技術者インタビュー
匠の技にエプソンの製造技術が
融合することで
機械式腕時計はさらに進化する
1950年の誕生から70年以上の歴史を誇るエプソンの機械式腕時計が『オリエント』です。 また、翌年1951年に誕生した初代『オリエントスター』などこれまで数多くのモデルを発表してきました。そして、その裏では技術者たちの絶え間ない技術革新がありました。そのようなウオッチ開発の歩みを、『オリエント』、『オリエントスター』の開発に長く携わってきた髙野、向山の2人が、最新モデルに搭載されている『46系F8ムーブメント』の技術開発の秘話を語ります。
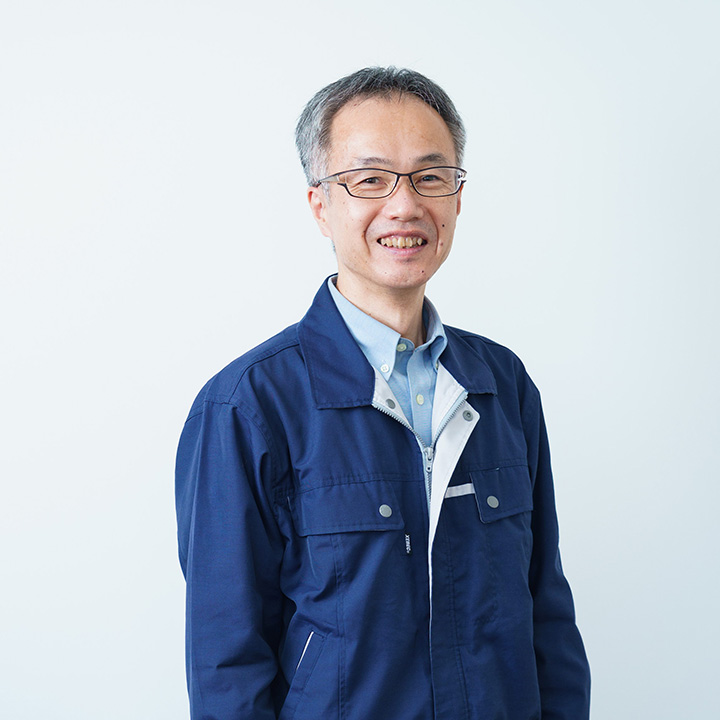
WP開発設計・技術部 髙野
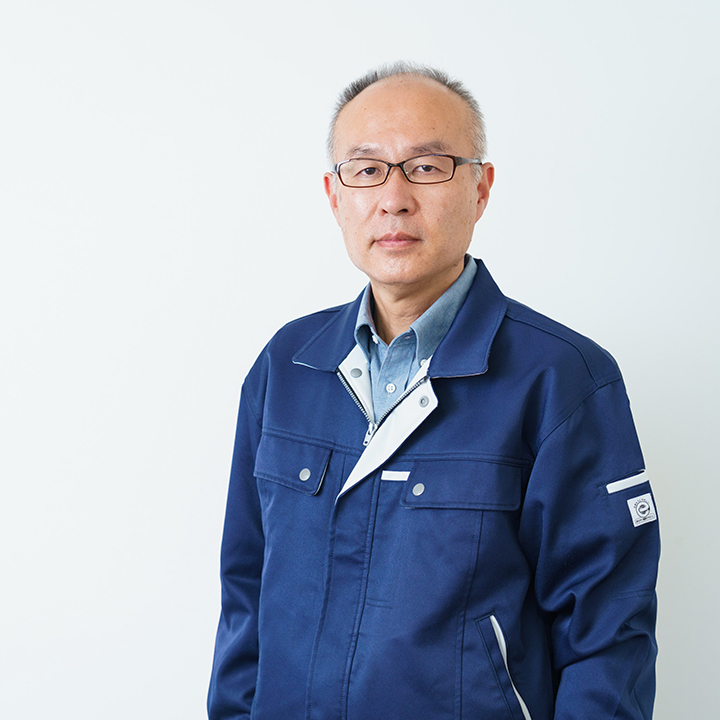
WP開発設計・技術部 向山
『オリエント』の
ウオッチムーブメントの系譜
まずはオリエント時計としての歴史について、改めてご紹介いただけますか。
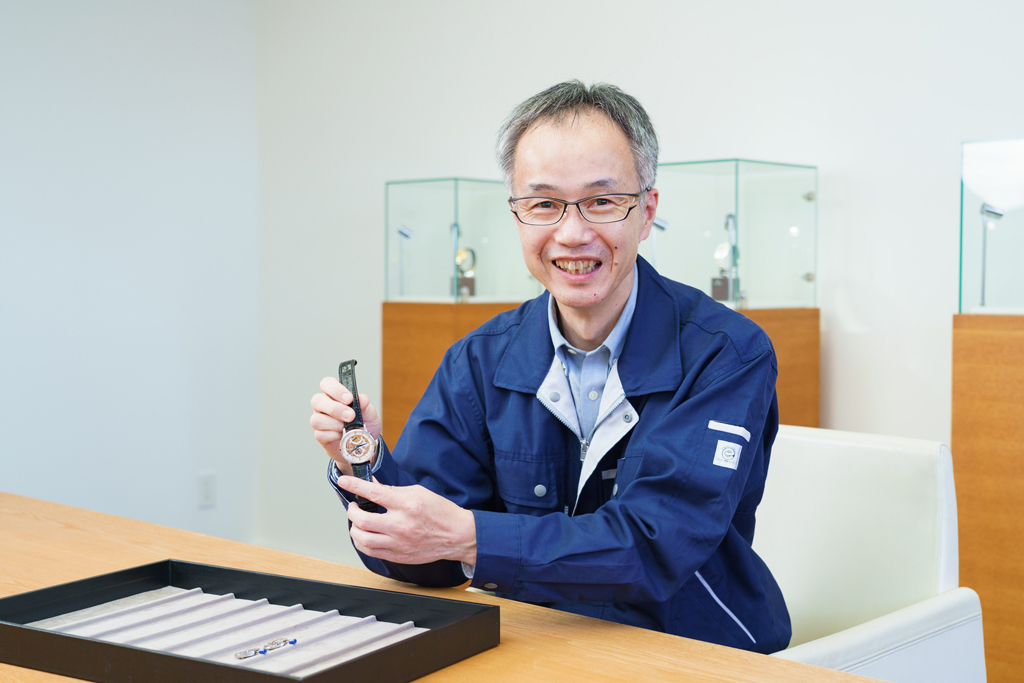
髙野オリエント時計株式会社として、初代『オリエント』が誕生したのは今から70年前の1950年になります。私は実際に開発に携わってはおりませんが、資料や先輩技術者から聞いた話では、初期モデル発表後は積極的に技術開発が進み、T型、N型、L型といったムーブメントが1960年代までに開発されていきます。
向山そして1971年に、現在多くの『オリエント』や『オリエントスター』に搭載されているムーブメント、46系ムーブメントが開発されます。46系ムーブメントではエプソンが独自開発した自動巻き技術『マジックレバー』を搭載することで、高い巻き上げ効率を実現。機構もシンプルに設計したことで、その後、数多くのモデルに搭載されるムーブメントとなります。
髙野一方で46系ムーブメント開発後の1980年代は、クオーツウオッチが中心との時代背景がありました。そのためオリエントウオッチに限らず、多くの国産機械式腕時計の技術進歩は、しばらくのあいだ進みませんでした。実際、販売先も国内ではなく海外がメインで、電池が入手できない地域などでの使用が主だったようです。
向山ですから言い方は悪いですが、ただ粛々と作り続けていた、という表現が正しいと思います。46系ムーブメントはシンプルなつくりであったため、メンテナンスしやすい点や多くのモデルに搭載できる点も好まれたのでしょう。ただ粛々と20年近く同じムーブメントを作り続けていたことが、最新ムーブメントF8も含め、その後再燃するオリエントウオッチの技術革新につながっていったとも言えると思います。
髙野まさに90年代に入ると状況は一変します。スイスメーカーの高級機械式ウオッチなどが再び注目されるようになり、そのムーブに引っ張られるかたちで、『オリエント』のウオッチも注目されていきました。その結果、ぜんまい残量を示す「パワーリザーブインジケーター」や曜日を逆行運針で示す機能「レトログラード」といった、現在のモデルにも搭載されている新たな機構が開発され、さまざまなモデルが発表されていきました。
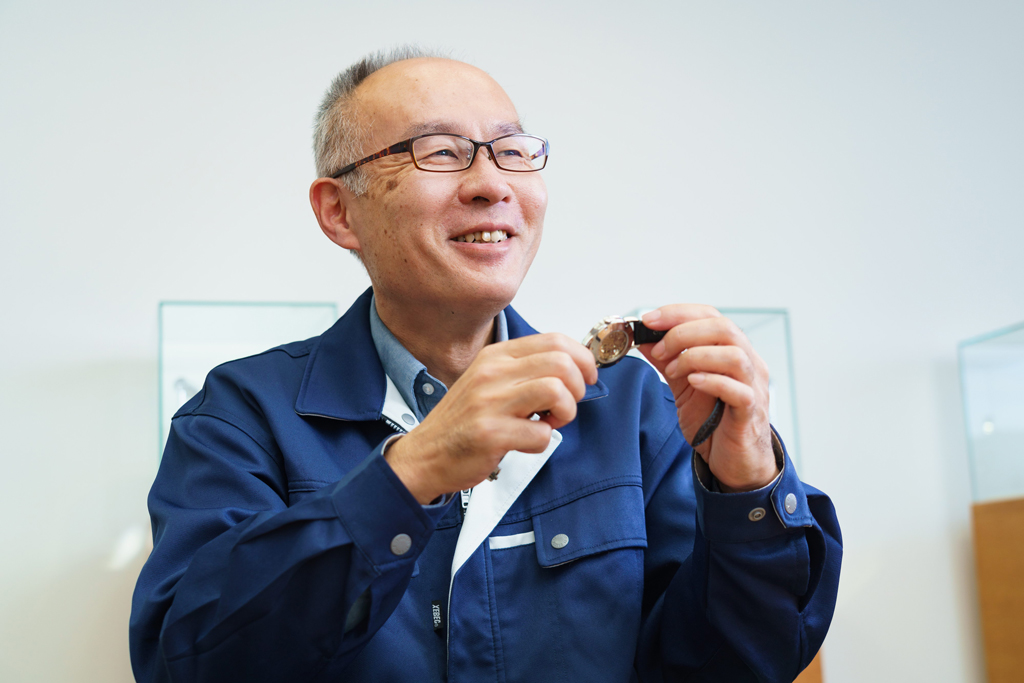
向山2010年代に入ると、新たなムーブメントの開発プロジェクトが立ち上がります。46系ムーブメントが開発されたのは1971年ですから、約40年ぶりの大きな改革でした。新ムーブメントでは地板や受け類といった、それまではモデルごとに変えていた部品を、統一する設計ならびに生産体制への刷新を行いました。
髙野なかでも難しかったのが、パワーリザーブインジケーター機構の有無を同じ部品で実現することでした。また技術的な課題だけでなく、新しいムーブメントの開発中も製品を製造することが求められましたから、販売状況などを入念に下調べするなど、2年がかりのプロジェクトでした。こうして完成したのが、通称F6と呼ばれるムーブメントです。
向山次のモデルF7(2017年)では、精度の向上ならびにパワーリザーブの持続時間のさらなる増加、40時間から50時間を実現します。装飾においてもそれまでのゴム砥石から刃物による切削に変更することで、よりシャープな模様を実現しました。またこのころはムーブメントの主要パーツである「がんぎ車」の研究開発にも取り組んでいました。
「がんぎ車」の精度向上、
重さ軽減を目指し
素材を金属からシリコンに変更
がんぎ車とはどういった役割を持つパーツなのですか。
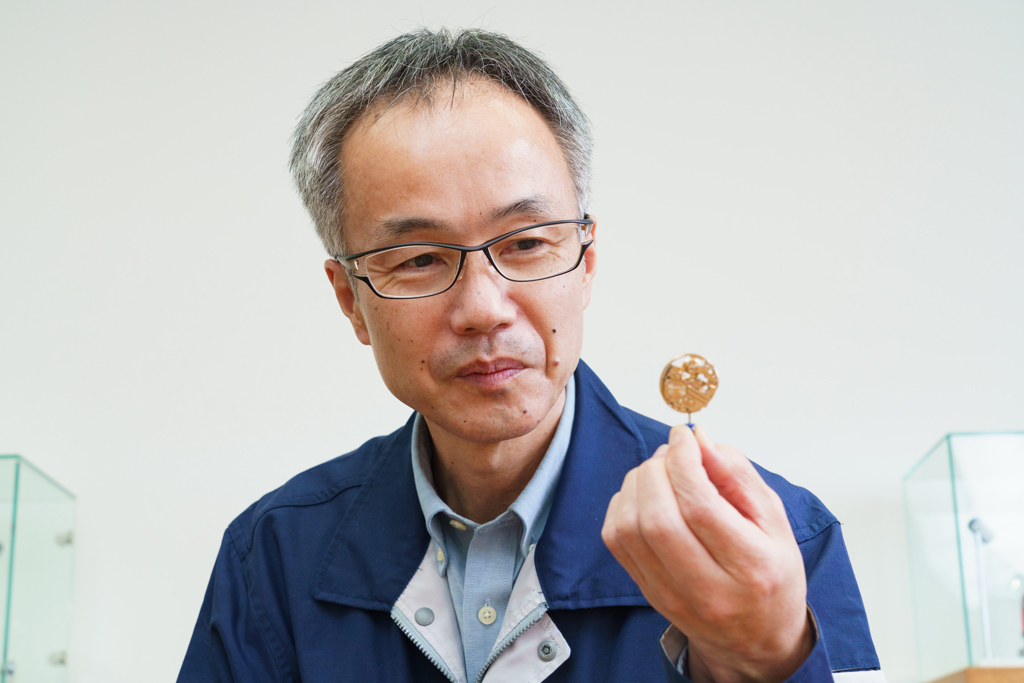
髙野一言で説明すれば、正確な時を刻むための最重要パーツのひとつです。一般的に機械式腕時計は100個以上もの精緻なパーツから構成されています。これらのパーツが個々に精密かつ正確な動きをすることで、正確な時を刻みます。動力源はむかしのブリキのおもちゃで使われていたゼンマイで、このゼンマイを巻き上げ、その巻き上げたエネルギーが解き放たれる際に発されるエネルギーを動力源としています。
向山エネルギーは「香箱(一番)車」「二番車」「三番車」「四番車」という4つの歯車で構成される「輪列機構」にまず伝わります。2番車には分針が、4番車には秒針が取り付けられており、それぞれ60分、60秒で1周する仕組みです。そしてここからが重要ですが、輪列機構の先にがんぎ車があり、その先に「アンクル」「テンプ」「ヒゲゼンマイ(テンプの構成部品の一つ)」といったパーツで構成される「脱進機」「調速機」と呼ばれる機構につながります。つまりがんぎ車は、輪列機構の最後の歯車であると同時に、「脱進機」を構成するパーツでもあるのです。
髙野がんぎ車の役割はゼンマイのエネルギーを一気に解放せず、徐々に使っていくことです。そして繰り返しになりますが、その動きが結果として「カチカチ」という正確な時を刻んでいるのです。振り子時計の動きをがんぎ車、アンクル、テンプで再現しているようなイメージです。
がんぎ車の研究開発は具体的にどういった内容だったのでしょう。
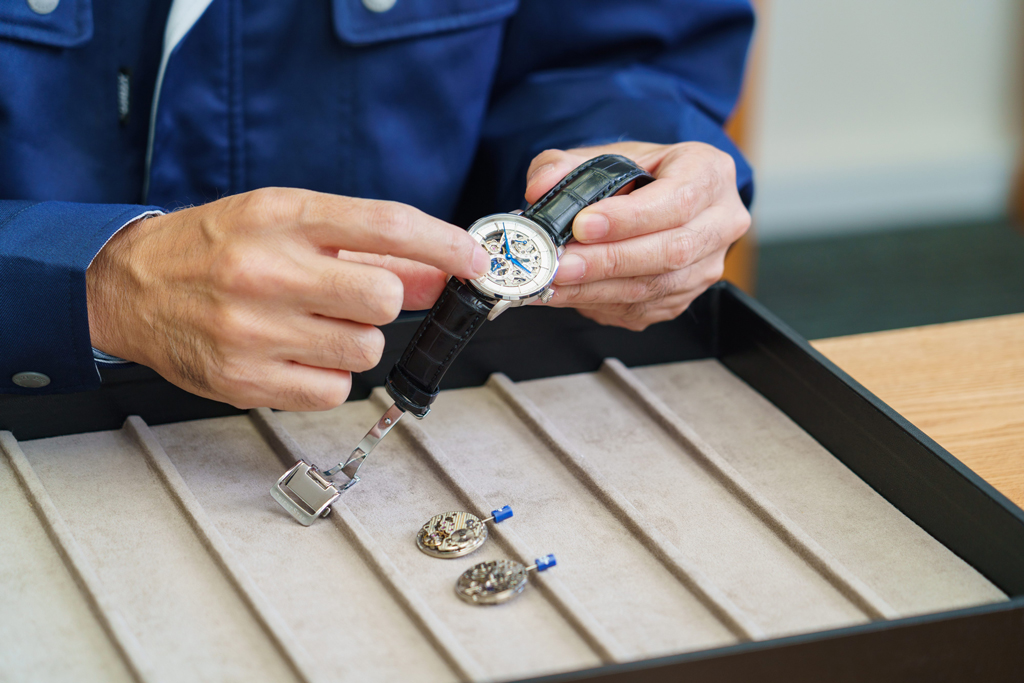
向山大きくは2つのテーマがありました。さらなる長時間駆動の実現ならびに、がんぎ車の精度向上です。前者においては、ゼンマイで得たエネルギーのおよそ半分が、脱進機で消費されています。つまり脱進機のパワーロスを減らすことができれば、さらに駆動時間は伸びるだろうと予想できました。
髙野半分ものパワーを消費している理由はいくつかありますが、その一つが重量です。F7までのムーブメントではがんぎ車は洋白材という金属を加工して作られています。そのため、重くて、動かすのにパワーが必要となります。
髙野もう一つのパワーを消費している原因は、爪石とがんぎ車が消費する摩擦力です。がんぎ車とてんぷをつなぐアンクルの先端は「爪石」と呼ばれ、長時間の駆動に耐えるよう人工ルビーで設計されています。がんぎ車と爪石が係る量が、従来の加工精度の100分の1mmレベルだとそれなりの余裕(遊び)をもたせて設計する必要がありました。当然ですが、その遊び分は余計な負荷となり、爪石とがんぎ車が消費する摩擦力も発生していました。そこで我々はこれらの重さと寸法精度の問題を解決するために、これまで経験のない「シリコン製がんぎ車」の開発に着手することを決意しました。
「MEMS加工技術」により、
シリコン製がんぎ車の製造に成功
シリコン製がんぎ車というのはウオッチでは一般的なのですか。
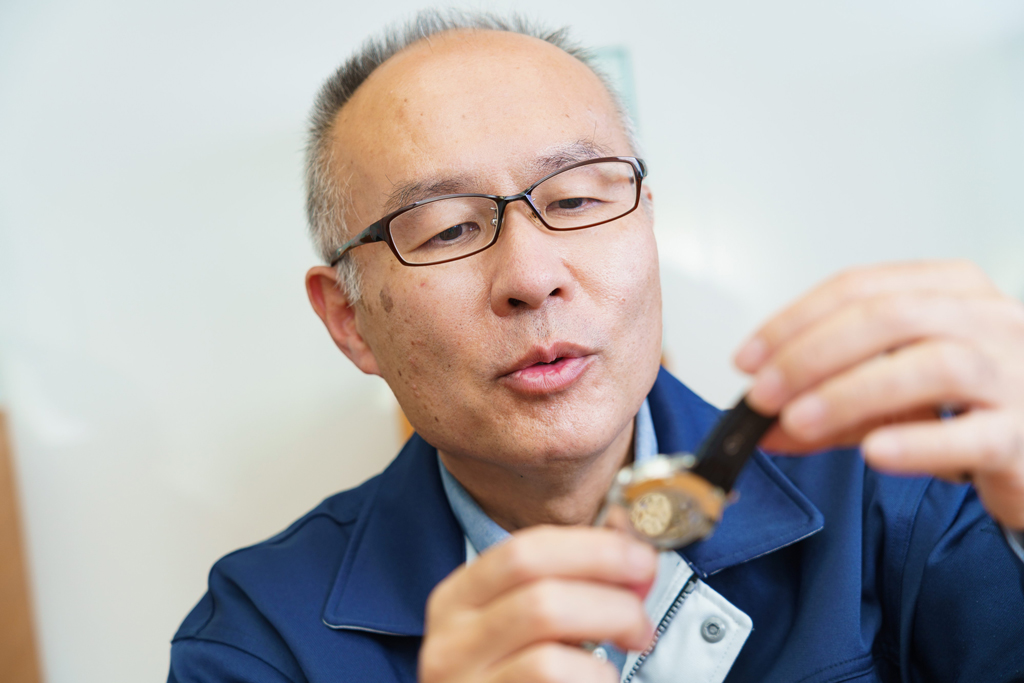
向山スイスの時計メーカーでは一部採用されていますが、国内の時計メーカーではこれまで例がない取り組みだと思います。さらに言えば、シリコン製部品を作る能力はウエアラブル機器事業部にはありませんでした。そこでシリコンの扱いに長けている、エプソンの技術開発本部に協力を打診。技術開発本部と二人三脚で研究開発を行いました。具体的には、エプソンのプリンターヘッドなどにも使われているMEMS加工技術を活用することで、シリコン製のがんぎ車の実現を目指しました。
開発に際してはどのあたりが難しかったですか。
髙野シリコンは以前使用していた洋白材に比べ比重が約3分の1と小さいのですが、ガラスのような素材ですからもろく欠けやすいとの特性があります。そのため軽量化を実現しながらも、いかに強度を維持できるか。そこが、ひとつの大きな技術課題でした。解決したのは「膜」でした。
膜、ですか?
向山シリコンに熱処理を施すと、表面に「SiO2(酸化膜)」という膜が生じます。この膜を除去し、再び熱酸化を行うのです。この工程を繰り返しいていくことでシリコン表面が丸みを帯び角が取れ、その表面にはSiO2(酸化膜)の層ができ、もろく欠けやすい特性を改善できることが分かったのです。結果、従来の金属製の「がんぎ車」の強度を上回るほどのスペックのシリコン製のがんぎ車を作ることに成功しました。
髙野MEMS加工技術により、精度は一桁アップの1000分の1mm単位まで高まりました。その結果、先の係合量は従来の80%まで減らすことができました。さらに、洋白材をシリコンに変更した結果、がんぎ車の重量は約3分の1にまで減りました。ただ課題は他にもありました。
シリコン製がんぎ車の研究開発で
新たな特許技術を取得
どのような課題ですか。
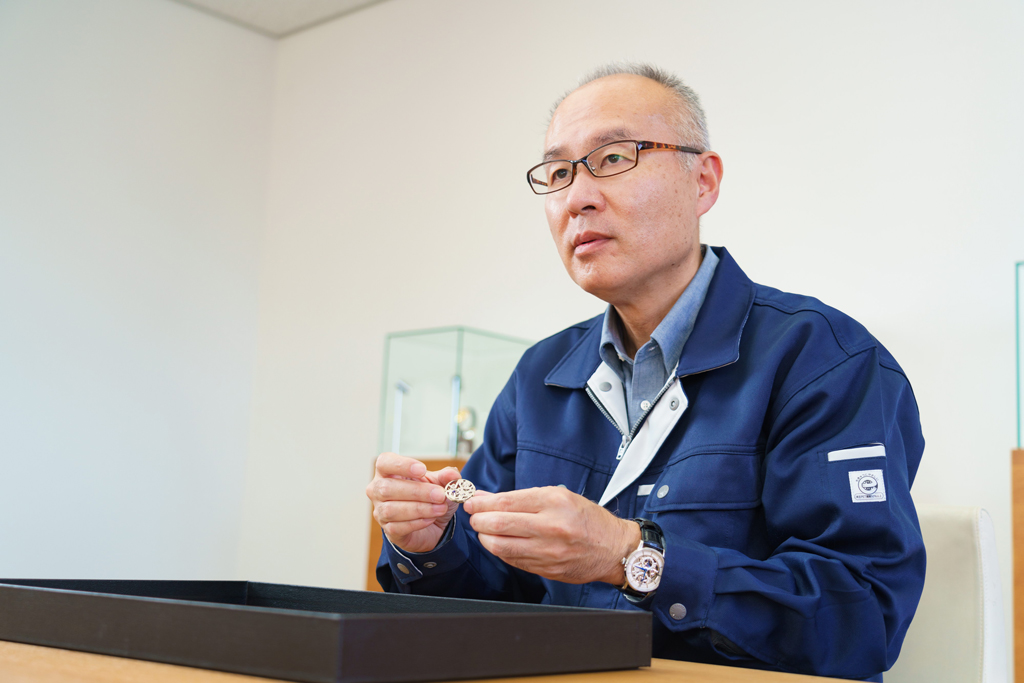
向山これも欠けやすいシリコンならではの特性による問題でした。がんぎ車の中心に差し込む「かな」という軸パーツを調整する必要が生じたのです。かなは金属ですから、以前のがんぎ車であれば両者が金属性であったため、強く打ち込むことでしっかりと固定することができました。
髙野しかしシリコン製のがんぎ車に同じように金属製のかなを使って固定しようとすると、がんぎ車が割れてしまったのです。そうはいっても緩めてしまってはがんぎ車が正しく保持できず、精度も悪くなってしまいます。さて、どうしようかと。そうして出たアイデアが、がんぎ車の形状でバネ性を持たせることで力を分散させ、割れを防ぐというものでした。
画期的なアイデアですね。
向山ただ実際にどのような形状がベストなのか。アイデアはよかったのですが、そこから実際に割れに対応する形状のがんぎ車を設計するまでの道のりは、そう簡単ではありませんでした。技術開発本部のメンバーとアイデアを考えるのはもちろん、がんぎ車の試作品を何十種類も作り、最適な形状を探していきました。このような試行錯誤を重ね開発されたのが現在の形状です。
とてもユニークな形状です。
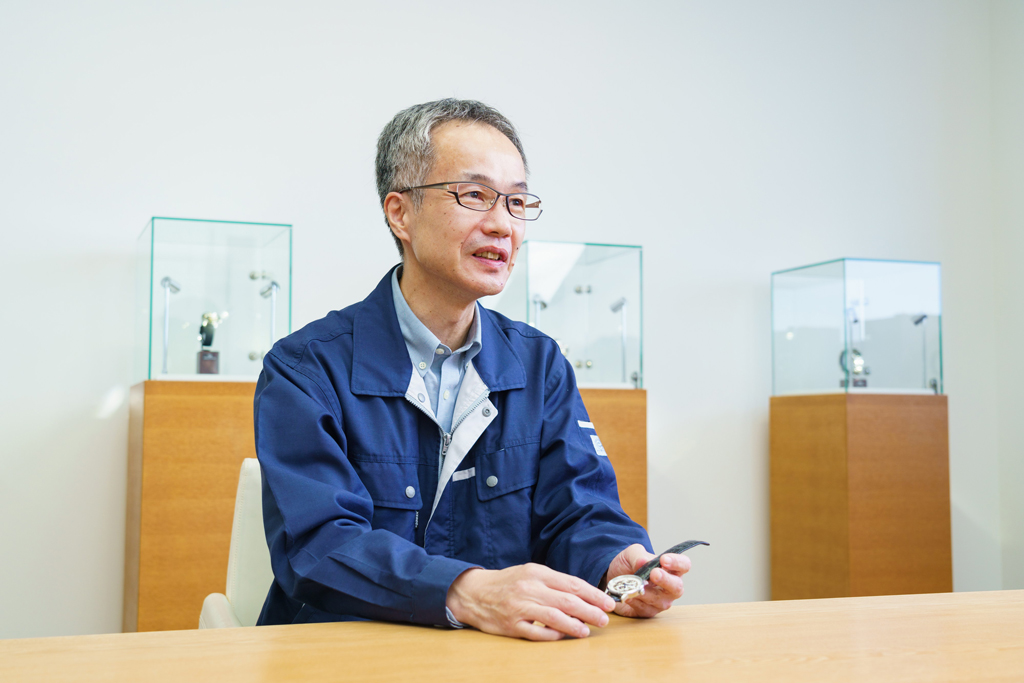
髙野風車の羽のような形状にすることで、がんぎ車の一部にバネ性を持たせています。さらに、かなを密着する部分の形状を歯ブラシの毛先のようにしました。そしてこのような凹凸の形状にかなが嚙み合うよう、かなも新たに設計し直し、スリットを入れたのです。このような試行錯誤の結果、両者が的確に嚙み合いながらも力を分散する新たなシリコン製がんぎ車が誕生。この設計は特許も取得しています。
ナノレベルの膜厚調整技術で
鮮やかな青色を実現
新たなムーブメントF8を搭載したモデルはスケルトンのため、見た目にも配慮したそうですね。
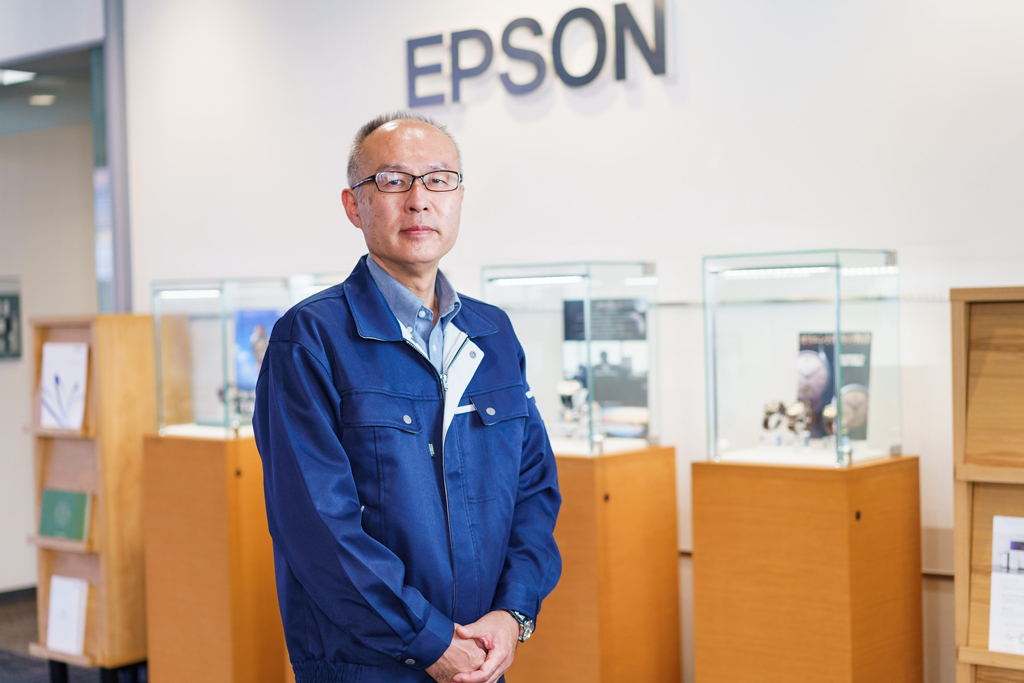
向山ええ。ここでも技術開発本部が保有する、ナノレベルの膜厚調整技術が活躍しました。発色をより鮮やかにするために、先の酸化膜に加え、ポリシリコンの膜も成膜しています。その結果、多層膜によって鮮やかな青色のがんぎ車となりました。ちなみに青色にしたのは、がんぎ車の形状が宇宙の銀河系に似ていたことから、それならば天の川をイメージした青色にしようとの発想からです。
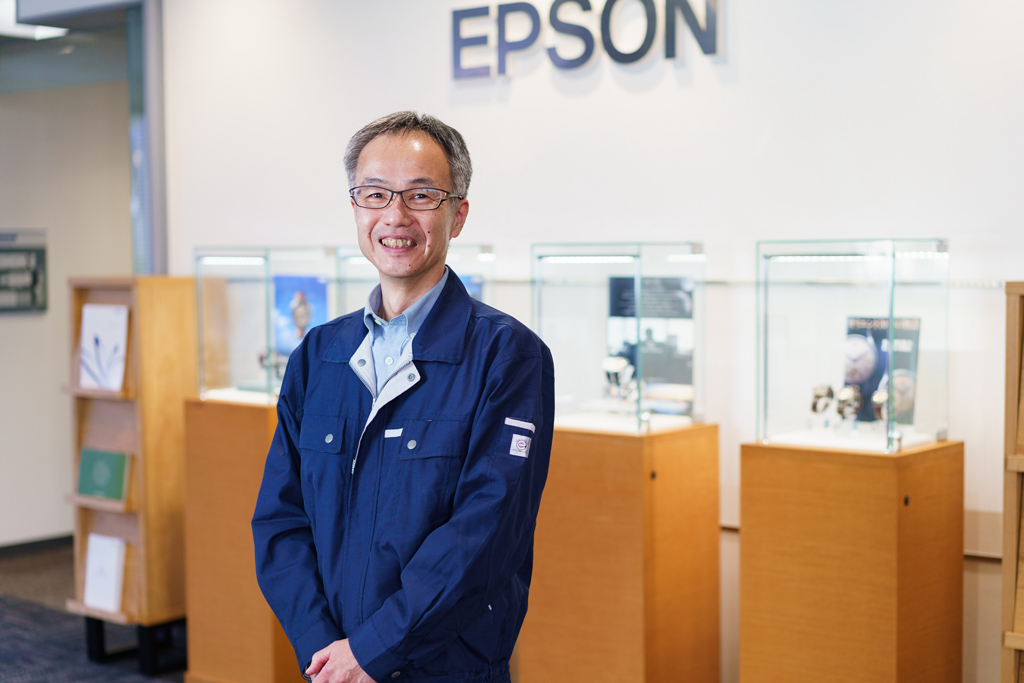
髙野改めて開発を振り返ると、苦労が多かったのが正直なところです。ただそのような苦労を乗り越え、開発された青いがんぎ車がカチカチと正確に回っているのを初めて見たときは、感動を覚えずにはいられませんでした。特に今回のF8ムーブメント搭載のオリエントスターはスケルトン仕様ですから、表裏両面ともガラス越しに私たちが感じた感動を、多くの方に味わってもらえればと思います。
記載の部署名・役職はインタビュー当時のものです。(取材:2020年11月)