マイクロウィーブ
色むら・バンディングを防ぐ
マイクロウィーブ
エプソンのインクジェットプリンターは、PrecisionCoreテクノロジーなどの独自技術により、高い着弾位置精度を実現することで、高精度な印刷を可能にしています。
しかし、多種多様な用紙に印刷する場合、用紙たわみや、搬送時の用紙滑りなどを要因としたドット位置のずれが発生することで、画像の中に濃い部分と淡い部分の不均一性が発生する濃淡バンディング、印刷むらや、パスの境界部にはスジバンディングなどが発生してしまい、印刷品質の低下を招きます。
そこで、印刷品質の低下を抑制するためにエプソンが独自に開発し、自社プリンターに搭載している技術が「マイクロウィーブ」です。
エプソンのマイクロウィーブが印刷品質を保つために果たす役割やマイクロウィーブ技術について紹介します。
マイクロウィーブとは
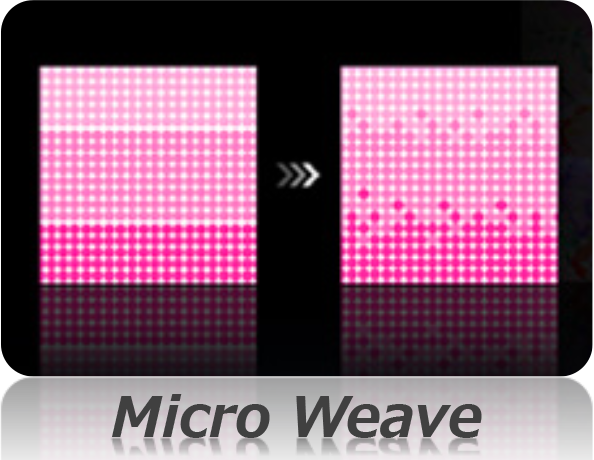
マイクロウィーブとは、パス間の着弾ドットずれが生じても色むらやバンディング(帯状のスジ)を目立ち難くさせるエプソン独自の技術です。
シリアル走査方式での高画質実現のためには、走査領域のつなぎ目がバンディングとして視認されることを防ぐために、1回の紙搬送量をヘッドのノズル長の数分の1以下とし、同一領域を複数回の主走査で徐々に完成させていくインターレース走査が用いられます。一般的には、走査領域のつなぎ目部分のバンディングを目立ち難くするためには、主走査回数を多くし、印刷速度を犠牲にして画質改善を行いますが、エプソンのマイクロウィーブでは、ハーフトーニングで決めたドット配置に対して、どのパス・どのノズルでドット吐出するかを最適化することで速度劣化も抑制しています。
具体的なマイクロウィーブとして、走査領域のつなぎ目部分の処理があります。走査領域のつなぎ目部分のドット配置を階調的に配置し、複数パスに分けて印刷させることで着弾ドットずれを分散し、誤差によるつなぎ目部分のバンディングを目立ち難くします。
エプソンのマイクロウィーブでは、階調部分のドット配置を決める際に、ハーフトーニングで用いている誤差耐性の高いディザマスクを併用し、さらに最適化することで、着弾ずれ耐性を高めています。その結果、高速・高画質の両立と、安定して印刷できることを可能としています。
マイクロウィーブ処理の仕組み
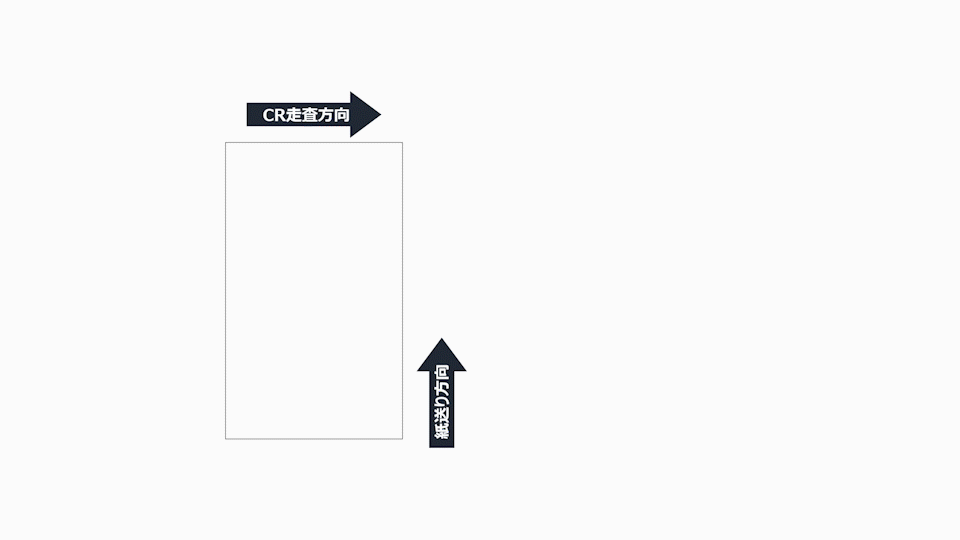
マイクロウィーブ処理ではどのようなことが行われているのか、なぜマイクロウィーブによりバンディングを防ぐことができるのかをより詳しく紹介します。
インクジェットプリントは、カラーマネジメントフローによって得られたインク量を、ハーフトーニング処理によってドット量に変換し、その後マイクロウィーブ処理を経てプリンターによる印刷を実現しています。マイクロウィーブ処理では、ハーフトーニングで決めたドット配置に対して、どれくらい紙搬送をして、どのパス、どのノズルでドット吐出するのかを決めています。
通常、シリアル走査方式の印刷は、同一領域を複数回の印刷ヘッドの走査により画像を徐々に完成させていきます。
このときの印刷出力方向に対して垂直な方向を主走査方向、平行な方向を副走査方向といいます。また、主走査方向に1列に並ぶドット列を「ラスターライン」と表現します。
色むらやバンディングはラスターラインの間隔がさまざまな要因、例えば用紙搬送時の滑りなどによる着弾ドットずれによって、粗密差が発生することで生じます。
そこでエプソンはマイクロウィーブ処理により、ラスターラインごとに発生する粗密差を分散させることで目立ちにくくし、抑制する開発を行ってきました。
抑制させる一つの手段として、前述の走査領域のつなぎ目部分の処理であるオーバーラップ印刷があります。一部のドットをマスクして、その後の走査で相補的に印刷することでオーバーラップを実現しており、これによりラスターラインを複数のノズルで構成することで着弾ドットズレを分散します。
さらにオーバーラップ部分のドット配置を最適化させることで、用紙搬送誤差などによる着弾ドットずれによるバンディングを目立ち難くしています。
この最適なドット配置を決める際には、ハーフトーニングで用いている誤差耐性の高いディザマスクも併用し、さらに着弾ずれ耐性を高めることで高速・高画質の両立と、安定して印刷できることを可能にしているのです。