required. Increase meeting productivity and minimize printouts by saving data or by emailing it directly from the projector.
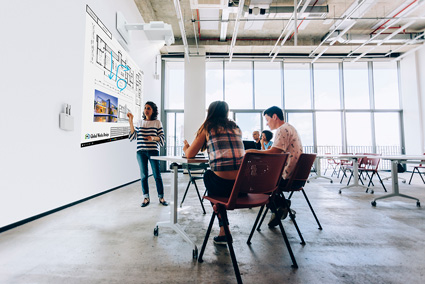
Maintenance-free Light Source
The laser light source is extremely reliable, eliminating the worry of lamp failure during important presentations.
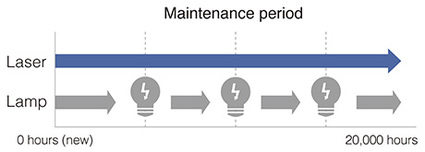
Energy and Resource-saving
Within the projector's lifecycle, CO2 emissions will be the greatest during the stage in which it is used by the customer.
Through product improvements, we will offer reductions in the consumption of electricity and natural resources during use.
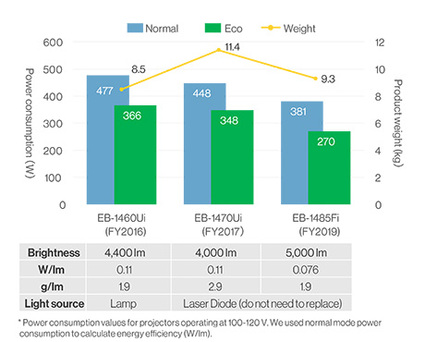
Eco Features
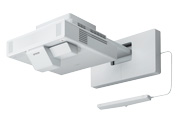
- Connect your videoconferencing system to the projector, and use the multi-location interactive and split-screen functions to display your videoconference on one side of the screen and your presentation on the other, to achieve easy remote collaboration and reduce the need for travel. Helps to reduce your environmental footprint.
- This all-in-one interactive projector includes copyboard, electronic blackboard, and other whiteboard functions to save both resources and installation space.
- Projected data and images can be annotated with digital pens. Minimize printouts by saving data as is or by emailing it directly from the projector.
- The laser light source is extremely reliable, eliminating the worry of lamp failure during important presentations.
- Energy-saving features
- An illuminance sensor detects ambient brightness and automatically adjusts the output of the lamp
- You can reduce power consumption by as much as 29% using ECO mode
Home
Reducing Environmental Impact with High-Capacity Ink Tank System
Inkjet printers with a high-capacity ink tank system are refilled from bottles. Compared to traditional cartridge-based printers, the high capacity of ink bottles reduces the frequency of consumable replacements for the same amount of ink used, thereby minimizing the resources required for consumables, including its packaging.
Comparison of Environmental Impact with Ink Cartridge Printers
A comparison of the environmental impact between the high-capacity ink tank printer ET-2400 and the ink cartridge printer XP-42001 shows that for printing 15,000 pages2, the number of consumables used is reduced from 364 ink cartridges to nine ink bottles, resulting in a 92% reduction in the environmental impact of consumables. This contributes to reducing the overall environmental impact across the entire lifecycle of the high-capacity ink tank printer.
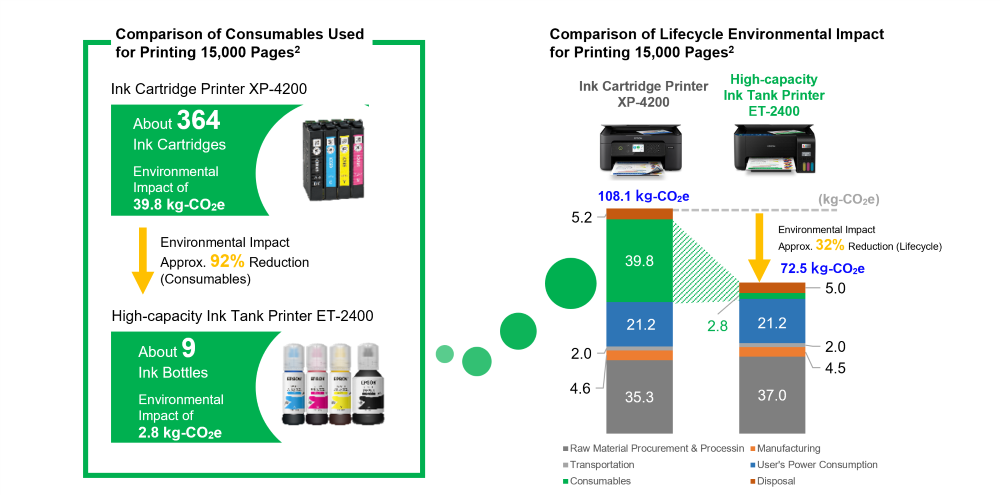
1 Calculated based on Epson's evaluation criteria using data from each stage of the product lifecycle (raw material procurement, manufacturing, transportation, use, and disposal) with verification of the calculation method by Mizuho Research & Technologies, Ltd. Results may vary depending on customer usage and product specifications.
The impact of paper is not considered in this calculation.
2 The number of pages printed over five years based on a printing speed of 10.5 ipm, in accordance with TEC standards.
Reducing Environmental Impact with High-Capacity Ink Tanks
As of October 2024, the cumulative global sales of Epson's high-capacity ink tank printers have reached 100 million units. Compared to ink cartridge printers that meet similar printing needs, this has resulted in a cumulative mitigation of approximately 1.63 million tons of CO2emissions3. By shifting to high-capacity ink tank systems, resource consumption for consumables can be reduced, contributing to the overall reduction of environmental impact across society.

3 The mitigation in environmental impact is calculated by comparing the total CO2 emissions over the entire product lifecycle of corresponding ink tank models and ink cartridge models, then multiplying the difference by the sales volume in each region. For the cumulative calculation, approximately 62.5 million units out of the 100 million total were considered, as they have comparable ink cartridge model counterparts.
Eco Features
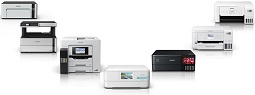
- Inkjet printers with high-capacity ink tanks reduce resource consumption associated with consumables compared to traditional inkjet printers, contributing to lower environmental impact throughout their lifecycle.
Manufacturing Plant
Label Printing Technology Shifting from Analog to Digital
The trend toward short-run print jobs has spread to labels and packages, giving rise to demand for efficient printing systems that can agilely respond to this demand. Epson's digital inkjet label presses provide customers with a new label printing workflow that meets their needs.
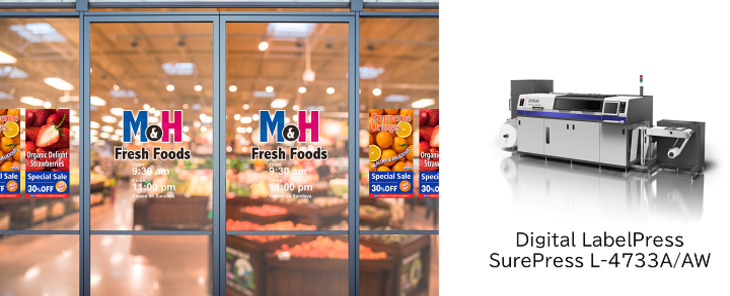
An Efficient Label Printing Process with a Low Environmental Impacts
A digital printing process does not need the press plates and other prepress processes required by analog printing processes. And, since a digital process does not use developer or film or plate materials, it conserves resources. Capable of stable, consistent output, a digital process does not require mock-ups and thus can reduce the waste of ink and label substrates during setup. Digital label presses thus offer both a more efficient workflow from start to finish and lower environmental impacts.
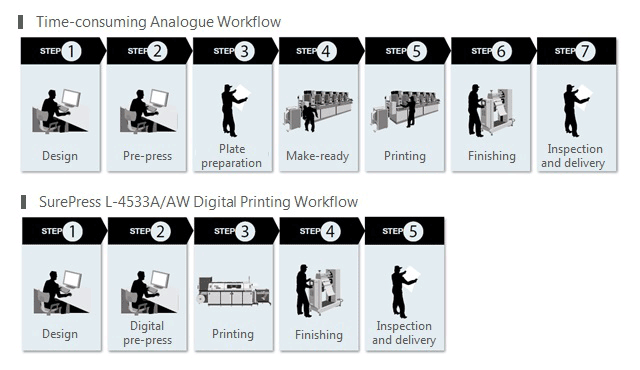
Water-based pigmented inks for less hassle
SurePress AQ ink T4, the water-based pigment ink used in Epson's digital label press, has high fusing properties and does not require precoating of the printed paper.
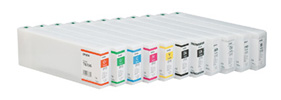
Eco Features
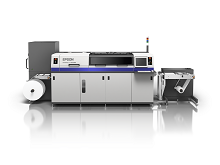
- Save resources by removing the need for pre-press process like plate making, and eliminating the use of developer and films.
- Easy color-matching and no replacement of plates makes the SurePress less wasteful, and enables it to consume less standard label stock and ink.
- No need for special cleaning eliminates waste fluid emissions from maintenance.
- Removing the need for pre-treatment, SurePress water-based ink has good adhesion on a variety of standard label stocks.
Reducing Environmental Impacts by Providing Remote Work Assistance with Smart Headsets
Epson's smart headsets with binocular, see-through lenses increase operational efficiency and work quality by displaying digital manuals and work instructions in the field of vision and enabling workers to perform work with both hands. In industrial settings, these headsets can be used by managers to provide remote service and maintenance personnel, for example, with instructions and assistance.
1 Helmet is not included as product
Remote Work Assistance
The centered high-resolution 8 mega-pixel front-facing camera enables workers to share their view and receive help with complex tasks through streaming or recorded Full HD pictures and videos.
In addition to safely increasing work efficiency and contributing to greater overall operational efficiency, Epson's smart headsets enable skilled personnel in a remote location to provide technical instructions to workers on the ground. This helps to reduce the need for travel and, consequently, your environmental footprint.
Advantages
- Printed paper manuals and instructions are rendered unnecessary.
- Greater work efficiency thanks to hands-free operation.
- Tasks can be completed safely because the binocular, see-through lenses allow workers to see their surroundings through projected content.
- Images and voice can be shared with workers in remote locations so that assistance can be provided effectively.
Usage Scenes
Used for work where they wear caps, or where they do not need to wear anything on their head
- Infrastructure (server room)
- Manufacturing (assembly of office automation equipment, household appliances, vehicles, etc.)
- Maintenance (large equipment such as aircraft, semiconductor manufacturing equipment)
- Agriculture (technology transfer)
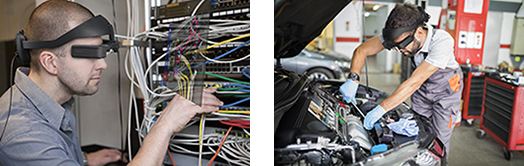
Used for work where wearing a helmet is mandatory
- Infrastructure (electricity, gas, water)
- Manufacturing (heavy machinery, steel, robotics)
- Construction, Public Works (building construction, excavations, bridges)
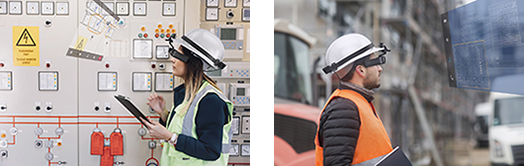
Eco Features
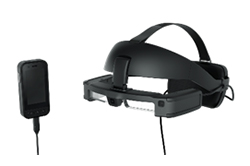
- The headsets are equipped with a camera and sensors that provide remote personnel with an accurate picture of the situation so that they can provide workers on the ground with instructions and assistance without having to travel, so the environmental impacts associated with travel can be reduced. The headsets also promise to reduce downtime and time losses associated with travel.
- Hands-free operation enables tasks to be performed safely and efficiently, improving both operational efficiency and work quality.
Make More with Less: Micro Injection Molding Machines for Superior Financial and Environmental Performance
The smaller the parts, the greater the waste of materials and energy consumed in the manufacturing process.
Epson’s micro injection molding machines solve this customer issue by allowing users to make more with less.
Epson’s AE-M3 and AE-M10 micro injection molding machines employ a proprietary disk drive system that dramatically reduces machine size, making them ideal for molding small, precision parts with exceptional energy efficiency.
These machines are standard-equipped with a hot runner system that minimizes waste and efficiently uses input resources.
* Only available in Japan
Fast, Precision Injection with Minimal Energy and Waste
Injection molding machines melt a plastic material with a heater and precisely inject the molten material into a mold cavity, where the material cools and hardens before being ejected as a molded product.
Epson's micro injection molding machine employs a proprietary disk drive system to melt and inject the plastic. The molten plastic is precision injected with minimal energy. The short melting path has the additional benefit of reducing damage to thermally sensitive materials, thus helping to ensure good molding quality.
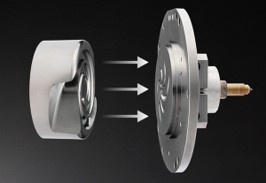
The hot runner system that is standard on these molding machines minimizes material waste from runners and other parts in the molding process. It also shortens cooling time after mold clamping, which reduces molding time (cycle time) and thus increases productivity.
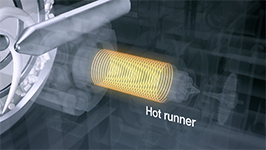
Click here for a movie of the injection molding process
*The video above was provided using the service of YouTube™. YouTube™ is a trademark of Google Inc.
Reduces CO2 by Conserving Energy, Saving Space, and Reducing Waste Plastic
Epson's micro injection molding machines have a far smaller environmental impact than the average 30-ton molding machine. In addition to unrivaled compactness and an energy saving design, our machines eliminate much of the waste material from runners and such that are generated in the part molding process.
* This evaluation compares the impacts of a 30-ton machine and a 3-ton machine when producing 500,000 Epson printer parts per month. Calculations were checked using a method of Mizuho Research & Technologies Institute. Epson's AE-M3 (3-ton molding machine) produces two parts at a time and has a molding time of 694 hours, whereas the average 30-ton molding machine of other companies produces eight parts at a time and has an average molding time of 382 hours. The manufacturing, transportation, and disposal stages of products and accessories are not taken into account when calculating CO2 emissions.
These are the estimated results of a hypothetical model based on Epson’s actual results, and the calculation results may differ depending on the conditions of the customer's equipment and materials.
Calculation conditions: Cubic volume of part was 0.5㎤, plastic material was POM, the 30-ton machine was a composite imagined using the mean value of three representative models from other manufacturers, and the installation area was the molding machine installation space + incidental equipment + work space.
2022 Good Design Award
The micro injection molding machine AE-M3 and AE-M10 won a 2022 Good Design Award, which presented annually for designs that benefit and enrich our lives and society. In addition, these were selected for the Good Design Gold Award and the Good Design Best 100.
< Reasons for Award >
Global industries need to find ways to economically produce the goods that are needed in only the amounts they are needed. However, there is a structural dilemma in that high-mix, low-volume production results in large losses; in fact, making more with less-less waste, less energy-is hard to do. We live surrounded by all kinds of plastic products, most of which are made using large plastic molding machines that waste significant amounts of material. Epson's micro injection molding machines are revolutionary in that they can efficiently do the work of a large factory in an area the size of a desktop.
Eco Features
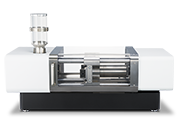
Designed around the concept of “making more with less,” the AE-M3 and AE-M10 are micro injection molding machines that support on-demand production and mass customization.
- A proprietary disk drive system dramatically reduces machine size and achieves exceptional energy efficiency. These machines are standard-equipped with a hot runner system that minimizes waste and efficiently uses input resources.
- The machines save energy and reduce plastic waste, thereby reducing CO2 emissions by as much as 78%1 compared to an average 30-ton machine from other manufacturers.
1 A 78% reduction from the average CO2 emissions of a standard 30-ton machine from other manufacturers. This figure is an estimate for when the same quantity of parts is produced using a model based on Epson's actual results.
Stores
Intelligent Receipt Printers that Control Peripherals
TM-T70II-DT2 and TM-T88VI-DT2 are next-generation receipt printers with integrated printer and PC functions that support smart store operations when connected with tablet and POS peripherals.
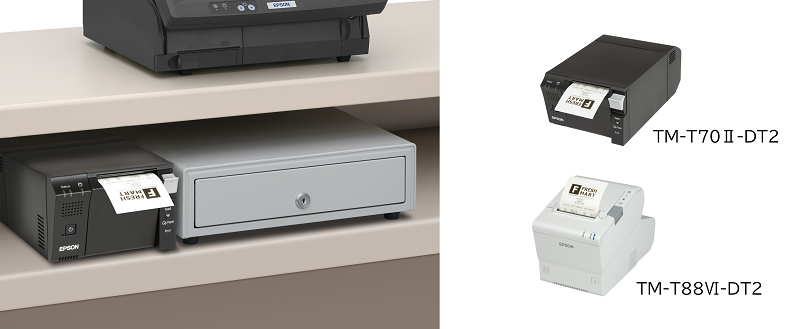
Greatly Simplified System Configuration
These receipt printers are loaded with interfaces for connectivity with a wide assortment of peripheral devices. They can be used with a web browser and are not dependent on any specific operating system or terminal type, simplifying POS system configuration.
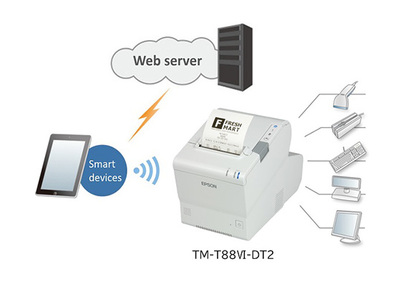
Easy maintenance
The latest applications are always available through the cloud (Web server), reducing the environmental impact of service staffs' business travel for onsite installation and updates.
POS configuration flexibility
The number of POS systems can be flexibly changed depending on the level of demand, contributing to the optimization of equipment utilization and reducing electricity consumption.
Every network terminal is available
Electricity-saving devices like smartphones can be used because the Intelligent receipt printer is not restricted by the type of terminal or operating system.
Resource-saving design
By using the paper saving modes for standard receipt lengths, it is possible to achieve up to a 49%1 reduction in paper usage.
Eco Features
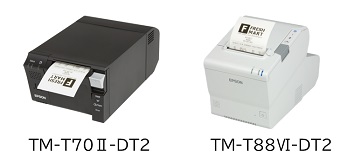
- Because the number of POS systems can be flexibly changed depending on the level of demand, users can reduce the electricity consumption of their operation by removing unnecessary devices.
- The latest applications are always available through the cloud (Web server), reducing the environmental impact of service staffs' business travel for onsite installation and updates.
- Electricity-saving devices like smartphones can be used because the Intelligent receipt printer is not restricted by the type of terminal or operating system.
- By using the paper saving modes for standard receipt lengths, it is possible to achieve up to a 49%1 reduction in paper usage.
1 The combination of paper saving and backward paper feeding is measured using a test pattern defined by Epson, with the actual reduction amount varying depending on the printing pattern.
Other (Textiles, Labels, Photographs)
Driving Production Process Innovations with Digital Textile Printers
Epson's digital textile printers faithfully reproduce prints in vivid colors and wonderful detail-and they do so with outstanding throughput and minimal environmental impact.
Monna Lisa
Streamlined Manufacturing Process
Epson's inkjet digital textile printers expand your design possibilities while minimizing your use of energy, water, materials, and time compared to conventional processes. Digital textile printing involves the use of printing systems to print out digital data to direct to fabric. It is different from traditional analog printing in which dedicated printing plates are pressed directly onto the fabric. Digital printing has the following characteristics:
- Faithful reproduction of fine gradations and subtle color tones
- Since no analog plates are needed, digital textile printing saves storage space, eliminates time spent on plate management, and enables small production runs at low cost and with fast turnaround
- Minimize the environmental impact in comparison with analog printing by using a little less dyeing material and requiring no water for plate washing.
Reduction of Water Usage
A study1 shows that around 20% of wastewater worldwide comes from fabric dyeing and treatment.
Digital textile printing, compared to analog methods (such as rotary screen printing), eliminates the need for plate washing. Furthermore, pigment-based digital printing requires no post-processing, allowing for a reduction of water usage by up to 97%2, thereby contributing to the reduction of industrial wastewater.
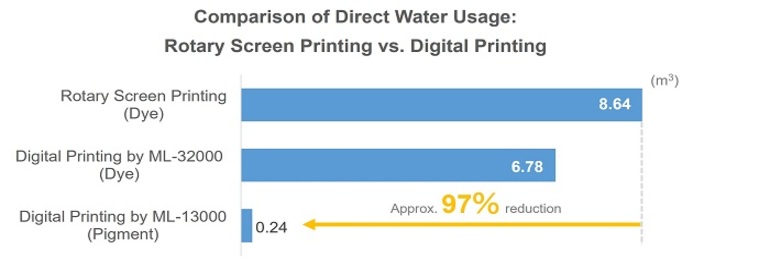
1 World Bank, 2019 How Much Do Our Wardrobes Cost to the Environment?
2 Report on Direct Water Usage in Digital Textile Printing (January 2024), commissioned by Seiko Epson to Furuhashi Environmental Research Institute, a comparison is made between the processes of rotary screen dye-printing and inkjet dye/pigment-printing by Monna Lisa. This comparison examines the direct water usage for dyeing a fabric that is 1.5 meters wide and 300 meters long, noting that these figures may vary depending on the usage environment and measurement conditions.
Efficient Inventory Management
Digital inkjet printing has a short processing time ranging from 3 days to 2 weeks, encompassing all stages from pre-processing to post-processing, making it ideal for small-lot, diverse production. This approach minimizes inventory losses associated with materials, partly-finished products, and finished products, from production through distribution and sale.
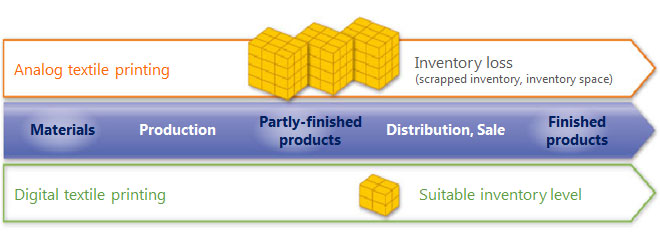
Eco Features
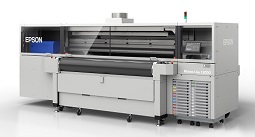
Monna Lisa
- Since the digital textile printing process:
- Is shorter and does not require printing plates, it uses less energy and water than a traditional analog process, and wastes far less ink.
- Is Ideal for small-lot production. Minimizes inventory losses from manufacturing through to sales.
- Digital textile printer inks have acquired Eco Passport certification, indicating that they meet international safety standard for chemical substances of textiles.
See here for a partnership that aims to transform the fashion industry.
An Inkjet Workflow for Brightly Colored Garments with Fineness of Detail
To meet the demand for original printing on cotton products such as T-shirts, polo shirts, and tote bags, we apply our advanced technology cultivated in inkjet printers to achieve vivid and delicate garment printing at low environmental impact cost.
Transforming the Garment Printing Workflow
Traditional silk-screen printing requires extensive preparation, including the production of screens and the mixing of ink, as well as maintenance. For photos and other multicolored prints with gradations, the print process is long, and the longer the process, the more energy, water, materials, and other resources are used.
Digital prints produced with a SureColor SC-F2200 series print digital data from a PC directly onto T-shirts and other garments. So, not only is there no need for screens or plates but images and photos can be reproduced with smooth gradations and in full color. The SureColor SC-F2200 series shortens the garment printing workflow.
Moreover, the inkjet process saves resources and is more environmentally conscious than analog processes because there are no films, screens, or plates to produce, wash, or store.
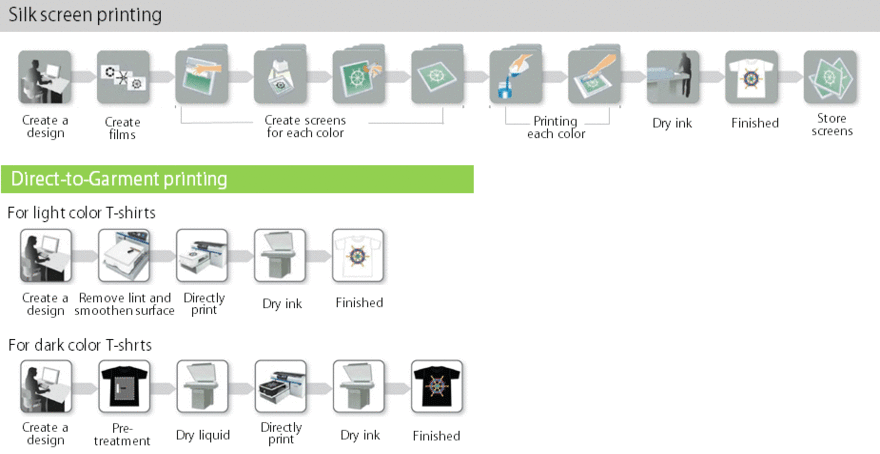
Infant-safe Prints on Textiles
The UltraChrome DG inks and pretreatment liquid used in Epson's garment printers are Eco Passport1 certified and complies with ZDHC MRSL2 level1, indicating that they meet international safety standard for textiles. Under this standard, even printed textiles that directly contact the skin of infants and toddlers are safe. Additionally, the inks are approved with GOTS3.
1繊維製品の生産時に使用する染料・顔料/助剤/仕上加工剤を対象とした化学物質に対する安心・安全の認証規格です。
2繊維製品などの製造工程での意図的な化学物質の使用を禁止する、「製造時規制物質リスト(MRSL)」に基づく分析試験により評価され、ZDHC MRSLガイドラインへの適合を示すものです。ZDHC:Zero Discharge of Hazardous Chemicals
3オーガニックテキスタイルで作られた製品のための国際基準。
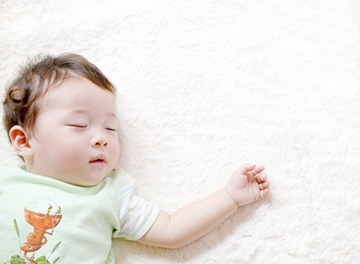
The UltraChrome DG inks and pretreatment liquid used in Epson's garment printers are Eco Passport 1 certified and complies with ZDHC MRSL 2 level1, indicating that they meet international safety standard for textiles. Under this standard, even printed textiles that directly contact the skin of infants and toddlers are safe. Additionally, the inks are approved with GOTS 3.
1 Eco Passport by Oeko-Tex® is a system by which textile chemical suppliers demonstrate that their products can be used in sustainable textile production.
2 The evaluation is based on analytical testing in accordance with the Manufacturing Restricted Substances List (MRSL), which prohibits the intentional use of chemicals in the manufacturing process of textile products and others. It demonstrates compliance with the ZDHC MRSL Guidelines. ZDHC: Zero Discharge of Hazardous Chemicals.
3 An international standard for products made from organic textiles.
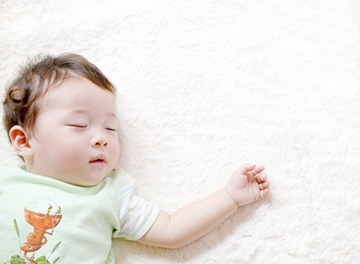
Eco Features
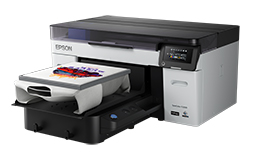
- Streamlined garment printing workflow compared to silk-screen printing.
- Saves resources because no plates or screens are used, unlike traditional printing processes that require a separate film and screen for each color. No washing required, since there are no screens.
- UltraChrome DG ink and pretreatment liquid are certified of Eco Passport.
The Value of Color on Demand
Easily print full-color labels, tickets and tags - where and when users need them and in the quantities required.
Eliminate large inventories of pre-printed labels on demand by printing labels in short runs.
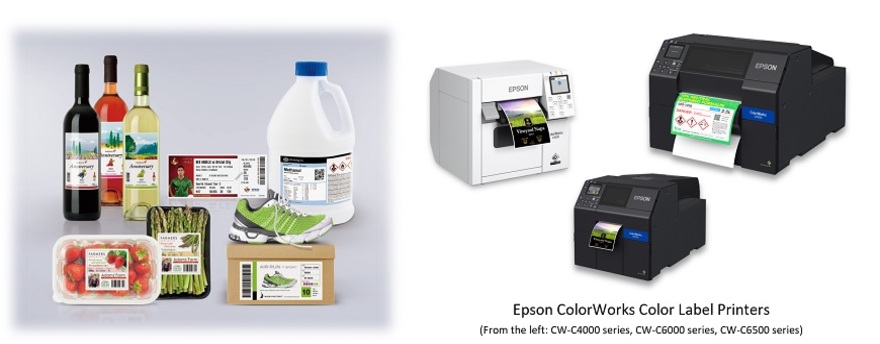
Epson's ColorWorks Inkjet Label Printers Simplify Traditional Processes
Thermal printers were traditionally used to overprint black onto pre-printed labels, but this approach can be slow, disruptive, wasteful and inconvenient.
Epson's range of on-demand color inkjet printers eliminates these issues easily. With the ability to print customized color labels, tickets and tags in-house as and when required, users no longer have to worry about inventory, production downtime, label waste, lost orders or late shipments.
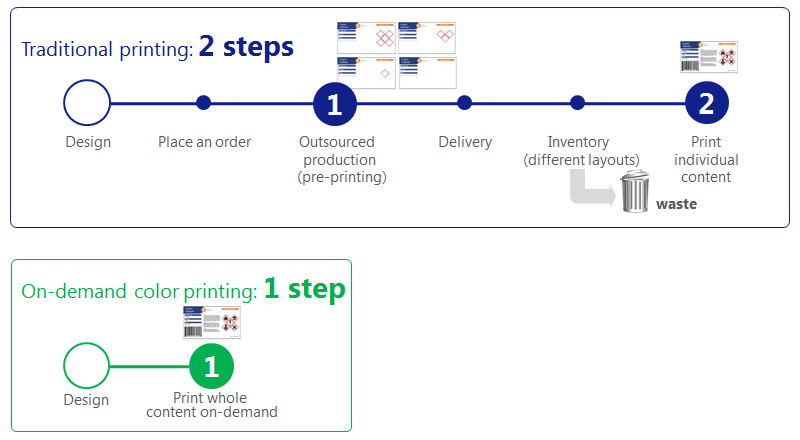
Eco Features
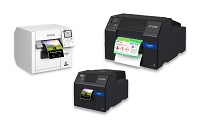
- Simplifying the traditional label printing process, improve inventory management and reduce waste.
- Streamline label production by printing color labels on-demand
- No need to keep an inventory of pre-printed labels
Revamping the Photo Printing Workflow with Inkjet Minilabs
Epson inkjet minilabs are easier to maintain than traditional silver-halide photofinishing equipment. In addition to streamlining the photo printing workflow, they save maintenance costs, help to mitigate resource consumption and reduce the environmental impacts of the printing process.
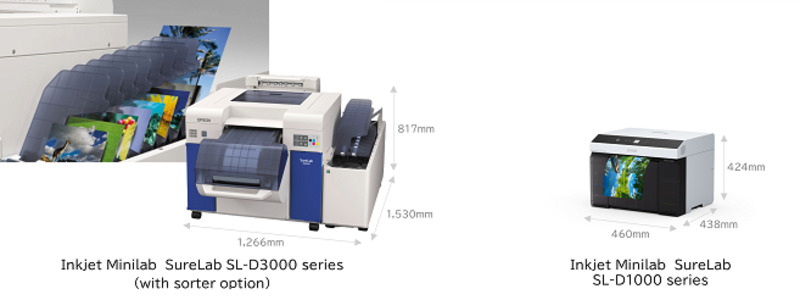
Efficient Photo Printing with Digital Printing
Silver-halide minilabs require chemical adjustment and calibration in the morning, as well as waste fluid processing and cleaning at the end of the day1. The SureLab SL-D3000 series/D1000 series inkjet minilab, however, does not require any special maintenance at startup and shutdown. Inkjet minilabs dramatically improve the photofinishers' work environment because, without chemicals, there is no waste liquid to be processed, no parts to be cleaned, and no chemical smell.
1 According to Epson research.
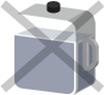
Eco Features
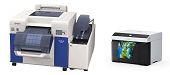
D1000 series
- No chemicals means no liquid waste.
- No washing process means no water hookup is needed.