Keeping tradition alive

Creating Value That Exceeds Customer Expectations and the Monozukuri Juku
Epson's Monozukuri Juku, or Manufacturing School, aims to enhance the customer value we create. To this end, we teach our personnel basic technology and skills and have them experience monozukuri (the art and science of manufacturing) by performing specific manufacturing tasks step by step. This helps them tackle jobs from different angles. To give a specific example, employees learn the basics of component processing technology (molding and pressing). Once they learn these, employees have the skills to make the various parts that go into a product. Employees also learn by mastering essential skills for making production lines more efficient (e.g., automating lines or operating them with fewer staff).
In addition, we contribute to the community and society by giving practical training for new employees of local businesses, offering corporate experiences to junior and senior high school students, and providing instruction for technical skill trainings. We also send experts abroad to take part in official development assistance for building technical skill evaluation systems at the request of the Japanese Ministry of Health, Labour and Welfare.
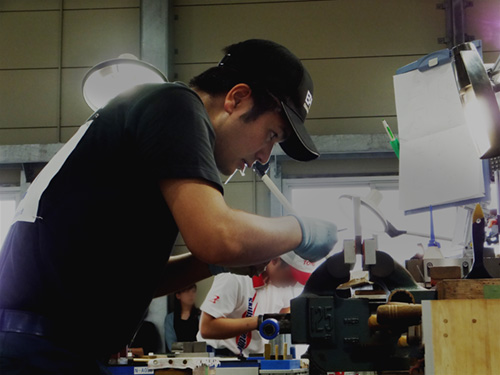
Mechatronics Training for Building, Maintaining, and Enhancing Automated Lines
Factory productivity improvement initiatives are nothing new at Epson. Earlier examples included the introduction of simple and systematic tools to production processes. More recently, however, we are facing great changes in the manufacturing environment. As wages have risen rapidly and workers prefer non-manufacturing jobs, it is not always easy to recruit the necessary labor. Earlier improvements were based on the assumption there would be plenty of inexpensive labor. Our business is not likely to survive if we just try to repeat such improvements. Therefore, we are making a strong push to build production lines that rely on human labor as little as possible but are still capable of stable production.
Monozukuri Juku holds about 100 trainings of various types each year to develop the engineers who keep production lines running. Trainings impart machining skills like mechanical drafting and measuring required to build equipment. The organization prepares such curricula as mechatronics basic technologies, where engineers who promote manpower-saving and automation technology get training in basic technologies like compressed air and electrical control as well as assembling and adjusting simple devices. Other courses include FA robot training, image processing training, and mechatronics practical training, which are designed to teach practical technologies and skills. Thus, we are offering employees an opportunity and place to learn.
Monozukuri Juku trains machine tool and maintenance engineers in Japan but also sends staff to teach at overseas affiliates that serve as our major manufacturing sites. There, we develop leaders in production and machine tool maintenance at overseas affiliates, by giving courses based on our training program in Japan.
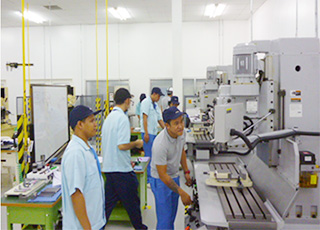
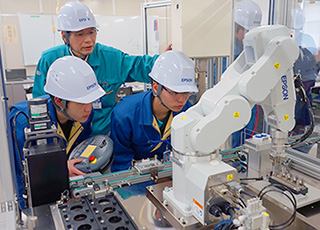
Developing Young Technicians through National Skills Competition
As a manufacturing company, Epson uses training for WorldSkills competitions to develop "groundbreaker technicians"*1 who have acquired essential manufacturing knowledge and skills at an early age. As a rule, individuals are allowed to take part in WorldSkills trainings just once. The purpose of the short-term intensive trainings is to help participants learn technical skills at the all-Japan level. Every year we send 10-15 individuals to the National Skills Competition associated with WorldSkills to compete in six selected occupational categories that are applicable to our employees' work: Instrument making, Press tool making, Mechatronics, Industrial electronics, Web design, and Watch repair.
New employees sent to Monozukuri Juku as WorldSkills trainees experience monozukuri (the art and science of manufacturing) in such forms as filing and sawing. They also learn basic knowledge about machinery, electricity, and other general topics in each occupational category. In conjunction with everyday occupation-specific training, there are training camps three times a year. Participants lodge together, run a long distance, set targets, and the like. All of this helps to build a sense of solidarity as a team.
To recreate the feel of the national competition, we also hold joint training events with other companies that take part in WorldSkills. Additionally, our employees actively pursue such national qualifications as machining technician, electronic device assembly technician, web design technician, and watch repair technician. After participants finish WorldSkills trainings, they get practical training to help them build the basic skills learned there into skills they can use to make products. Each participant then joins an operations division. The units they join often praise these employees for performing beyond expectations.
*1 Technicians with the ability to break from precedent to create innovative technologies and systems
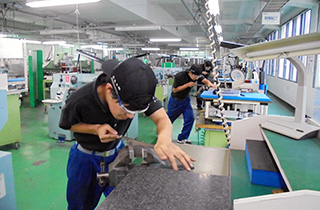
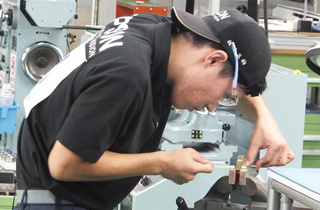