Engineer Interviews
Driving the Further Evolution of Mechanical Watches
Epson's mechanical watches in the ORIENT line boast a history that traces back to 1950. In 1951, the company announced the first ORIENT STAR watch model. This was followed by many more models and technological innovations over the ensuing 70 years. Masashi Takano and Keiichi Mukaiyama, two of the people who have had a hand in these innovations, were asked about the development of ORIENT and ORIENT STAR products, as well as about the story behind the development of technology for the 46-F8 series calibers installed in the latest models.
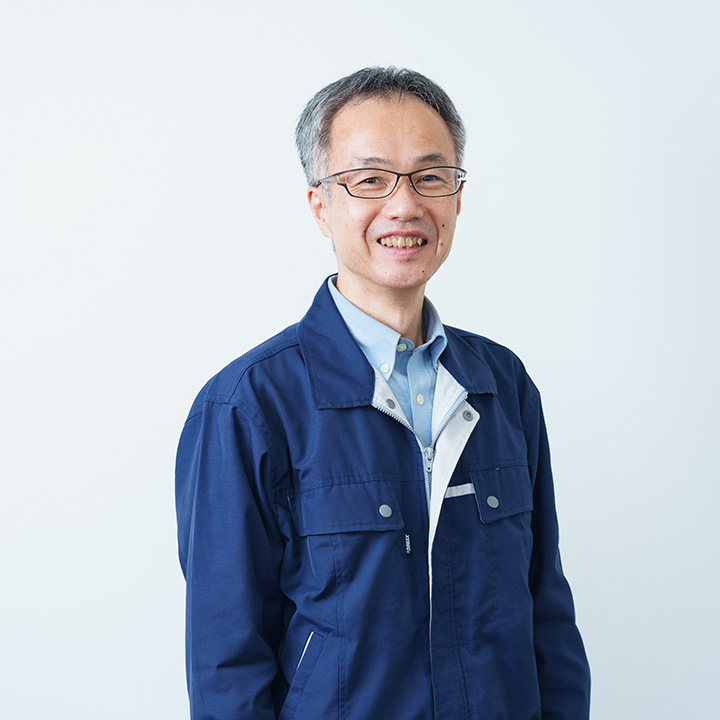
WP Development Design & Engineering Department
Takano
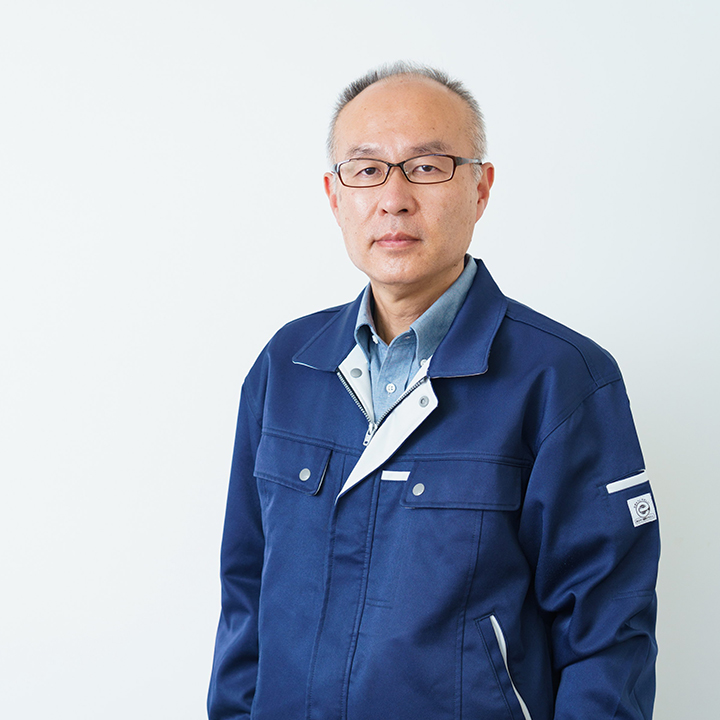
WP Development Design & Engineering Department
Mukaiyama
Genealogy of ORIENT watch movements
I'd like you to start by telling us a little about the history of ORIENT watches.
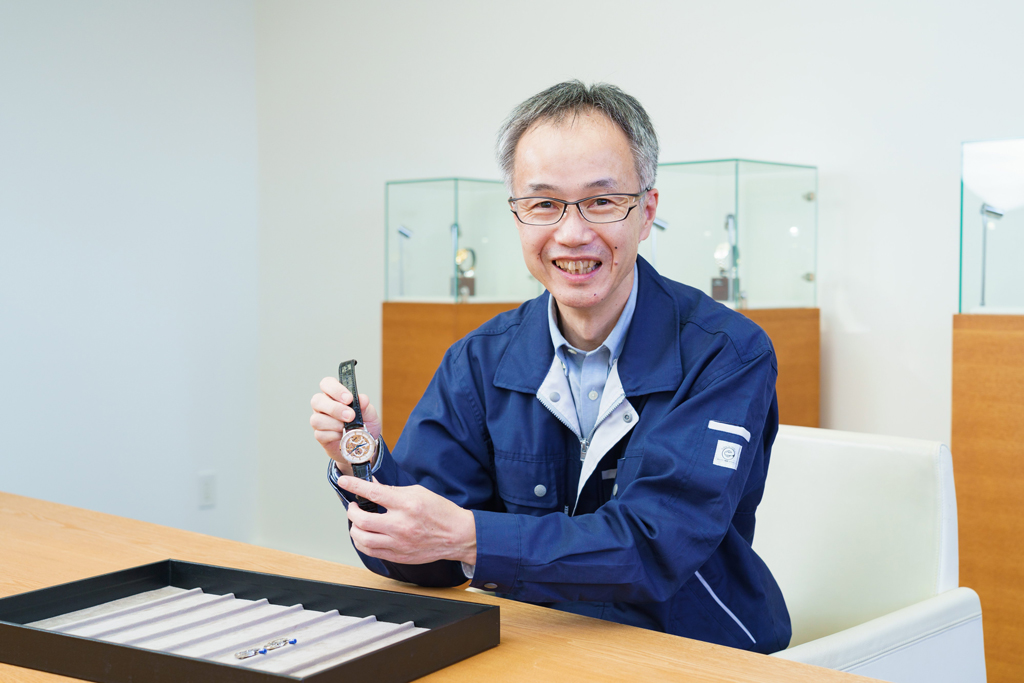
TakanoORIENT Watch Co., Ltd. produced the first ORIENT watch more than 70 years ago, in 1950. I wasn't involved in that, but I have read and heard from those who were that, after the announcement of the first model, they picked up the pace of technology development and that this work culminated in the development of the T-type, N-type, and L-type movements by the end of the 1960s.
MukaiyamaThen, in 1971, the 46 series calibers, which are used in many current ORIENT and ORIENT STAR watches, were developed. These movements have a so-called magic lever that Epson developed to provide high winding efficiency. They were engineered with simple mechanisms that enabled them to be used in many subsequent models.
Takano-On the other hand, the development of the 46 series calibers was followed, in the 1980s, by a rise in popularity of quartz watches. Technological progress not only on ORIENT watches but on nearly all other domestic mechanical watches stalled as a result. In fact, most mechanical watches were sold overseas, particularly in regions where batteries were not readily available.
MukaiyamaSo, it sounds bad, but I think it's accurate to say that we just quietly kept making mechanical watches. The simplicity of the 46 series calibers earned them favor because they were easy to maintain and could be used in many different models. However, the fact that we continued to quietly make the same movements for nearly 20 years is what rekindled later technological innovation of ORIENT watches, including the latest movement, the 46-F8.
TakanoThe situation completely changed in the 1990s. Swiss luxury mechanical watches began attracting renewed attention, and as this wave of interest increased, eyes also started turning toward ORIENT watches. This resulted in the release of many new models with newly developed mechanisms like a power reserve indicator, which indicates how much energy the mainspring has left, and a retrograde function, which indicates the day of the week with a hand that bounces backwards at the end of a week instead of going full circle.
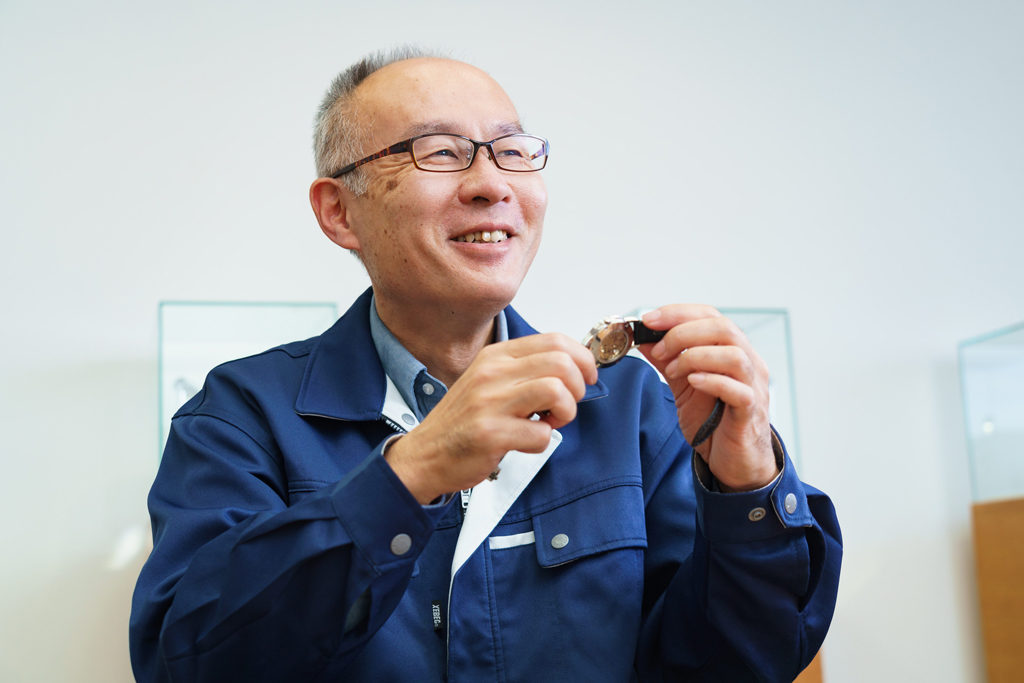
MukaiyamaIn the 2010s, a project to develop a new movement, which came to be called the 46-F6, was launched. The 46-series was developed in 1971, so the 46-F6 would be the first major movement innovation in about 40 years. The new movement was redesigned with a standardized main plate, bridges, and other parts so that these parts no longer had to be changed for each model. The production system was also overhauled.
Takano One of the most difficult challenges was to create movements both with and without a power reserve indicator using the same parts. And we were confronted with more than just technical issues. We also had to manufacture products while we were developing the new movement, so we had to closely analyze sales and find the right time to use the production lines for trial manufacturing of the new movement. Ultimately, the development of the 46-F6 turned into a two-year project.
MukaiyamaThe next model, the 46-F7, was released in 2017 and would offer improved accuracy and a longer power reserve, boosting it from 40 to 50 hours. We also decorated the movements with sharper patterns by engraving them with cutters instead of rubber whetstones. It was around this time that we also researched and developed an important part called the escape wheel.
The escape wheel was made from silicon instead of metal to increase its accuracy and reduce its weight.
What is the purpose of the escape wheel?
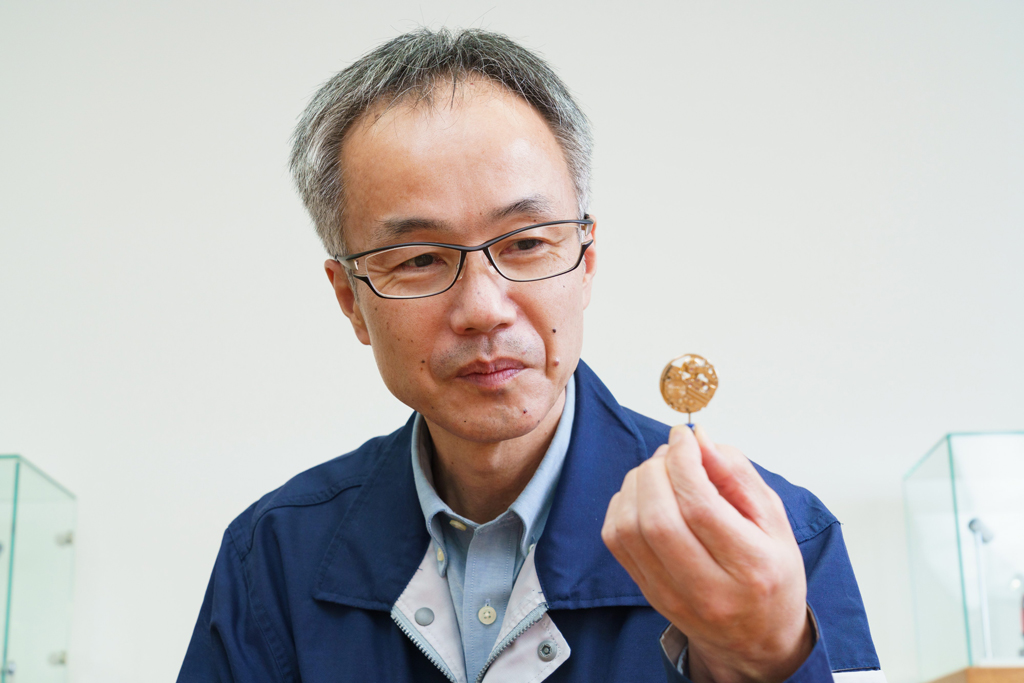
TakanoIn a nutshell, it's one of the most important parts in terms of keeping accurate time. Mechanical watches are generally made up of more than 100 exquisitely crafted parts. Each of these parts moves precisely to keep accurate time. A mainspring like that used in old wind-up toys serves as the power source. The mainspring is wound up, and the energy generated when the wound energy is released is used as the power source.
MukaiyamaEnergy is first transmitted to the gear train, which barrel complete (first wheel), center wheel, third wheel, and fourth wheel. The center wheel is attached to the minute hand, and the fourth wheel is attached to the second hand. These hands make one complete circle every 60 minutes or 60 seconds, respectively. This is the point where things get important. At the end of the wheel train is an escape wheel, followed by a pallet fork, a balance wheel, and a hairspring, which is one of the components of the balance wheel. These parts make up mechanisms called the escapement and controller unit. In other words, the escape wheel is not only the last wheel in the gear train but is also a part that makes up the escapement.
TakanoThe role of the escape wheel is to gradually use the energy of the mainspring instead of allowing it to be released all at once. It's the movement of the escape wheel that literally ticks off the accurate time. You can imagine it as the escape wheel, pallet fork, and balance wheel reproducing the movement of a pendulum clock.
What did the research and development of the escape wheel entail, specifically?
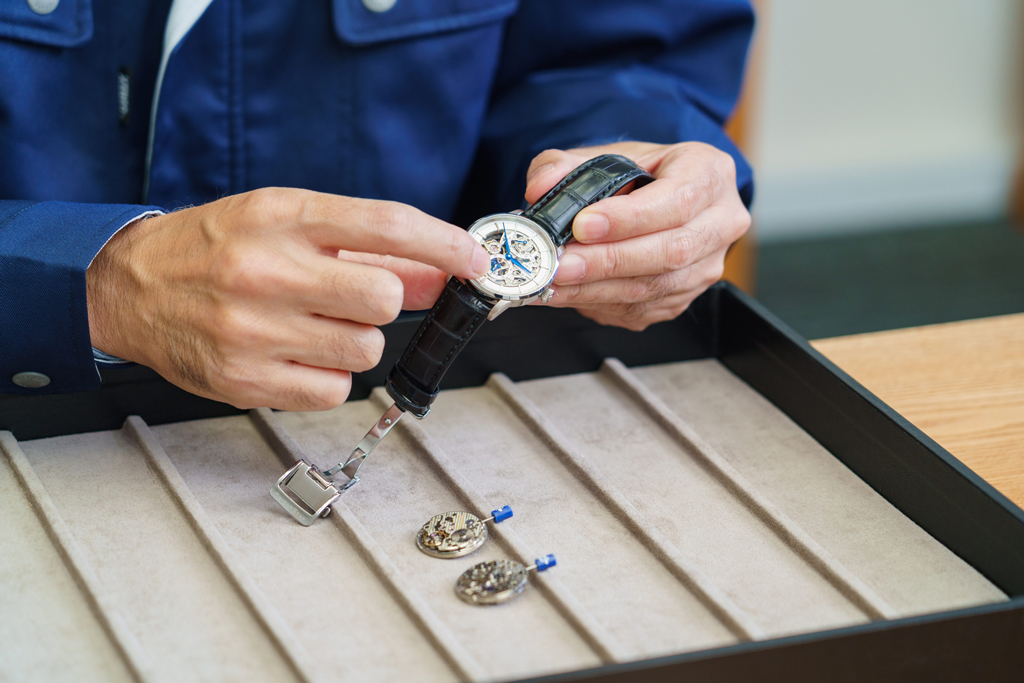
MukaiyamaBroadly speaking, there were two main themes. One was to further increase the drive time. The other was to improve the accuracy of the escape wheel.
To increase the drive time, we needed to reduce the power loss of the escapement, which consumed about half of the energy obtained from the mainspring.
Takano There are several reasons why the escapement consumes half of the power, but one of them is weight. In the movements up to the 46-F7, the escape wheel was made of a metal called nickel silver. The escape wheel was thus heavy and used up power to move.
Takano Frictional force between the pallet stones and escape wheel was another source of power consumption. Pallet stones are installed at the tips of the pallet fork, which connects the escape wheel and balance wheel. The pallet stones are made from synthetic rubies, which are durable enough to withstand long hours of driving. If the amount of engagement between the pallet stones and the escape wheel was the conventional processing accuracy of one one-hundredth of a millimeter, a certain margin, which we call the amount of clearance, would have to be provided in the design. Naturally, that clearance became an extra load, which also generated frictional force that was expended by the pallet stones and the escape wheel. Therefore, in order to solve the problems of weight and dimensional accuracy, we decided to begin developing a silicon escape wheel, something with which we had no prior experience.
Success in manufacturing a silicon escape wheel using MEMS processing
Is a silicon escape wheel common in watches?
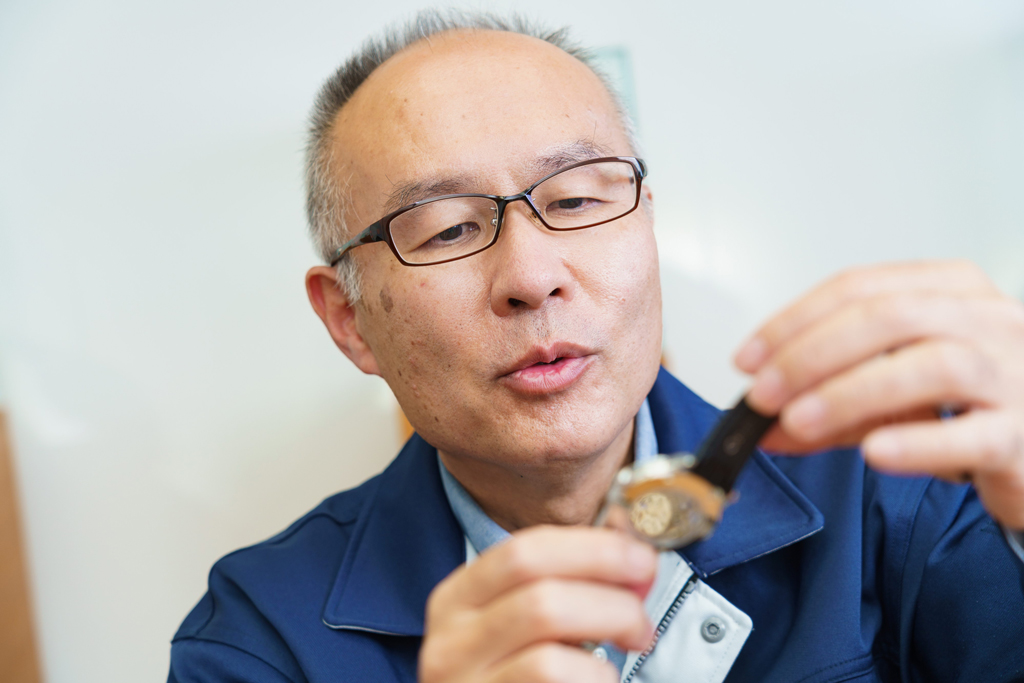
MukaiyamaSome Swiss watchmakers use silicon escape wheels, but I think we were the first in Japan to attempt their manufacture. However, the Watch Operations Division did not have the capability to make silicon parts. Therefore, we sought the cooperation of Epson's Technology Development Division, which we knew had silicon processing expertise. We worked with them to develop a silicon escape wheel by using the MEMS fabrication technology that is also used to manufacture components such as Epson's printheads.
Where did you run into difficulty in development?
TakanoSilicon has a low relative density-about one-third that of the nickel silver we used for metal escape wheels. Since it is a glass-like material, it is brittle and easily chipped. So, one of the biggest technological challenges was to make the escape wheel lighter while still maintaining the required strength. The solution was a film.
A film?
MukaiyamaWhen silicon is thermally annealed, a silicon-dioxide film forms on the surface. This film is removed and then again thermal oxidation is performed. We found that when this process is repeated, the silicon surface becomes rounded, corners are removed, and a silicon-dioxide layer forms on the surface. The changes reduce the brittleness and susceptibility to chipping. As a result, we succeeded in making an escape wheel that is even stronger than a metal escape wheel.
TakanoMEMS fabrication increased processing accuracy to one one-thousandth of a millimeter. As a result, we were able to reduce the amount of engagement by 80%. Furthermore, switching from nickel silver to silicon reduced the weight of the escape wheel by around 65%. However, there was another issue that also needed to be addressed.
New patented technology was acquired through R&D on silicon escape wheels.
What kind of issue?
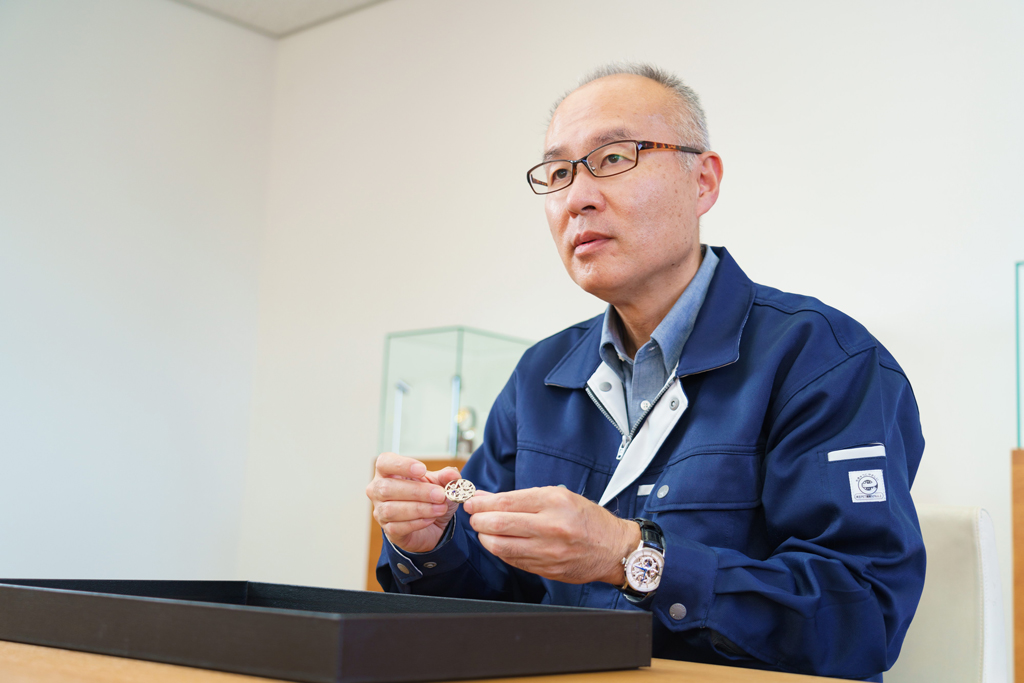
MukaiyamaThere was an issue caused by the susceptibility of silicon to chipping. It became necessary to adjust the pinion that is inserted in the center of the escape wheel. The pinion, like the earlier metal escape wheels, is made of metal, so it could be forcefully tapped into place.
TakanoHowever, when we tried to secure a silicon escape wheel with a metal pinion, the escape wheel broke. Conversely, if you don't use as much force, the pinion will not be able to hold the escape wheel properly and accuracy will deteriorate. So, we mulled over potential solutions. The idea we came up with was to disperse the force and prevent breaking by lending springiness with the configuration of the escape wheel.
That was an innovative idea.
MukaiyamaHowever, we had to determine what configuration would actually be best. The idea was good, but the journey from there to actually designing an escape wheel with a configuration that would actually resist breaking was not so easy. In addition to reviewing ideas with people in the Technology Development Division, we made dozens of escape wheel prototypes in our search for the optimum configuration. We arrived at the current configuration through this process of trial and error.
It is a unique configuration.
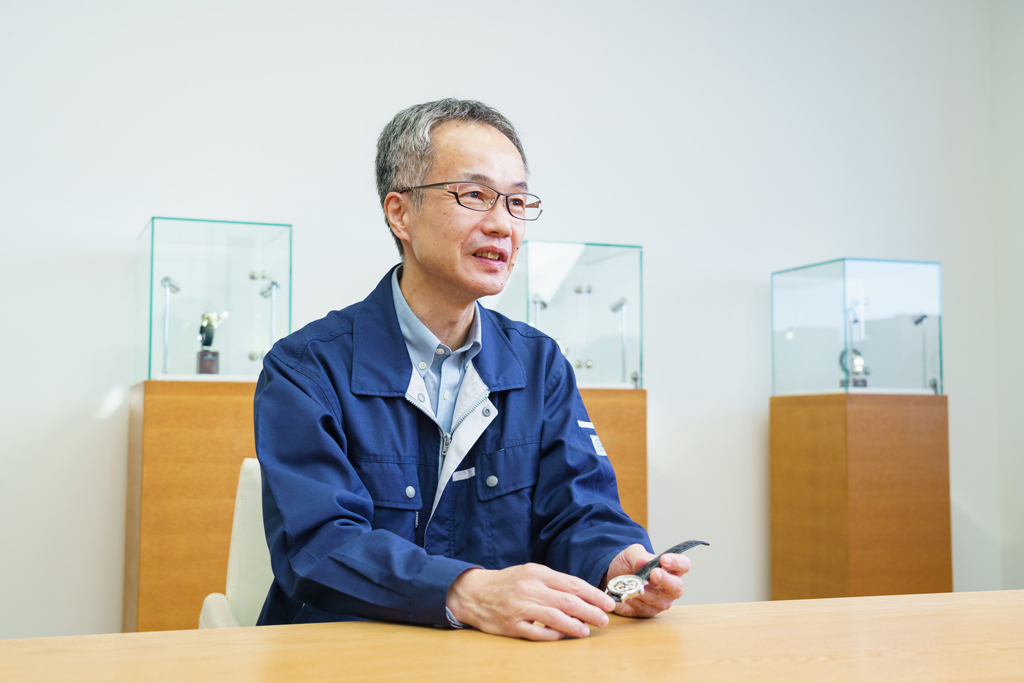
TakanoThe escape wheel was made springy in places by designing it with windmill-like vanes. In addition, the configuration of the part of the escape wheel that is in close contact with the pinion is like the tip of the bristles on a toothbrush. The pinion was also redesigned and slits were added so that the pinion would mesh with this uneven configuration. This process of trial and error resulted in a new escape wheel and pinion that disperse force as they mesh. This design is also patented.
Achieving a bright blue color with technology for controlling film thickness on a nano-level.
It seems that since the new 46-F8 movement is used in skeleton models, you also took a lot of care in terms of the appearance.
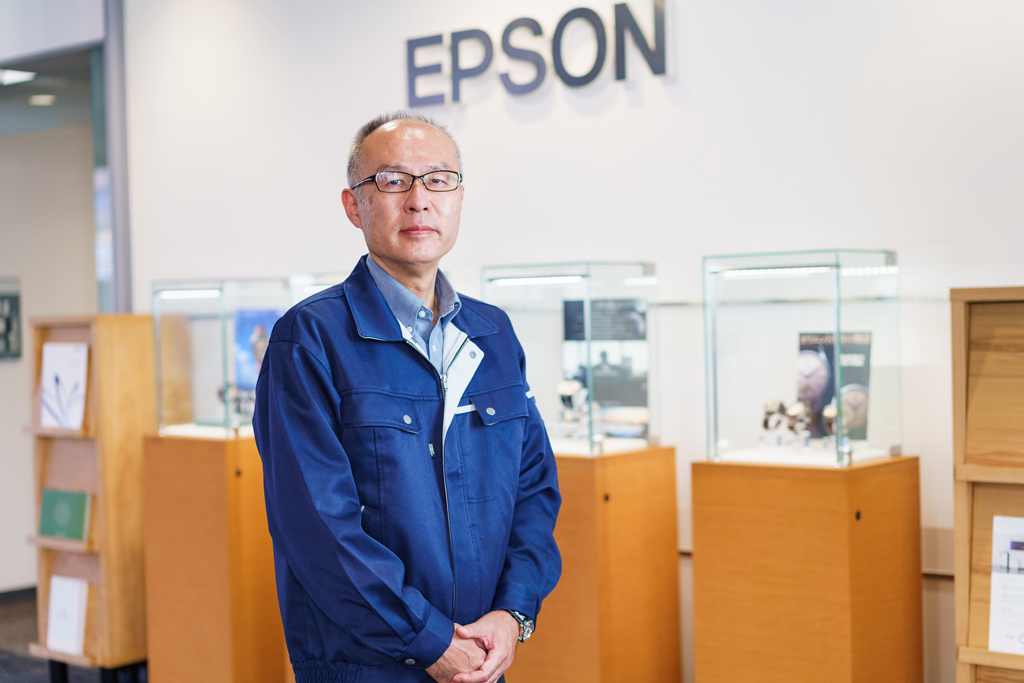
MukaiyamaWe did. Here, too, the Technology Development Division's nano-level film thickness control technology played an important role. In addition to the oxide layer mentioned earlier, multiple layers of polysilicon film were also formed for more vivid color development. The result is a bright blue escape wheel. Incidentally, the reason we made it blue was that the shape of the escape wheel resembled a galaxy and the blue was reminiscent of the Milky Way.
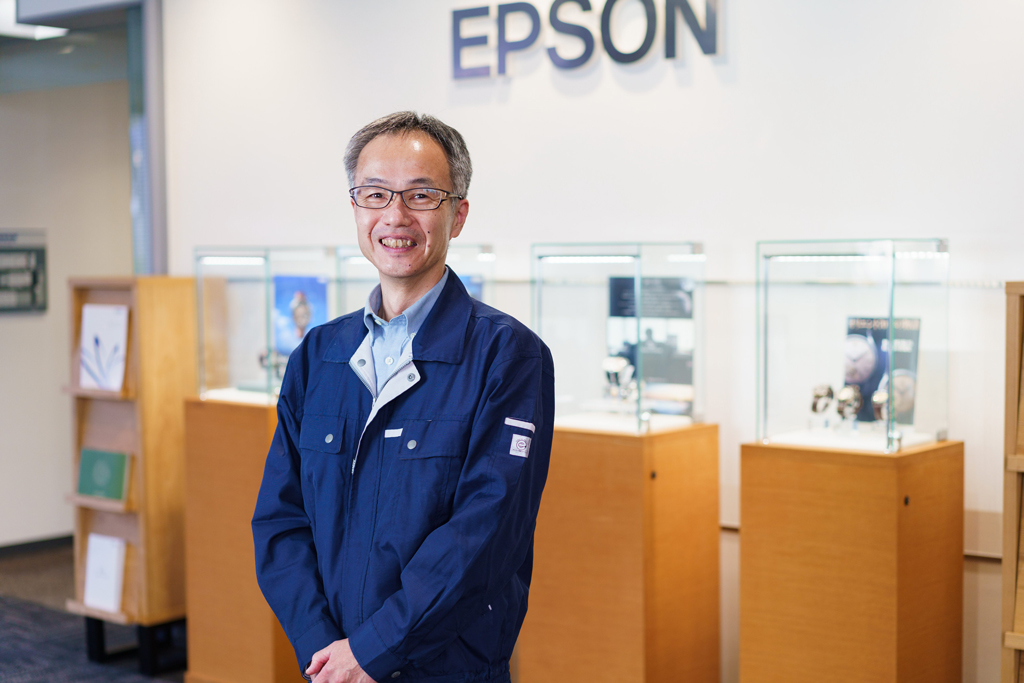
TakanoNow that I think back on it, honestly, we struggled a lot during the development stage. But, after overcoming all the hardships, the first time I saw the blue escape wheel precisely rotating, I couldn't help but be impressed. The ORIENT STAR models equipped with the 46-F8 movement have a skeleton design, so I hope that people will experience the thrill that we felt when we first saw the movement through the crystals on the front and back of the watches.
The titles and positions are as of the time of interviews in November 2020.