Case study - Value Chain
Epson has manufacturing sites and sales centers in all parts of the world making environmentally-conscious transportation an important consideration. Here we present examples of such environmentally-conscious transportation initiatives in which we introduced high cube containers1 and changed our distribution center and shipping method.
1 With a height of 9 ft 6 in (about 2.6 m), they are 1 ft (about 30 cm) taller than standard containers, whose height is 8 feet 6 inches (about 2.3 m).
- Topic 1 : Utilization of Low-Carbon Shipping Services
- Topic 2 : Slashing CO2 emissions by Redesigning Distribution Routes
- Topic 3 : Improving Transport Efficiency with High Cube Containers
- Topic 4: Reduced Environmental Impact by Changing Printhead Shipping
Topic 1 : Utilization of Low-Carbon Shipping Services
In fiscal 2024, Epson began using low-carbon shipping services to reduce greenhouse gas (GHG) emissions for some of its maritime shipping services to Europe. In the first year, we plan to use one-hundred 40-foot export containers from the Philippines to reduce our greenhouse gas emissions by approximately 230 tonnes compared to conventional maritime transport using heavy fuel oil ships. Decarbonization is a global challenge, and the shipping industry is transitioning to alternative fuels with low environmental impact with the goal of achieving net-zero GHG emissions by around 2050. European shipping companies in particular are accelerating their timelines to achieve this goal. Epson has partnered with global shipping giant Maersk to use a container ship service that operates on biodiesel and green methanol as alternative fuels on some routes. This will reduce GHG emissions on these routes by up to 84% compared to conventional ocean transport.
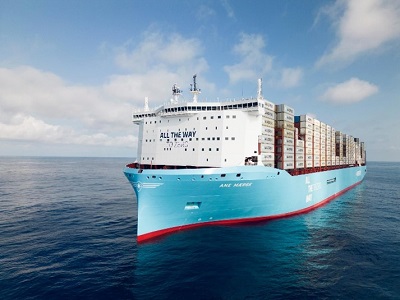
Topic 2 : Slashing CO2 emissions by Redesigning Distribution Routes
Epson was providing consumer products for customers in southern Africa by shipping them to Johannesburg, South Africa from a distribution center in the United Arab Emirates or from a central warehouse in Germany. This approach was taken because Epson did not have its own distribution center in Africa and was using an existing distribution center.
Having to first ship products to the UAE or Germany from our production sites in Asia (China, Indonesia, and the Philippines) before delivery to southern Africa increased transport distances. We needed to address the issue of higher transport CO2 emissions and long delivery times.
To do so, we established our own new distribution center in South Africa and began shipping directly to it from our production sites to serve the expanding African market. This dramatic change in distribution routes resulted in CO2 emissions being reduced to 66–75% of those from shipments via the UAE, and to 34–41% of those from shipments via Germany.
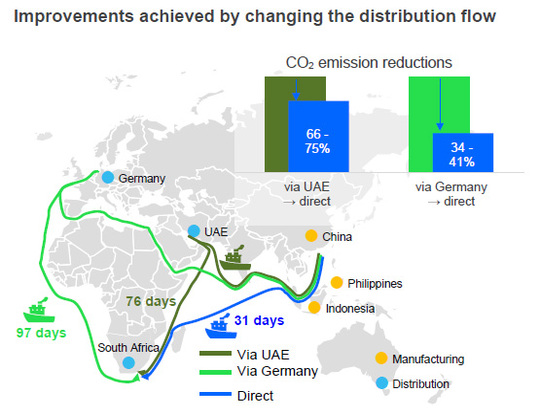
Topic 3 : Improving Transport Efficiency with High Cube Containers
Currently, high cube containers account for about 70% of shipping containers in the marketplace. Hitherto, Epson has used the standard type of container for shipping products from its factories, but with the widespread adoption of high cube containers, we are gradually making the switch.
Since the inner dimensions of the containers are higher, palletizing products for standard containers resulted in wasted space amounting to about 10%. Optimizing the pallets for high cube containers reduces the number of containers required, contributing to reducing environmental impact by raising transportation efficiency.
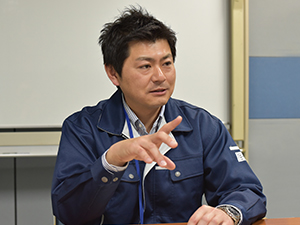
The head of logistics planning, who led the initiative, says, "All of our arrangements including the number of products shipped and the height of the pallet racks in our warehouses were optimized for pallet sizes to fit standard containers. In order to introduce high cube containers, it was necessary to ask for the cooperation of the warehouse managers at sales companies who receive the containers. We had to ask them to review the layout of their warehouses, optimize the method of stacking and so on. We had a very hard time adjusting the cost factors, but a shared awareness that this would reduce our environmental impact was a very important point in undertaking this activity."
For shipments from Southeast Asia, where many of Epson's finished products are manufactured, the switch to high cube containers for all areas of Europe was completed in fiscal 2011 and in fiscal 2015 for the U.S., Brazil and India.
Comparison of Standard and High Cube Containers
40 ft Standard containers | 40 ft High cube containers | Advantages | |
---|---|---|---|
Container size (LWH) | 12,033 x 2,352 x 2,393 mm | 12,033 x 2,352 x 2,698 mm | 1 ft (30 cm) up |
Cubic capacity | 67.7 m³ | 76.4 m³ | 12.9% up |
Case of WF-2650 Series | |||
Packaging dimensions | 488 x 434 x 301 mm | - | |
Palletize dimensions | 976 x 1,302 x 2,108 mm | 976 x 1,302 x 2,409 mm | 1 additional layer |
Number of units per pallet | 42 units | 48 units | 14.3% up |
Number of units per container | 882 units | 1,008 units |
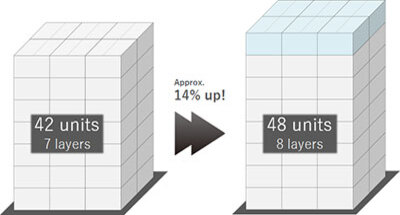
Results of Switching Containers for Shipping to the U.S.
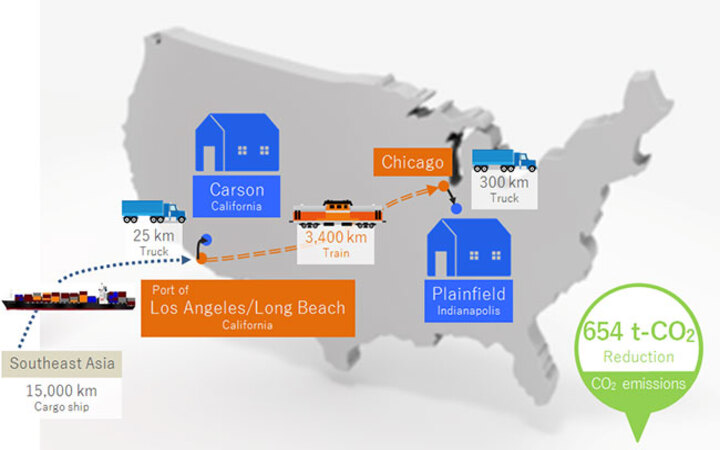
* We have calculated the reductions in CO2 emissions emitted when transporting containers by cargo ship, train and truck from our manufacturing affiliates in Southeast Asia, as a result of reducing the number of containers shipped to the U.S. by about 200. The unit indicator by the Japan Ship Technology Research Association is used for calculating emissions during sea transport.
Topic 4: Reduced Environmental Impact by Changing Printhead Shipping
Previously, printheads for shipping to our printer manufacturing sites in Indonesia were gathered from our plants around Japan at Tohoku Epson in Yamagata Prefecture and transported by truck to Narita Airport for air transportation. By establishing a sea transportation pipeline from Sakata Port, which is located conveniently about 8 km from Tohoku Epson, we significantly reduced our costs and CO2 emissions.
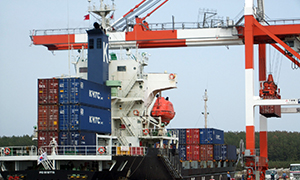
CO2 Reductions Due to Changing the Shipping Method (Unit: t-CO2)
Before | After | |||
---|---|---|---|---|
Distance | CO2 emissions | Distance | CO2 emissions | |
Land | Approx. 500 km | 33.9 | Approx. 8 km | 0.5 |
Air | Approx. 5,800 km | 401.3 | - | |
Sea | - | Approx. 6,200 km | 47.7 | |
Total | 435.2 | 48.2 |
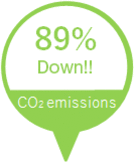
* We calculated the CO2 emissions from shipping a 20-foot container from Tohoku Epson to Indonesia's capital, Jakarta. The unit indicator by the Japan Ship Technology Research Association is used for calculating emissions during sea transport.