Environmental technology development
Goal
Developing environmental technology based on societal issues to foster the circular economy
「Epson 25 Renewed」では、社会課題に照らし、4つのマテリアリティを定義しています。なかでも「循環型経済の牽引」においては、材料開発を中心に、地下資源に頼らない資源循環やカーボンマイナスを実現する技術開発に注力しています。このようなマテリアリティ達成に向けた環境技術の貢献とあわせて、積極的にパートナーとの共創も進めながら環境負荷低減に貢献する新たなソリューション開発を行うことで、新たなビジネス創出も同時に目指していきます。
例えば、ドライファイバーテクノロジー(DFT)や金属粉末制御技術などの材料技術により、廃材やリサイクル材から新たな製品を生み出すことで、地下資源から地上資源由来材料への置き換えを実現します。
また、カーボンマイナスの実現に向け、どうしても排出が避けられないGHG残余排出量への対応に向けて、CO2吸収技術を開発しています。
Dry Fiber Technology (DFT)
Closing the resource loop by recycling paper and textile fibers
Dry Fiber Technology is a defibration technology used in Epson's PaperLab dry-process office papermaking systems. We are evolving Dry Fiber Technology and expanding its use in-house to create sound-absorbing and cushioning materials for equipment from used paper. We are also developing new internal applications for cotton mill ends from clothing.
We have also entered into a joint development agreement with the Hong Kong Research Institute of Textiles and Apparel limited (HKRITA) to establish a process for defibrating elastic blended fabrics and tightly woven fabrics. This will enable the extraction of new recycled fibers from functional clothing, sheets, and dress shirts, as well as from factory mill ends, unsold items of clothing, and unwanted apparel.
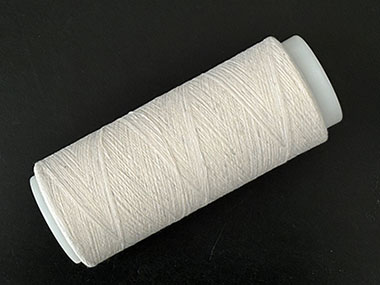
Accelerating the social implementation of composite plastics for a circular economy in collaboration with Tohoku University
Using bioplastics and recycled plastics instead of virgin plastics is crucial for a circular economy. However, bioplastics often have lower mechanical strength and durability than virgin plastic, which limits their usage to certain applications.
Epson has been collaborating with Tohoku University under a comprehensive partnership agreement since 2006, engaging in systematic research and development as well as talent cultivation through industry-academia cooperation. Joint research on fiber-reinforced plastics, based on Dry Fiber Technology, is one of the efforts. In August 2023, the establishment of the "Sustainable Materials Co-Creation Research Institute" aims to accelerate research and development, as well as social implementation, of foundational technologies for cellulose fiber-reinforced bioplastics and recycled plastics, which serve as sustainable materials to drive the circular economy.
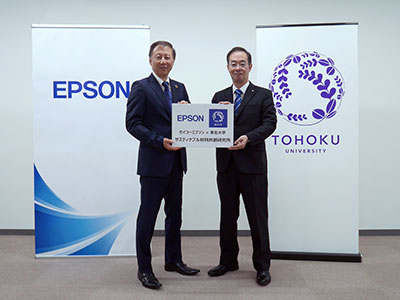
The development of composite plastics using defibrated cellulose or fabric has been adopted as a sub-project under the "Construction of a Circular Economy System," which is part of the Cross-Ministerial Strategic Innovation Promotion Program (SIP)1 Phase 3, led by the Cabinet Office. (July 2023)
1 A national program led by the Council for Science, Technology, and Innovation (CSTI) aims to achieve scientific and technological innovation, transcending the boundaries of ministries and conventional fields.
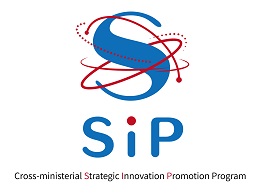
Related link
CO2 Absorption Technology
Epson aims to establish CO2 absorption technologies that can offset its own residual CO2 emissions in pursuit of carbon negative, as outlined in its Environmental Vision 2050.
CO2 separation membrane based on Epson's proprietary technologies
Epson is developing separation membrane that preferentially transmit CO2 based on several proprietary technologies, such as thin film technology from inkjet heads. In the future, we aim to achieve high-efficiency CO2 capture with compact, low-energy systems.
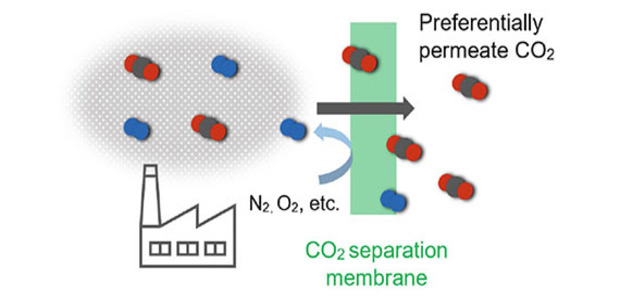
Biological carbon fixation
★要確認★by microalgae CO 2 We are working to develop absorption technologies. Currently, CCS *2 In the laboratory, we focused on calcium carbonate-synthesizing coccolithophytes, and by optimizing culture conditions and using various breeding techniques, we were able to develop a forest *3 is 70 times higher than that of CO 2 We have succeeded in raising it to a fixed amount. In addition, the CCU *4 to develop technologies using green algae. In the future, we plan to develop more efficient CO 2 fixation, and CO 2 We even aim to convert the resources of the
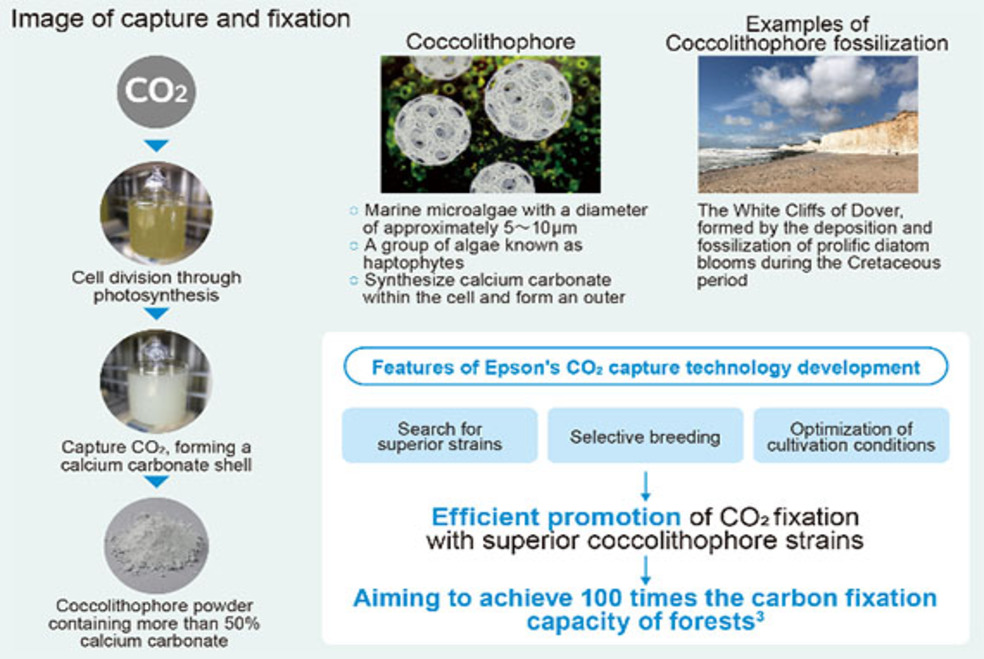
Epson is working on the development of CO 2 Currently, we are focusing on coccolithophore, which synthesize calcium carbonate, for CCS 2. Through the optimization of cultivation conditions and the utilization of various breeding technologies, we have succeeded in increasing CO 2 fixation in our lab to 70 times that of forests 3. Additionally, for CCU 4 In the future, we aim to more efficiently fix CO 2 and even pursue its utilization.
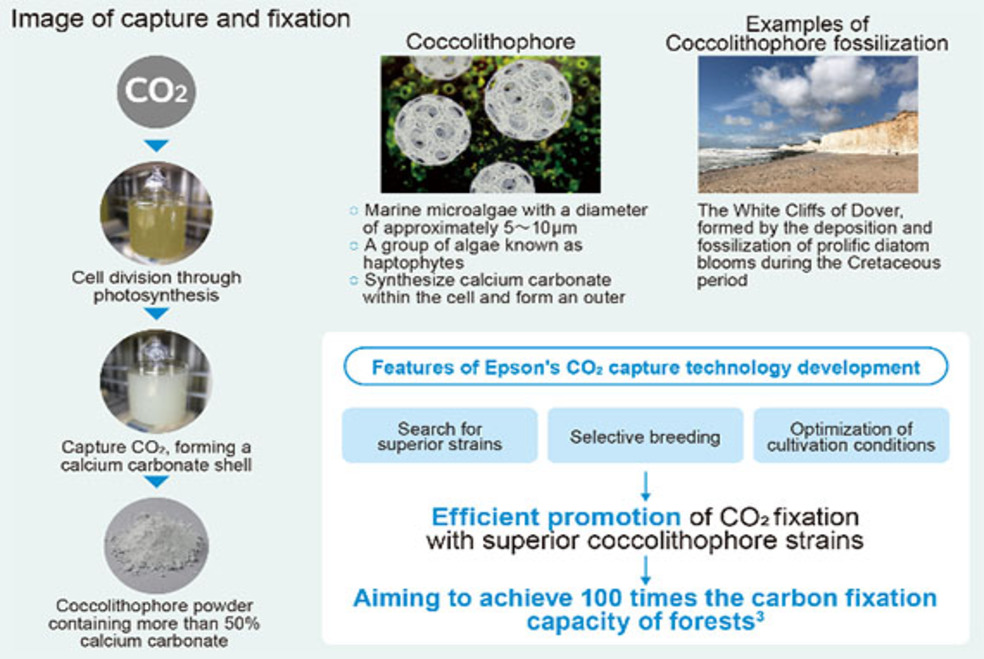
2 CCS (Carbon dioxide Capture and Storage): Capturing CO2 emitted from power plants, factories, etc., and storing it somewhere, such as underground
3 Calculation is based on the data from the Forestry and Forest Products Research Institute (FFPRI), Japan
4 CCU (Carbon dioxide Capture and Utilization): Capturing CO2 emitted from power plants, factories, etc., and utilizing it such as direct use for the agricultural or for fuel production
Metal Powder Manufacturing Technology
Recycling Metal Materials in the Epson Group with Original Metal Powder Manufacturing Technology
Epson Atmix Corporation is using its metal melting and atomizing process technologies to produce metal powder products. In February 2020, the company began taking silicon wafers that were used in Epson's semiconductor fabrication business and producing metal powder from them. This reuse of wafers reduces Epson's waste, CO2 emissions, and use of underground resources such as virgin silicon. By the end of the 2021 fiscal year, Epson Atmix had recycled 8.5 tonnes' worth of silicon wafers. The company will continue to search for other materials that could potentially be upcycled into high-performance metal powders.
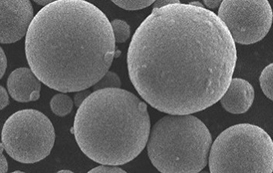
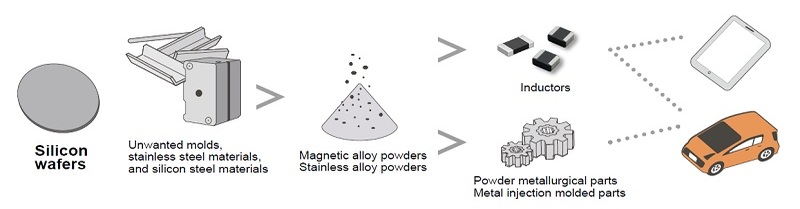
不要な金属を原料として資源化する金属精錬工場を建設開始
エプソンアトミックスは、金属の資源循環を実現する金属粉末製造を確立するために、グループや市中などにおいて不要となった金属を、金属粉末製品の原料として再生する新工場を建設しており、2025年6月の稼働を目指しています。
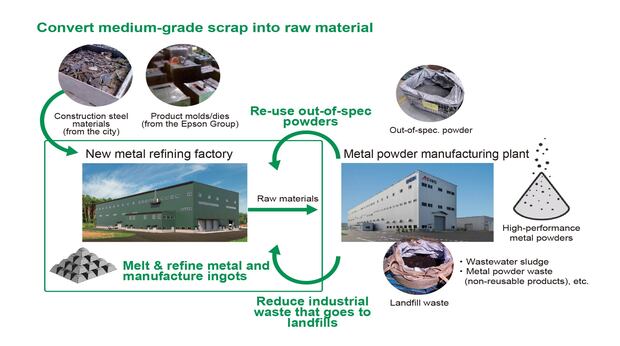