Case study - Production
- Topic 1 : Updating to a More Efficient Cogeneration System
- Topic 2: Visualizing Air Conditioning to Help Reduce CO2 Emissions
- Other Case Studies
Topic 1 : Updating to a More Efficient Cogeneration System1
The Suwa Minami Plant, where Epson manufactures core devices such as high-temperature polysilicon TFT LCD panels for 3LCD projectors and PrecisionCore MicroTFP printheads, is one of Epson's most energy-intensive facilities in Japan. The plant had used a cogeneration system (CGS) to generate between 40% and 60% of its power needs since 2001, but in May 2014, Epson replaced that CGS with three new high-efficiency CGS. The new systems use less natural gas to operate and reduced the plant's CO₂ emissions. The use of the three new CGS makes the overall system easier to maintain and provides a steady supply of electrical power.
1 Cogeneration systems, also known as combined heat and power, utilize a single fuel source to produce and supply both electricity and heat.
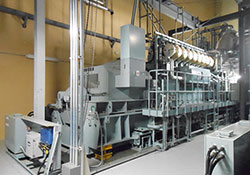
CGS Overview
Energy output | Units | Model | Fuel | |
---|---|---|---|---|
New | 2,270 kW | 3 | Gas engine | Natural gas |
Old | 7,200 kW | 1 | Gas turbine | Natural gas |
Annual savings (by switching to a gas engine from a gas turbine system)
Amount of natural gas saved: 1,480,000 Nm³
Reduction of CO2 emissions: 4,900 tons
Benefits of CGS
Whereas about 60% of the energy generated by a typical power plant is lost as waste heat and during transmission, only about 15% to 30% of the energy generated by an on-site CGS is lost as waste heat. In addition to generating electricity, CGS also save energy because they effectively recycle about 30% of the waste heat into energy for heating or cooling.
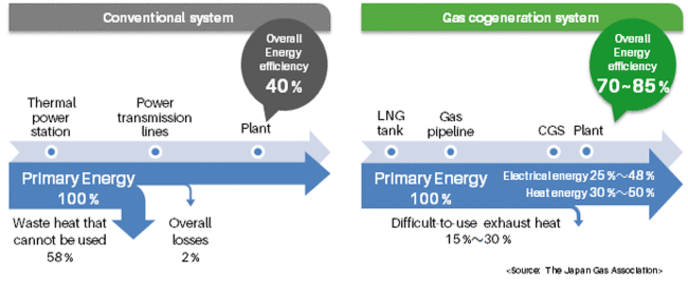
Case 2: Visualizing Air Conditioning to Help Reduce CO2 Emissions
Epson Portland Inc. (EPI), in the US, has the important role of manufacturing Epson ink cartridges and other products for the Americas. The manufacturing process for Epson inkjet printer cartridges requires a clean room environment to ensure the levels of quality where more than 7 million kWh are consumed each year, on average, for air conditioning and production support equipment.
In 2011, the Facilities team worked with the non-profit Energy Trust of Oregon to introduce a new air conditioning monitoring system to reduce EPI's energy use and environmental impact. The monitoring system allowed Facilities to observe and record the actual air temperatures in the ink cartridge production areas throughout the day.
EPI used the data to qualify the modification of the air conditioning system so that, when outdoor temperatures are lower than those in the production areas, warm air is automatically exhausted and outside air is used for cooling, saving energy and money. These actions have helped EPI reduce its annual CO2 emissions by more than 100 tons.
Since implementing this cooling system in 2011, EPI has taken advantage of various other energy conservation opportunities. These have resulted in cumulative CO2 reductions of approximately 655 tons.