Internal Control System
- Group Governance
- Compliance and Risk Management
- Risk Management
- Supply Chain Business Continuity Management
- Internal Audits
- Internal Controls over Financial Reporting
The entire Epson Group embraces “the Epson Way”, which was founded on Epson’s Management Philosophy. Epson also established “the Basic Internal Control System Policy” to help ensure that operations across the Group are conducted appropriately in line with the Epson Way, and Seiko Epson is committed to steadily improving the overall level of the Group.
Group Governance
The Epson Group is managed based on the concept: global consolidated responsibility of product-based divisions; and global responsibility of the Head Office supervisory functions. The head of the business operations divisions take the responsibility for the business execution systems of subsidiaries. And the head of Head Office supervisory sections take the responsibility for Group-level corporate functions. With this system, Epson strives to streamline operations throughout the Epson Group, including subsidiaries.
Compliance and Risk Management
Epson's goal is to continuously create value that exceeds customer expectations while building trust with all stakeholders based on the "Epson Way." To maintain and strengthen this trust, Epson seeks to increase management transparency and fairness and effectively manage compliance through faster decision-making. There were no legal or regulatory violations subject to disclosure in FY2023, nor were there fines or settlements subject to reporting in audited financial statements.
Compliance Organization
As an advisory body to the Board of Directors, the Compliance Committee is made up of six outside directors and one director who is a full-time member of the Audit & Supervisory Committee. It is chaired by the full-time member of the Audit & Supervisory Committee, and supervises and monitors business affairs by discussing important compliance activities and making reports and suggestions to the Board of Directors. The Chief Compliance Officer (CCO) supervises and monitors the execution of all compliance operations and periodically reports the state of compliance affairs to the Compliance Committee. Under the supervision of the president, the compliance control department globally promotes and enforces compliance in cooperation with businesses and subsidiaries. It monitors compliance in general and, if necessary, makes corrections and adjustments to enhance the completeness and effectiveness of compliance activities.
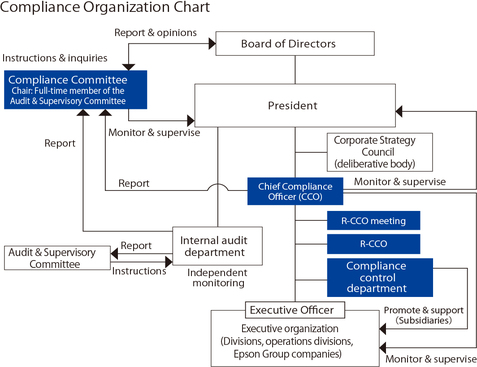
Whistleblowing Systems and Reporting Channels
Epson provides reporting channels to obtain information from officers, regular employees, contract employees, and temporary workers to quickly call our attention to potential compliance problems that might go undetected. We set up a process for escalating reports of concern. The basic rules for whistleblowing systems, such as the need to strictly manage information contained in reports, forbid reprisals against whistleblowers, and protect anonymity, are set forth in Principles of Corporate Behavior and the Epson Group Whistleblowing Systems Regulation. Seiko Epson and all the Group companies, including in the Americas, Europe, China, and Southeast Asia, provide reporting channels based on them. Whistleblowing systems comply with the laws and regulations of each country and region, including, in Japan, the Whistleblower Protection Act. They are available in Group companies in their local language.
Reporting channels are prescribed in the Epson Global Code of Conduct and accessible on the intranet. We inform officers, employees, and temporary workers about the channels and urge their use through Compliance Month activities every October and online courses.
In addition, Seiko Epson and all Epson Group companies around the world have set up supplier whistleblowing systems to receive reports from suppliers and other external business partners. In April 2025, Seiko Epson also opened a Global Stakeholders Hotline to accept reports from all stakeholders.
As with Epson's internal reporting channels, the information contained in reports is strictly protected, reprisals against whistleblowers are prohibited, and anonymity is ensured.
Suppliers and other external business partners are notified about supplier whistleblowing systems in written supplier guidelines and at supplier conferences and are encouraged to use them.
Whistleblowing system use and reports received in the Epson Group are reported regularly to the Board of Directors, Audit & Supervisory Committee, Compliance Committee, and Corporate Management Council. The identity of whistleblowers is kept confidential.
Supplier Whistleblowing System
Global Stakeholders Hotline
Human rights-related inquiries and reports are handled as described below.
Directors, employees, and dispatch workers can use the Epson Helpline or several other reporting channels and advisory services to report or consult regarding diversity issues and so forth.
Suppliers and other external business partners can use a supplier whistleblowing system to lodge reports.
All stakeholders can seek engagement and remedy by filing grievances via a grievance handling platform provided by the Japan Center for Engagement and Remedy on Business and Human Rights (JaCER).
See here for more information about using the JaCER platform
Support System in Japan
Epson has set up three types of Epson Helpline reporting channels. One type is operated internally. The second is operated by a third-party provider. And the third is operated by an external lawyer. Officers, employees, and temporary workers in domestic Group companies can use any type of channel to report their concerns. Instructions for using Epson Helplines are provided in a user manual posted on the company intranet. Trainings and other opportunities also cover helpline use. Reports can be lodged by e-mail or phone 24 hours a day, 365 days a year. We investigate reports from whistleblowers and take corrective action as needed. We have been taking the initiative in developing the whistleblowing system since establishing the first reporting channels for employees and temporary workers in conjunction with the enforcement of the Whistleblower Protection Act in 2006. In compliance with the amended Whistleblower Protection Act that came into force in June 2022, we have designated personnel to handle whistleblowing reports and have been addressing reports from employees and dispatch workers within one year after leaving the company. We actively develop, improve, and implement systems based on the latest social and regulatory trends that are identified from things such as evaluations by an external consultant.
In the 2024 fiscal year, our reporting channels in Japan received 144 reports, an increase of 1 over the previous fiscal year. Whistleblowers reported possible cases of internal rule violations, misconduct, and lawbreaking. Epson responded appropriately to each of these reports. Aside from Epson Helplines, we set up advisory services for specific concerns for officers, employees, and temporary workers. This helps us to maintain and operate an environment that makes it easier to seek advice.
Counseling and Support Services in Japan
Harassment counseling | Management advisory service | Counseling related to overwork and long working hours |
Career counseling | Diversity counseling | Women's health counseling |
Employee counseling | Corruption (bribery) regulations & Competition laws advisory service | Insider trading advisory service |
Support System Outside Japan
All overseas Group companies, including in the Americas, Europe, China, and Southeast Asia, have set up reporting channels that allow officers, employees and temporary workers to report. Each reporting channel complies with local laws and regulations. Information contained in reports is strictly protected and reprisals against whistleblowers are prohibited. Reports may be made anonymously.
We have also introduced an Epson Executive Compliance Hotline, a global reporting system that Epson uses to directly receive compliance-related reports involving executives in subsidiaries outside Japan. The system helps us to improve the completeness and effectiveness of the reporting system in the Epson Group.
Risk Management
The president of Seiko Epson acts as the chief risk management officer in the Epson Group, including subsidiaries. Group-wide risks are globally managed by Head Office supervisory departments with the cooperation of the operations divisions and subsidiaries. Risks unique to an individual business are managed by the chief operating officer of that business, including at subsidiaries consolidated under them. The Seiko Epson risk management department monitors overall risk management in the Epson Group, makes corrections and adjustments thereto, and ensures the effectiveness of risk management programs.
The risk management organization is defined in the Epson Group Risk Management Basic Regulation.
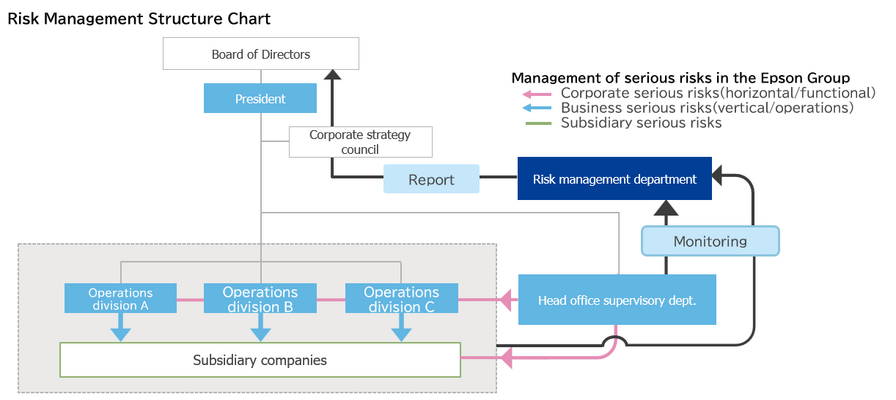
Epson identifies business operations risks, business ethics risks, such as participation in bribery and cartels, and other serious risks that could materially impact the company. Epson evaluates these risks using The Committee of Sponsoring Organizations (COSO) and ISO 31000 as guides and sets priorities.Risks that could have serious adverse effects on Epson Group management are considered to be serious corporate risks. Risks that could have serious adverse effects on business operations are considered to be serious business risks. Risks that could have serious adverse effects on subsidiaries' management are considered serious Group company risks.
Epson drafts and executes plans to control these serious risks and periodically monitors plan progress. The company also strives to ensure control plan effectiveness by evaluating serious Group-wide risks every quarter, evaluating serious business risks and serious Group company risks every six months, and revising the plans as needed. The president of Seiko Epson reports important risk management affairs to the board of directors quarterly.
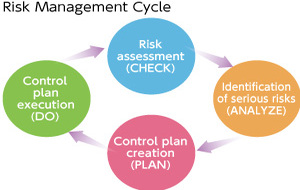
Crisis Management
At Epson, we maintain a standing crisis management program to enable us to quickly address emergent risks that could have a significant impact on Group management. This program provides for a Crisis Management Committee chaired by the president and vice-chaired by the general manager in charge of risk management, and initial response procedures are in place to handle crises.
In the event of a crisis, the general administrative manager of the corporate department responsible for that particular crisis class directs the response, and an organization that reports directly to the committee chair is invoked to enable rapid decision-making.
The crisis management program includes response programs for each crisis class, with specific initial response procedures tailored to the nature of the anticipated risks. The stakeholder organizations work together to quickly analyze and come to grips with the situation, devising countermeasures to prevent or limit damage. When necessary, Epson engages external entities such as lawyers, consulting firms, and government authorities to ensure that risks are thoroughly and effectively addressed.
Once the situation stabilizes, the crisis management organization is disbanded. However, ongoing recovery steps, recurrence prevention measures, and knowledge transfer across the Group are monitored within the risk management cycle. These efforts are regularly reported to the management team, including outside directors, at board meetings. Furthermore, they are reflected in revisions to the crisis management program and in risk control initiatives, thereby enhancing the company’s ability to respond to future crises..
The activities of the Crisis Management Committee are regularly reported to executive management, including outside directors, through meetings of the Corporate Strategy Council and Board of Directors.
Supply Chain Business Continuity Management
The Epson Group formulates a business continuity plans (BCPs) to ensure that we fulfill our responsibility to supply products and services and to minimize losses in the event of a disaster, accident, outbreak of emerging infectious disease, or other disruption in the supply chain. Epson also implements supply chain business continuity management (BCM) to properly maintain and improve the BCPs.
Supply Chain BCM
Supply chains are becoming increasingly sophisticated and complex. Epson's basic approach to establishing supply chains that are more resilient, sustainable, and resistant to the risks and contingencies that today’s supply chains face is to geographically distribute functions, secure alternative sources, and increase resilience. We have divided supply chain functions into five categories (suppliers, procurement, production, sales, and logistics) and are addressing the priorities that have been set for each.
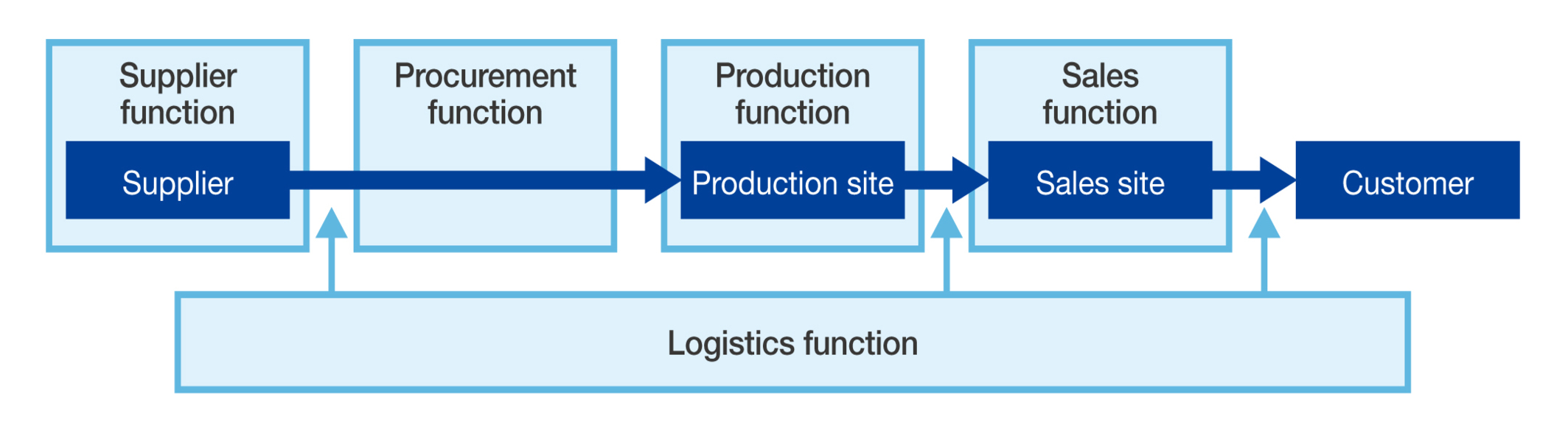
Functions | Initiatives |
---|---|
Suppliers | Acting on suppliers to enhance their own supply continuity capabilities by establishing business continuity management (BCM) and a business continuity plan (BCP) |
Procurement |
Multi-sourcing, securing alternative sources for procured goods, executing long-term procurement contracts, strengthening partnerships, and maintaining inventory of parts and raw materials * Applies to direct materials and parts and to indirect materials |
Production | Strengthening the distributed production organization, increasing the resilience of facilities, strengthening measures to prevent the spread of infectious diseases, and securing product inventories |
Sales | Maintaining operations sites, human resources, and an IT backup system |
Logistics | Securing space on ships by strengthening relationships with shipping companies, improving the accuracy of shipping plan management, and securing multiple logistics modes and methods (carriers, transportation routes, and warehousing functions) |
Schematic Diagram of the BCP
The vertical axis on this graph shows the operating level while the horizontal axis is recovery time. In an emergency, the operating level declines and stays at that level for a period of time. However, implementing actions in the BCM enable a business to keep the operating level as high as possible even in an emergency or enable it to quickly restore operations in the event of a shutdown.
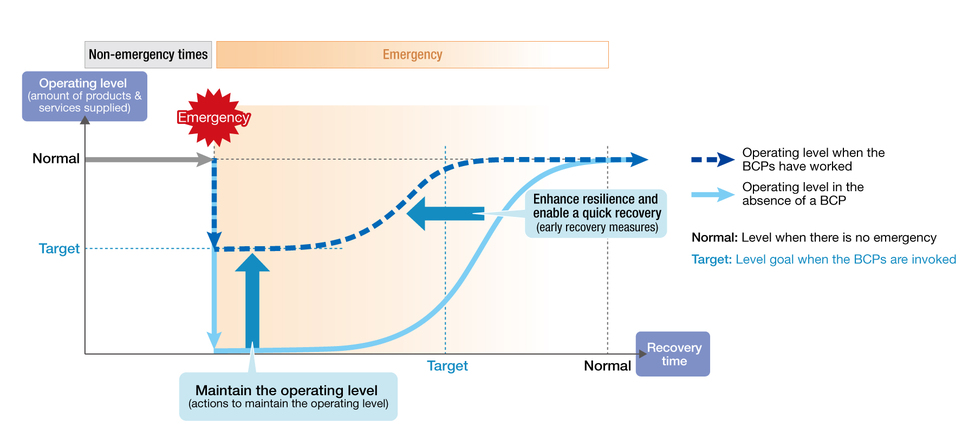
Responding to Supply Chain Risks
Since 2019, the risk of supply chain disruptions due to events like the spread of infectious disease, global chip shortages, and shipping container scarcity has been far greater than assumed. Moreover, risks in the business environment that threaten supply chains, including the outbreak and protraction of regional conflicts as well as geopolitical and disaster risks, have not been resolved. If anything, they have increased in magnitude and scope. Supply chains are becoming increasingly sophisticated and complex.
Epson's basic approach to establishing supply chains that are more resilient, sustainable, and resistant to the risks and contingencies that today’s supply chains face is to geographically distribute functions, secure alternative sources, and increase resilience. Epson is addressing these risks by taking the actions described below in the five supply chain functions.
- Suppliers
We need our suppliers to strengthen their own supply continuity capabilities, so we ask them to put business continuity management (BCM) arrangements in place and to formulate a multifaceted action plan (BCP) to respond to contingencies so that they can minimize damage and losses should there be a disruptive event in the supply chain. - Procurement
We are gathering more in-depth supply chain information and enhancing our ability to detect risks. Furthermore, we will implement effective, practical procurement risk avoidance measures (preventive measures) to ensure stable material procurement.
We will secure multiple sourcing options, expand the evaluation of alternative products, keep BCP inventory, and strengthen relationships with partners to achieve these objectives. - Production
In preparation for future outbreaks of infectious disease, we have established preventive guidelines to protect our employees–our top priority–and to minimize the impact on production.
To fulfill our product supply obligations, we are moving toward geographically distributed production. We are also increasing the resilience of all our production facilities, particularly the domestic Japanese factories responsible for manufacturing the core components of each of our businesses. - Sales
We will establish sales and distribution guidelines and will specify the required level of prevention to shield the sales function from the impact of contingencies that arise. To meet our product supply obligations, we will operate in line with the sales and distribution guidelines. - Logistics
In addition to further strengthening partner relationships, we will increase the visualization of logistics, improve the communication and coordination of information between production sites and sales sites, and deliver goods to meet the demands of our customers.
We will diversify the means and modes of distribution, including transport routes, ocean and air freight, and warehouse facilities. Additionally, we will continue to improve product loading efficiency in all businesses, mitigate logistics risks, improve logistics efficiency, and minimize environmental impact.
Internal Audits
The internal audit department conducts audits in accordance with a code of conduct to check for compliance and corporate ethics violations and to facilitate self-directed internal control at all Group divisions as well as subsidiaries and related organizations in Japan and overseas. Audits are used to check compliance and the effectiveness and efficiency of these units' risk management, internal controls, and governance processes. If problems are found, the internal audit department helps minimize business risks by conducting a follow-up audit to check the status of improvements. To ensure effective Group governance, the internal audit department also centrally oversees internal audits throughout the Group in collaboration with auditing departments at regional headquarters in Europe, the Americas, China, and Southeast Asia.
Each year, the units to be audited are chosen by assessing the risk at each division and each subsidiary and related organization in Japan and overseas. Then an auditing cycle is set that is designed for effectiveness and efficiency. Audits are then performed systematically. In the 2024 fiscal year, the internal audit department audited 17 business units and provided them with concrete advice on correcting 37 observed nonconformities. In the 2025 fiscal year, business units were grouped into 82 organizations. The internal audit department conducted risk assessments on the groups, selected the units to be audited, and is performing the audits.
Internal Controls over Financial Reporting
Every year, we audit internal controls to ensure the reliability of financial reporting (J-SOX). The Epson Group uses an autonomous distributed implementation system in which operations divisions and subsidiaries subject to external audits conduct a self-assessment on the design and operation of their internal controls, while the J-SOX Compliance Department ensures the validity of the assessment results. Operations divisions, subsidiaries, and affiliates not subject to external audits are required to independently assess their internal controls and make such improvements as are necessary.