Human Resource Development
- New Initiatives for Human Resource Development
- Training Initiatives
- FY2023 Workforce Composition and Training Data
New Initiatives for Human Resource Development
Epson aims to be a company where people autonomously form careers and continue to develop over the long-term. We will achieve the business targets we have set forth in Epson 25 Renewed and support our company’s development by raising the ability of each of our employees to respond to changes. That will then lead to the building of sustainable and enriched communities.
Epson has re-examined our education and training system from this perspective. We have begun three new initiatives based on the opinions of our business entities and feedback from our employees.
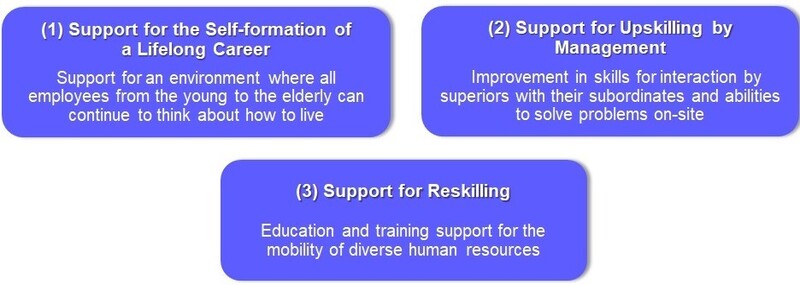
(1) Support for the Self-formation of a Lifelong Career
Epson continuously implements initiatives aimed at being an organization that promotes personnel development. We provide support toward building motivating and challenging careers that encourage growth. To help our employees set their own medium- and long-term career goals, we have been offering Lifetime Career Support (LTCS) since FY2016. LTCS provides age- and grade-specific training which gives employees an opportunity to independently plan their own career path. We have expanded the system to include LTCS40, LTCS50 and also the Introduction to LTCS Course for employees who have just joined the company.
●Number of Participants in FY2023
LLTCS50 Training (for all employees age 50): 307 participants (total up to FY2023: 2,903 participants)
LTCS40 Training (for all employees age 40): 186 participants (total up to FY2022: 1,881 participants)
Introduction to LTCS Course (given in new employee training): 344 participants
In FY2023, we launched LTCS A30 for employees in their 30s and LTCS50up with a view to rehiring employees up to age 70. By providing employees with an opportunity to continue thinking about their careers at each age milestone, we help them to overcome various career challenges and to shape their own careers.
Interviews with third-year employees
The Human Resources Department interviews young employees who joined the company right out of school and are in their third year with the company to help them quickly improve their effectiveness and to encourage retention. The goal is to enhance the engagement of individuals with their work and workplace by listening to their concerns regarding their job, work environment, and personal career development, and by providing support, including within the workplace.
(2) Support for Upskilling by Management
Management and communication by superiors in the workplace play an extremely important role for employees to work and grow dynamically. Questionnaires have made it clear that many managers, especially those with little experience, are concerned about this point. Accordingly, we have newly introduced 1-on-1 communication training. Moreover, in addition to existing new section manager training, we have launched follow-up training after employees are promoted to the level of section manager. That means we have set up opportunities for section managers to share information, think and learn from each other.We also partner with outsiders to provide materials for learning management skills.
(3) Support for Reskilling
To support employees’ desire to build their careers and continuously grow, as well as to improve their skills and ability to respond to changes, we have been creating a reskilling program that is designed with the following three main objectives: (i) raise the level of all employees by helping them obtain the minimum digital knowledge and use it in their own work, (ii) provide an opportunity for re-learning knowledge specific to a product or business and for education in specialized fields such as digital transformation to accelerate personnel assignment and rotation to priority areas and new areas, and (iii) establish an environment that provides opportunities for learning and improving skills to accommodate employees’ desire to learn and encourage them to apply for jobs inside the company by using the internal recruitment system.
Initiative to Expand Rotation
Epson places importance on job rotations that expand the range of the abilities, experience and knowledge of individuals. One aim of rotation is for each employee to shape their career and continue to grow and improve their ability to respond to change. The other aim is to contribute to the effective and efficient operation of the value chain. However, people were not rotating to new jobs as much as expected in the past. So, to encourage people to seek new opportunities in-house, we eliminated the need for approval by a superior when using the internal recruitment or job challenge systems. We also incorporated rotation as a requirement for promotion, filled vacancies left by personnel who transferred to a new job, and added rotation to managers' performance appraisal. We are also reinforcing our reskilling program to support rotation.
Going forward, we will promote rotation while giving consideration to workplaces and support for persons transferred.
Rotation Rate
FY2019 | | FY2021 | FY2022 | FY2023 | Target | |
---|---|---|---|---|---|---|
Rotation Rate | 6.0% | 7.3% | 9.0% | 10.0% | 10.1% | 15% or more each fiscal year |
Revitalization of the Internal Recruitment System
We established an internal recruitment system in FY2007 to empower confident, motivated employees to reach higher and to increase the rate of personnel rotations. Initially, however, only about 20 or 30 people a year were transferred using the system. Therefore, we eliminated the need for supervisor approval to apply for another job in-house in FY2021. This significantly increased the number of applications, with about 200 employees transferring each year for three consecutive years. In addition to responding to employees’ willingness to take on challenges, the system helps employees experience different operations and workplaces, broaden their horizons, and improve their skills, thereby making them more adaptable to change.
Number of Employees Using the Internal Recruitment System
Before the Changes to the System | After the Changes to the System | ||||
---|---|---|---|---|---|
FY2019 | | FY2021 | FY2022 | FY2023 | |
Number of applicants | 142 | 148 | 378 | 293 | 325 |
Number of transferees using this system | 27 | 12 | 217 | 201 | 176 |
Training Initiatives
Our human resource development is based on on-the-job training (OJT). In addition, we have established an education system to provide education by job level and various types of specialized education as off-the-job training. We have in place screened, rank-based education programs for the development of leadership human resources.
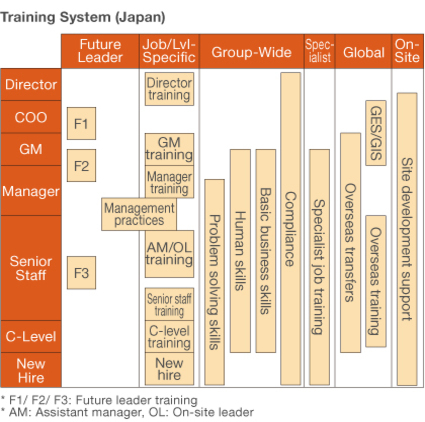
Echelon-based Training
Seiko Epson requires that employees complete a course in management practices before being appointed to a management position. This course prepares them to meet the requirements as a manager by ensuring that they understand their role in terms of both business and actions. On the business end, they learn the skills they need to understand strategic business objectives and respond rapidly and nimbly to internal and external changes in the business environment. On the action end, they learn the skills they need to support the growth and development of the people who report to them by putting organizations and individuals in a position to succeed.
In addition, we provide training for new employees, group training for each grade, and various open-type training to develop people who will fulfill roles as future middle managers step-by-step.
Leadership Training
In addition to a course in management practices for managers and employees who will be appointed to a management position, Epson provides training (F1, F2, and F3 course) to selected employees. In the F1 course, director candidates learn the skills needed to be a top executive. The F2 course is used to prepare middle managers to take the reins of a business or division. In the F3 course participants learn the basics of business through simulated exercises. Through these courses, Epson develops future leaders across the group.
Training for New Employees in Japan
Epson considers the first year of employment to be a training period during which new employees learn about the Epson approach to work.
For the first three weeks, new employees in Epson Group companies in Japan gather for group training, where they learn the following:
・Conduct expected of them as Epson employees
・The mindset and attitude necessary for practicing "monozukuri" or the art and science of manufacturing, which is the foundation of Epson's efficient, compact and precision technologies
・The importance of working cooperatively as a team
Training ranges from lectures on the Epson Global Code of Conduct to hands-on training in manufacturing. New employees learn the importance and enjoyment of working in teams, through group activities that take place throughout the training period.
After they complete group training, new employees are sent to the department where they have been assigned. There they learn their job through on-the-job training under a mentor. Mentors are usually selected from among young employees with three to five years of experience. They produce training plans tailored to the individuals they will be mentoring and, for a full year, provide them with the support they will need to stand on their own. Mentors themselves are expected to grow through this experience.
At the end of the first year, the new employees gather again for follow-up group training, where they can observe how they and others have grown and developed. To further solidify the foundation they have built as a business professional, they review the previous year and consider action plans for the next year and beyond to achieve further growth and expand their contributions to the company.
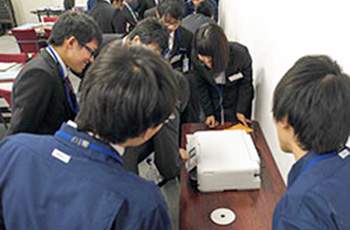
Overseas dispatch of young employees
Epson has 107 R&D, production, and sales sites outside Japan. Overseas operations generate approximately 80% of consolidated revenue and account for 70% of employees. We actively dispatch young employees to our overseas affiliates to gain international experience and prepare them to thrive on the global stage. (Overseas trainee program)
The program was temporarily suspended due to COVID-19 but resumed in FY2022. We dispatched 27 employees in FY2023.
Number of Employees Assigned to Overseas Training Programs
FY2012 | FY2013 | FY2014 | FY2015 | FY2016 | FY2017 | FY2018 | FY2019 | FY2022 | FY2023 | |
---|---|---|---|---|---|---|---|---|---|---|
Number | 8 | 20 | 34 | 38 | 29 | 28 | 22 | 13 | 1 | 27 |
Management by Objectives
Epson has used a management by objectives systems for more than 30 years. All employees of every grade are subject to the systems, and managers and their subordinates work together to set objectives that they can both agree on. Progress toward the objectives is periodically reviewed, end results are evaluated, and new, higher objectives are set. The management by objectives system is itself an on-the-job human resource training system. It is a win-win development cycle in which individual growth leads to the growth of the organization and the company.
Creating Value That Exceeds Customer Expectations and the Monozukuri Juku
Epson's Monozukuri Juku, or Manufacturing School, aims to enhance the customer value we create. To this end, we teach our personnel basic technology and skills and have them experience monozukuri (the art and science of manufacturing) by performing specific manufacturing tasks step by step. This helps them tackle jobs from different angles. To give a specific example, employees learn the basics of component processing technology (molding and pressing). Once they learn these, employees have the skills to make the various parts that go into a product. Employees also learn by mastering essential skills for making production lines more efficient (e.g., automating lines or operating them with fewer staff).
In addition, we contribute to the community and society by giving practical training for new employees of local businesses, offering corporate experiences to junior and senior high school students, and providing instruction for technical skill trainings. We also send experts abroad to take part in official development assistance for building technical skill evaluation systems at the request of the Japanese Ministry of Health, Labour and Welfare.
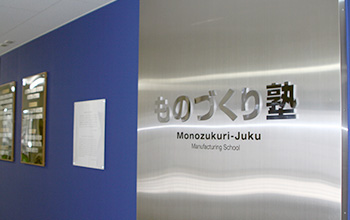
Developing Human Resources to Support Company-wide Production Strategies
Recently, we have faced labor shortages in manufacturing due to rapidly rising wages and workers’ preference for non-manufacturing jobs. In addition, we had suffered from logistics being disrupted due to natural disasters and the spread of infectious diseases, causing delays in delivering products to customers. It has become difficult for Epson to manage these changes with conventional manufacturing, which assumes an abundant and low-cost labor force and centralized production. In our Epson 25 Renewed corporate vision we therefore proposed promoting smart factories using automation and digital technologies and strengthening distributed and local production.
Monozukuri Juku provides opportunities for employees to learn. We hold more than 200 training courses a year to develop the technical abilities of engineers supporting production lines. The training includes mechanical drafting and calibration necessary for manufacturing equipment, as well as machining skills. In addition, we offer basic mechatronics training to help cultivate engineers who will promote automation by teaching them basic technologies such as pneumatic and electrical control. the basics of equipment assembly and adjustment, FA robot training, image processing training, and practical mechatronics training to allow them acquire more practical technologies and skills.
Monozukuri Juku does not only train Japanese engineers but also engineers from our manufacturing affiliates worldwide, where we seek to educate the employees about manufacturing and machine maintenance in order to develop future local leaders. In addition to on-site training, we also make full use of a remote training system established during a time when overseas business trips were difficult, to deploy necessary training in a timely manner. Through these efforts, we will promote optimal human resource development and improve the process control level of each of our worldwide affiliate companies so we can respond strategies such as distributed production.
Developing Young Technicians through National Skills Competition
As a manufacturing company, Epson uses training for WorldSkills competitions to develop "groundbreaker technicians" 1 who have acquired essential manufacturing knowledge and skills at an early age. As a rule, individuals are allowed to take part in two consecutive WorldSkills training, starting in the second year of employment. The purpose of the short-term intensive trainings is to help participants learn technical skills at the all-Japan level. Every year we send 10-15 individuals to the National Skills Competition associated with WorldSkills to compete in seven selected occupational categories that are applicable to our employees' work: Instrument making, Plastic die engineering, Mechatronics, Industrial electronics, Mobile robotics, Web design, and Watch repair.
New employees sent to Monozukuri Juku as WorldSkills trainees experience monozukuri (the art and science of manufacturing) in such forms as filing and sawing. They also learn basic knowledge about machinery, electricity, and other general topics in each occupational category. In conjunction with everyday occupation-specific training, there are training camps three times a year. Participants lodge together, run a long distance, set targets, and the like. All of this helps to build a sense of solidarity as a team.
To recreate the feel of the national competition, we also hold joint training events with other companies that take part in WorldSkills. Additionally, our employees actively pursue such national qualifications as machining technician, electronic device assembly technician, web design technician, and watch repair technician. After participants finish WorldSkills trainings, they get practical training to help them build the basic skills learned there into skills they can use to make products. Each participant then joins an operations division. The units they join often praise these employees for performing beyond expectations.
1 Technicians with the ability to break from precedent to create innovative technologies and systems.
FY2023 Workforce Composition and Training Data
Main Online Courses (Japan)
Course | Participants |
---|---|
Fundamentals of Export Control (2023) | 18,466 |
Epson's Compliance (2023) | 20,532 |
Basic Information Security (2023) | 21,074 |
Basic Environmental Training II (2023) | 20,334 |
Introduction to Procurement (Ethics and code of conduct) (2023) | 17,691 |
J-SOX(2023) | 20,038 |
Basic Harassment Preventive Training (2023) | 19,524 |
Occupational Safety Training (2023) | 19,742 |
Healthy Balance Between Work and Life Training | 11,551 |
Business & Human Rights (2022-) | 18,473 |
*The number of persons completing the course by March 31, 2024
Training by employee level
Training | Who | Participants | Percent |
---|---|---|---|
New employee orientation | New hires | 344 | 100% |
C-level employee training | New C-level staff | 285 | 97.9% |
Senior staff training | New senior staff | 301 | 98.0% |
Section manager training | New section managers | 143 | 93.5% |
General manager training | New general managers | 43 | 91.5% |
* Data for Seiko Epson Corporation employees as of March 31, 2024
*Employees who have not received training are scheduled to do so in FY2024.
Training Hours
Unit | FY2018 | FY2019 | | FY2021 | FY2022 | FY2023 | |
---|---|---|---|---|---|---|---|
Training by regular employee | Hours | 11.0 | 11.1 | 7.4 | 20.9 | 21.5 | 34.2 |
Total training hours | Hours | - | - | - | 228,696 | 235,910 | 375,219 |
*Seiko Epson HR Department training for regular employees and time spent on online courses. Education and training courses of functional supervisory departments and operations divisions are also included after FY2021.