Occupational Health and Safety
- Approach to Occupational Health and Safety
- Safety Management Initiatives
- Fire and Natural Disaster Safety
- Facility Safety Maintenance
Approach to Occupational Health and Safety
At Epson, safety, health, and compliance take precedence over performance. We believe that initiatives to promote a healthy and safe work environment and to protect the physical and mental wellbeing of our people are essential for a healthy company. We are thus carrying out occupational health and safety activities around the globe to ensure that all workers in the Epson Group can enjoy work in the knowledge that they are safe.
Epson has established a Basic Occupational Health and Safety Policy that is founded on the four pillars of safety, health, fire and disaster management, and facilities, and we make officers, employees, and our partners aware of our occupational health and safety (OH&S) activities.
Epson Group Basic Occupational Health and Safety Policy
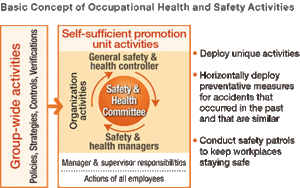
Epson is evolving the Group's OH&S activities to align them with ISO 45001, thereby further improving the workplace health and safety environment. Bearing in mind that safety, security, and health are the lifeblood of the company, we will comply with all applicable local and international laws and regulations as well as with company rules. We will strive to maintain and promote both mental and physical health. Together, we will work as one to achieve our goals of zero serious occupational accidents and industrial incidents and zero occupational illnesses, thereby laying the foundation for achieving sustainability and enriching communities.
Yoshihiko Kubota
Overall Health and Safety Controller
Deputy General Administrative Manager, Human Capital & Well-Being Management Division
Occupational accident situation
2023年度は重大労働災害*1が0件でした。活動により激突・激突されは12件が3件へ減少しましたが、転倒は18件から21件へ、動作の反動、無理な動作は3件から10件へ増加しました。2022年度から製造に加えて販社を含めた指標管理にあらため、労働安全衛生活動を強化しましたが、販社における労働災害は、倉庫作業による腰痛、オフィスでの転倒など、増加傾向を示しています。販社を含めた全推進体を対象とした労働安全衛生の会議を通じて、再発防止活動を継続して展開しています。
火災に繋がる、発火・発煙は3件から5件に増加しています。要因となっている購入備品(扇風機、食器乾燥機など)の管理を強化していきます。
労働災害度数率・強度率*2は昨年から微増となっていますが、全国平均を下回る水準で推移しています。
*1 死亡・後遺障害およびこれに準ずる災害
*2 労働災害に関する指標で、厚生労働省の計算式に準じて、算出
*2 労働災害に関する指標で、厚生労働省の計算式に準じて、算出
労働災害度数率推移 労働災害強度率推移
Workdays lost are calculated based on the criteria below.
・Fatality: 7,500 days
・Permanent total disability: 7,500 days for physical disability levels 1–3
・Permanent partial disability: 50 to 5,500 days depending on disabilitylevels 4 to 14
・Temporary disability: The total number of lost days, including designated holidays, is multiplied by 300/365
Number of Occupational Accidents, by Type, in FY2023
(Unit: Accident)
Falls | Reaction to motion, over-exertion |
Fire & smoke | Collisions | Cuts, scrapes | Other | Total |
---|---|---|---|---|---|---|
21 | 10 | 5 | 3 | 2 | 7 | 48 |
* The count only includes accidents that resulted in the loss of one or more work days.
Safety Management Activities
After reviewing the results from FY2023, we set the targets for FY2024 as follows:
Indicator | FY2023 Target | FY2023 Results | FY2024 Target |
---|---|---|---|
Serious occupational accidents & industrial incidents | Zero | Zero | Zero |
Occupational accident frequency rate | ≤ 0.30 | 0.32 | ≤ 0.30 |
Occupational accident severity rate | ≤ 0.006 | 0.007 | ≤ 0.006 |
Actions for FY2024
Based on an analysis of occupational accidents that occurred in FY2023, we will focus on the activities below in FY2024 to prevent the same or similar accidents from recurring and preemptively avoid other accidents.
- Falls: In addition to making environmental improvements to staircases and eliminating trip hazards, etc., we will try to eliminate falls by helping employees to improve or maintain their physical fitness.
- Reaction to motion & over-exertion: To address lower back injuries and other injuries that occur when transporting objects or when performing continuous physical tasks, we will better identify risks associated with physical stresses through on-site observation and take corrective action.
- Fire and smoke: In response to incidents involving general household appliances, we will enhance pre-purchase specification checks and regular inspections.
When introducing new machinery or equipment, including during the research and development stage, we identify and assess risks in accordance with the Group's risk assessment criteria. We then implement safety measures based on the findings.
ISO 45001 certification acquisition situation
To protect employees from occupational health and safety risks, Epson manufacturing companies as well as some other sites have been systematically working to obtain ISO 45001 certification, the international standard for OH&S management systems, over a three-year period. By the end of FY2023, 12 out of our 14 manufacturing sites in Japan and all 14 of our overseas manufacturing sites have obtained ISO 45001 certification, making for a certification rate of 92.9% (26/28). The remaining two sites will earn certification this fiscal year.
Global sharing of OH&S activities information
Epson production sites in Japan and abroad regularly hold meetings between management and operational staff and between labor and management to share information and level up their OH&S activities.
At the management level, the senior executives and Epson Group company presidents who head up health and safety programs at Epson sites in Japan gather twice a year for a General Health & Safety Controllers’ Meeting in which the director in charge participates. The same thing happens separately overseas. These meetings are used to discuss the current situation and challenges faced in occupational health and safety and to work on improvements.
At the labor-management level, members of the labor union and management convene monthly Health and Safety Committee meetings to gather ideas and feedback from workers that can be used to improve site health and safety.
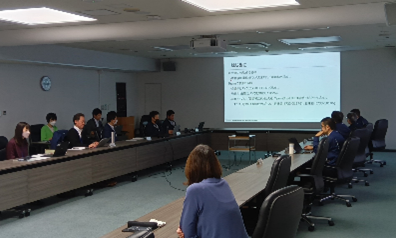
A February 2024 general health and safety controllers' meeting in Japan
Building awareness internally through Safety News bulletins
Epson analyzes all occupational accidents and industrial incidents in the Epson Group, identifies causes, and implements measures to prevent similar incidents. Information on occupational accidents and industrial incidents—including causes, countermeasures, and recurrence prevention measures—is compiled into "Safety News” bulletins and disseminated to all employees through the company intranet.
Human resource development through health and safety education
Epson considers its comprehensive health and safety education courses to be among the most important in its education program. A key feature of the program is that the curriculum is tailored to the different echelons and roles of employees. For general employees, we focus on practical training in things such as risk assessment and hazard prediction. For management and supervisory staff, the emphasis is on acquiring skills to lead the workplace. This approach is integrated into the company-wide education curriculum.
In FY2023, we provided online safety education courses. These courses were completed by 19,697 employees, or 97.97% of the workforce. Outside Japan, 27,336 employees completed the courses.
We keep track of, and follow up with, those who have not completed the courses.
Fire and Natural Disaster Safety
Epson has in place a Group-wide plan to control priority risks. We regularly review and update the plan and conduct drills based on it to prepare for fires, earthquakes, and wind and flood damage. These disaster drills are designed to preserve life, minimize damage, and enable a recovery. We test their effectiveness and take steps to further improve them.
Initial disaster response
In the event of a disaster or the threat of one, Epson Group companies and business sites, both domestic and international, invoke a disaster task force to direct a response. After invoking the task force, they immediately report the situation to the Seiko Epson Head Office disaster task force administrative office. This first report includes information on the following:
- personnel safety;
- damage to buildings, equipment, and facilities;
- impact on operations; and
- any other information that the disaster task force chief deems necessary.
To gather information about disaster situations and to ensure that information is transmitted even if infrastructure is disrupted, we have set up multiple channels to receive reports from both domestic and international sources. We have also set up a Microsoft Teams channel connecting Seiko Epson’s Head Office disaster task force administrative office with disaster response personnel at all domestic sites, enabling timely sharing of information and images via smartphones.
We have put in place a system that enables us to verify the safety of our people and to provide information not only at the Group-wide level but also at the local site level, thereby enabling us to respond to local disasters.
The Head Office disaster task force administrative office reviews site reports and sets up a central disaster task force if the damage is extensive or wide-spread or if an affected site asks it to do so. The central disaster task force assesses the situation at each site, issues comprehensive guidance to each disaster task force, and provides prompt support and actions for a recovery. It also compiles recovery prospects and announces them both internally and externally. Once the disaster task forces have completed their initial response, a swift transition to the business continuity plan (BCP) is made.
Disaster preparedness
Many Epson sites in Japan and abroad have their own fire brigades. They regularly conduct drills to prepare them to take the lead in providing aid and minimizing damage to facilities and equipment in the event of a fire. Moreover, all employees undergo training in the use of fire extinguishers to prepare them to fight fires in the incipient phase.
Each site also prepares for other disasters by identifying risks based on local hazard maps and developing drill plans accordingly. All employees participate in drills in which they evacuate buildings or extinguish fires in accordance with a simulated workplace disaster scenario.
In terms of organizational structure, we have put in place initial response guidelines for the entire Epson Group. These guidelines are regularly reviewed and updated, and Group companies and sites integrate these guidelines into their own processes to establish a system that works best for them.
See here for preparations in response to emerging infectious diseases
Facility Safety Maintenance
Epson maintains safe facilities in line with the Epson Group Basic Occupational Health and Safety Policy to prevent accidents caused by faulty buildings, equipment, and facilities.
Facility safety maintenance covers all domestic and foreign Epson Group buildings and building equipment, including but not limited to electrical equipment, air conditioning and sanitary equipment, drainage equipment, disaster management equipment, communication equipment, and equipment for supplying gas and chemicals to production machinery. Maintaining the soundness of buildings and building equipment, planning and maintaining them to minimize damage from fires and earthquakes, and ensuring the safety of employees and others will help Epson to ensure business continuity and deliver products and services on time. Epson thus has in place a variety of facility safety measures.
For example, before a new building or new building equipment is constructed, installed, refurbished, or removed, a safety assessment is conducted to identify potential problems and improve designs. In addition to managing safety during construction, we also conduct safety assessments prior to use to verify that buildings and building equipment were constructed or installed as designed. If there is a problem, we have it fixed, and if it is not fixed, the building or equipment cannot be used until the problem is resolved.
In addition to ensuring compliance with applicable laws, regulations, and codes when conducting safety assessments, we are also working to build safer buildings and building equipment by establishing our own standards and preventing the recurrence of past accidents and problems.
In many cases, we enlist the cooperation of outside partners to do the actual construction work. When we hire a partner, we carefully manage safety by communicating the construction rules, controlling access to the site, ensuring that confidentiality is maintained, and providing instructions for working safely. We also try to raise safety awareness among our partners by holding safety conferences.
To encourage employees to acquire the licenses and qualifications needed for facility management and to maintain and raise the level of facility management, Epson provides employees with ongoing professional education. To help ensure electrical safety, Epson created its own program for training and qualifying electrical equipment technicians. Only qualified technicians are allowed to perform electrical work and maintenance on machinery used at Epson sites worldwide.
We at Epson will continue to try to eliminate occupational accidents through activities like these.