Engineer Interviews
Epson innovation: Integrating robotics with sensing technology
Epson's robotics business once focused on automating the assembly of Epson watches. Nowadays, it engages in the manufacturing of electronic products such as mobile phones and other small precision instruments. Robots must assemble the tiny components of such products with minute precision, as the slightest vibration or misalignment will directly affect the quality of the product. To solve this challenge, Epson has integrated robotics with its original sensing technology to create robots that achieve excellent locomotive performance and are easy to control. Thanks to these robots, operations that once relied on manual labor and human senses can now be automated, resulting in better precision and speed.
We interviewed two robotics engineers about the advantages and applications of robotics. We also discussed the circumstances in which they developed the gyroscopic sensors and force sensors used to control the robots.
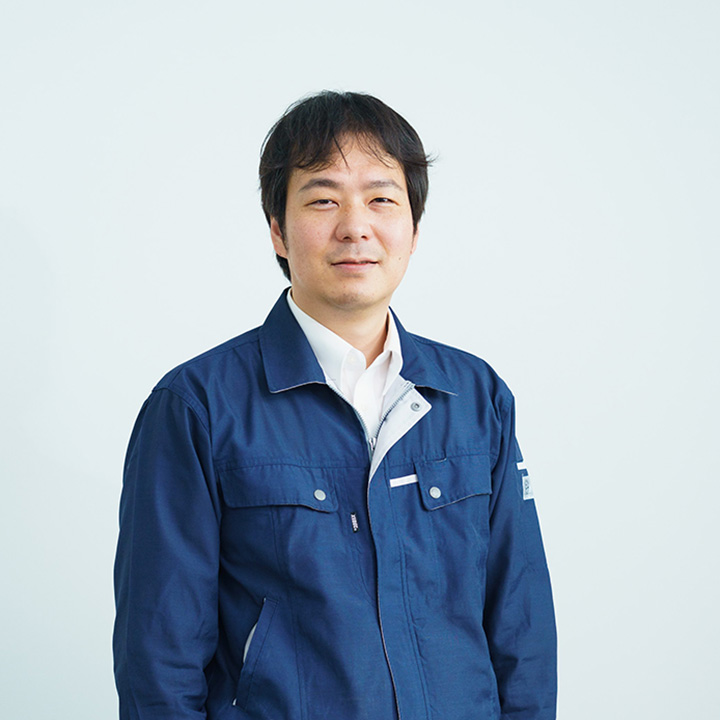
RS Planning & Design Department
Motoyoshi
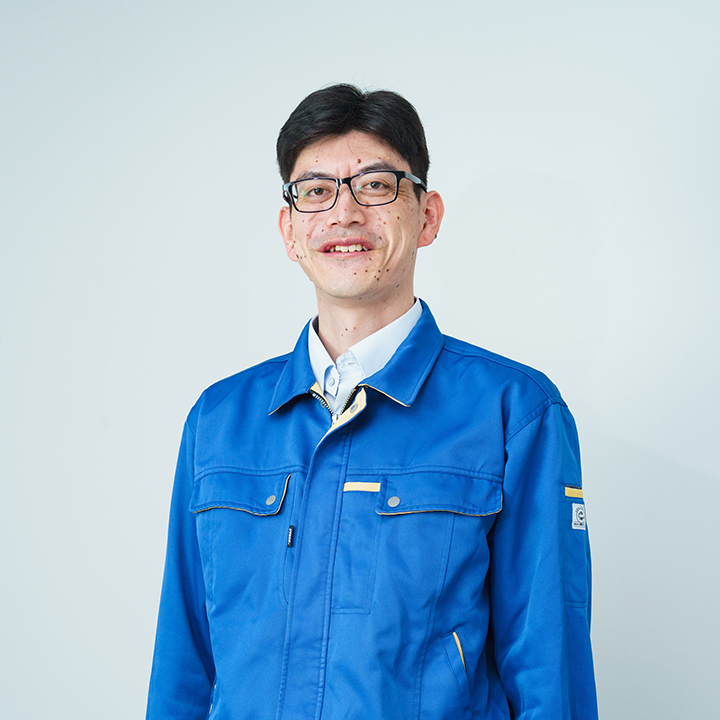
RS Planning & Design Department
Kawai
Improving speed and precision by automating processes that once relied on human senses
What are the advantages of Epson's robotics?
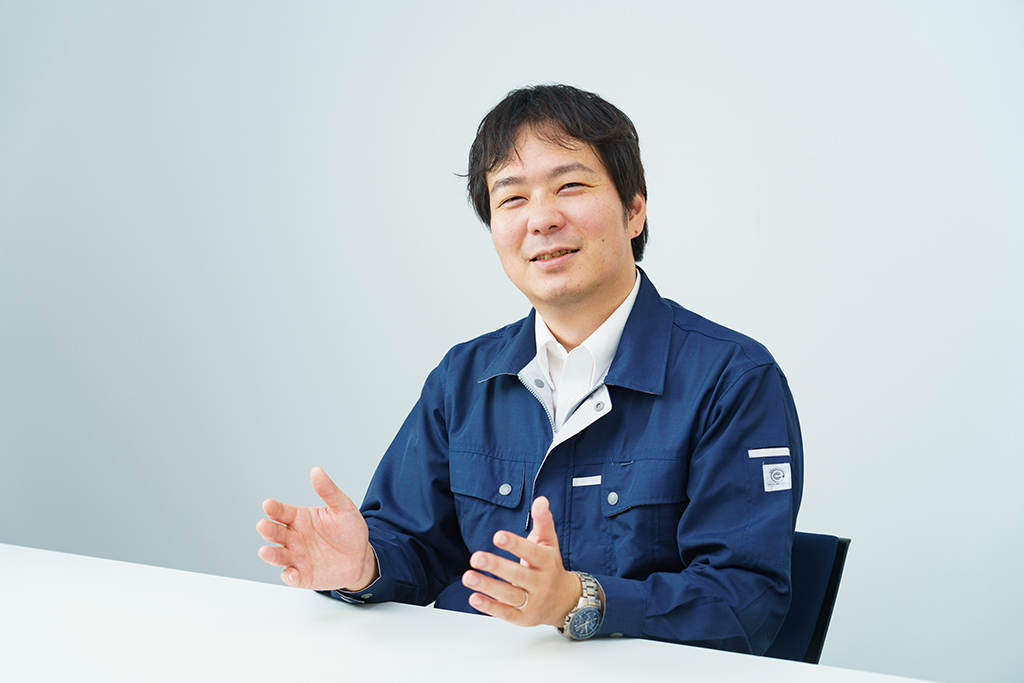
MotoyoshiInitially, Epson designed robots to automate the process of assembling watches. In this respect, our robotics technology had different origins from than that of other manufacturers. Most manufacturers introduced industrial robots to lift payloads that were too heavy for humans or to perform operations that would be hazardous to human health. In Epson's case, the focus was always on speed and precision. Our robots were initially designed for high-precision tasks that had previously relied on human senses. Subsequently, we achieved a huge leap in robotic performance by equipping the robots with gyroscopic sensors and force sensors. We developed these sensors using Epson's original quartz crystal devices.
Tell us about the circumstances in which you came to develop the gyroscopic sensor-based control technology and force sensors. What challenges did you face?
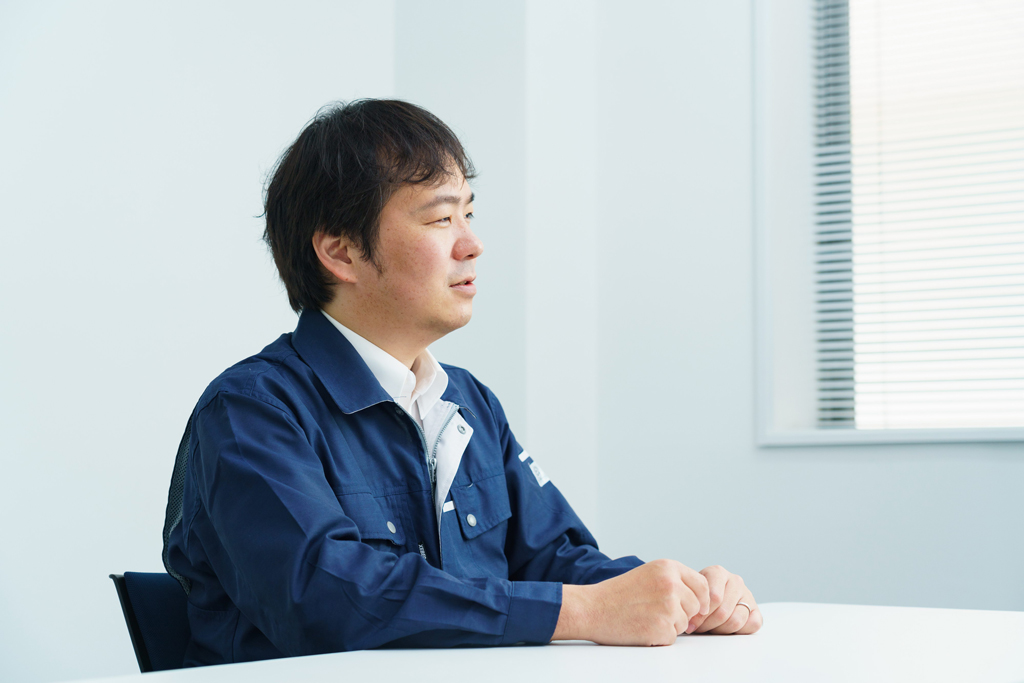
MotoyoshiEpson has always prided itself in speed and precision. To improve speed and precision, you must do more to suppress vibration. The conventional method for controlling robots involves the use of a servomotor to provide feedback on the angular position of robotics joints. The problem with this method is that even if all the motors are aligned correctly, the robotic arm can still get contorted, causing the tip of the arm to vibrate or deviate from its target position. To solve this problem, we started using gyroscopic sensors to detect vibrations directly and communicate this information to the motor controls. This system enabled us to minimize vibration without needing to make the arm more rigid.
Initially, though, there were no gyroscopic sensors small enough to fit the robotic arms. Accordingly, we developed a tiny gyroscopic sensor using our original quartz crystal technology. Mounting the gyroscopic sensor onto the robotic arm proved challenging due to the sensor's attributes. However, we overcame this challenge and produced a gyroscopic sensor compatible with the robots.
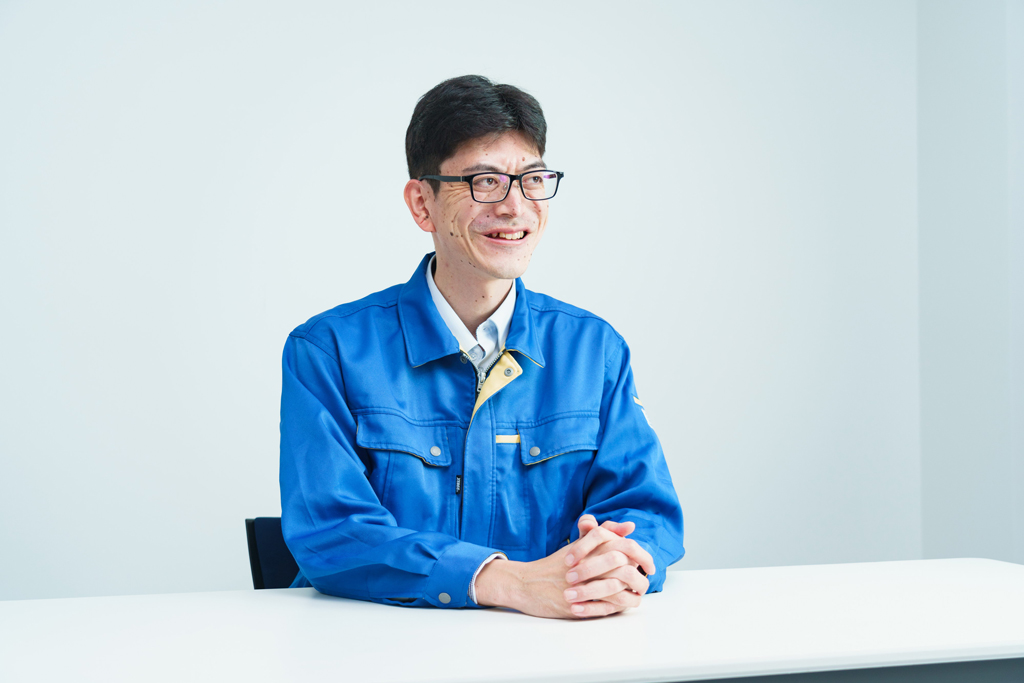
KawaiMany high-precision tasks, such as inserting tiny parts into slender gaps, were once performed manually, using human senses. The market was crying out for a way to automate these processes. We saw force sensors as a solution to this need.
Force sensors were already available on the market at the time. However, they were not rigid enough. When you exerted force upon the sensor, it would contort and deviate from the target position. They also had poor resolution, making precise locomotion impossible. Fragility was another issue. Sensors need to be shock-resistant because they move with the robot. In the end, we decided that if the market lacked any force sensors with the required rigidity, resolution, and shock-resistance, we would develop one ourselves. The result was the Epson force sensor.
Our force sensors use quartz crystals to combine rigidity with sensitivity. By embodying these paradoxical aspects, the sensors have enabled the automation of delicate and precise assembly processes that manufacturers once thought impossible to automate and for which they had relied on human senses. Examples include plugging in flexible flat cables (FFC) and inserting capacitors.
Making robotics accessible to all
-The scope of robotics-In what areas are robotics applied today? What are the future applications?
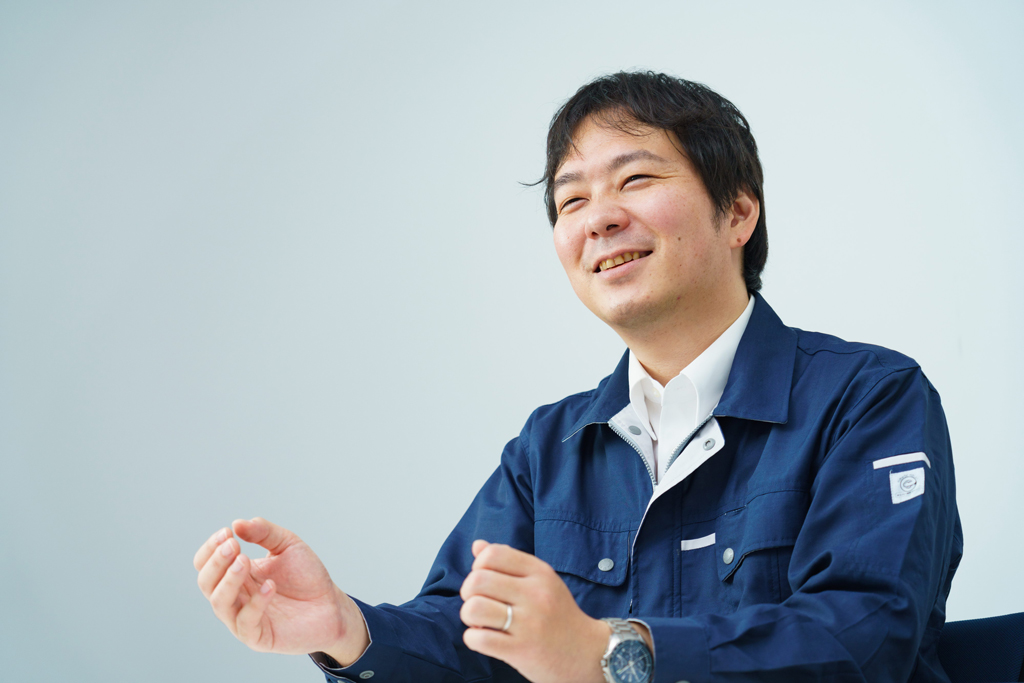
MotoyoshiThe most common applications today are in electronics assembly and transportation. Beside these, Epson's SCARA robots feature prominently in other areas requiring precision, such as the manufacture of precision instruments and medical instruments. We have built a strong market share in these fields. The market has grown rapidly at a global level. Many companies around the world are suffering from labor shortages and turning to labor-saving solutions. This socioeconomic trend suggests that robotics is no longer the preserve of large manufacturers-they will increasingly feature among small- and medium-sized enterprises too.
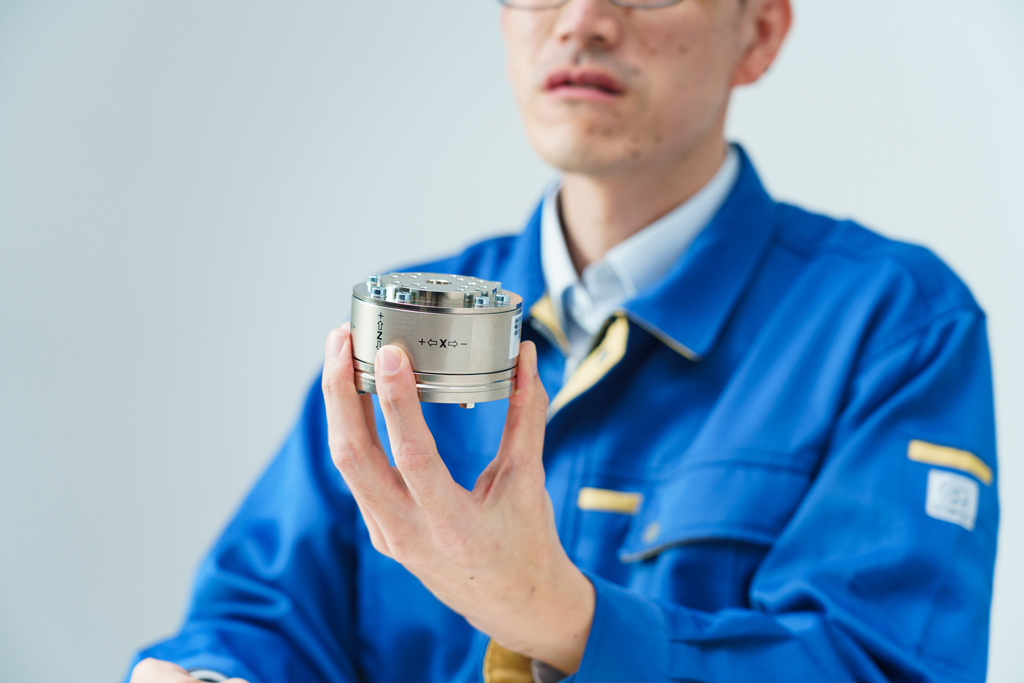
KawaiFor companies that are struggling amid a labor shortage,
robots are a boon. You can program robots to perform sophisticated processes repeatedly and consistently. You
could then get a second or third robot to perform the same process alongside the first robot, thereby doubling
or trebling the speed.
Another advantage is that a robot's sensor can provide you quantitative feedback of
its sensory input. The robot logs the sensor data for production or distribution processes, so if something
goes wrong, you can back-trace and identify when, where, and how the error occurred. Robotics also has
applicability outside automation: Robots could quantify the artisanal techniques of master craftspeople,
helping apprentices to inherit their craft.
As the market grows, what requirements will robots need to fulfill?
MotoyoshiIf the robotics market does indeed grow, robots will soon become accessible not only to skilled robot operators but also to the layperson. Take, for example, a robot's speed setting. In the past, it would take a skilled robot operator to set the speed at just the right level for ensuring both optimal performance and minimal vibrations. Nowadays, the robot can set its speed automatically, meaning that operators have a much easier task. Robots will need to be even more user-friendly so that they are accessible to all. To that end, we are exploring the potential of AI solutions based on our sensor and other original technology.
Additionally, robots will need to work in confined spaces. This requirement will become increasingly crucial as demand for small-lot production rises and more small and medium enterprises adopt robotic automation. To develop flexible robots that can fit into any space, we must go even further in the areas where Epson has always excelled: compactness, lightness, slimness, and energy efficiency.
Going further in sensing and robotics to meet societal needs
What kind of world will become possible through Epson's robotics?

MotoyoshiOur robots have minimal vibration, require little human input, and are easy to install. As well as solving the problem of labor shortages, they can help ensure that specialized techniques are transmitted to future generations. To meet the needs of the market, we will continue upgrading our robotics technology. Specifically, we will leverage our force sensors, gyroscopic sensors, and other technology assets to enhance the performance of robots on the factory floor, focusing as always on speed, precision, and quality.
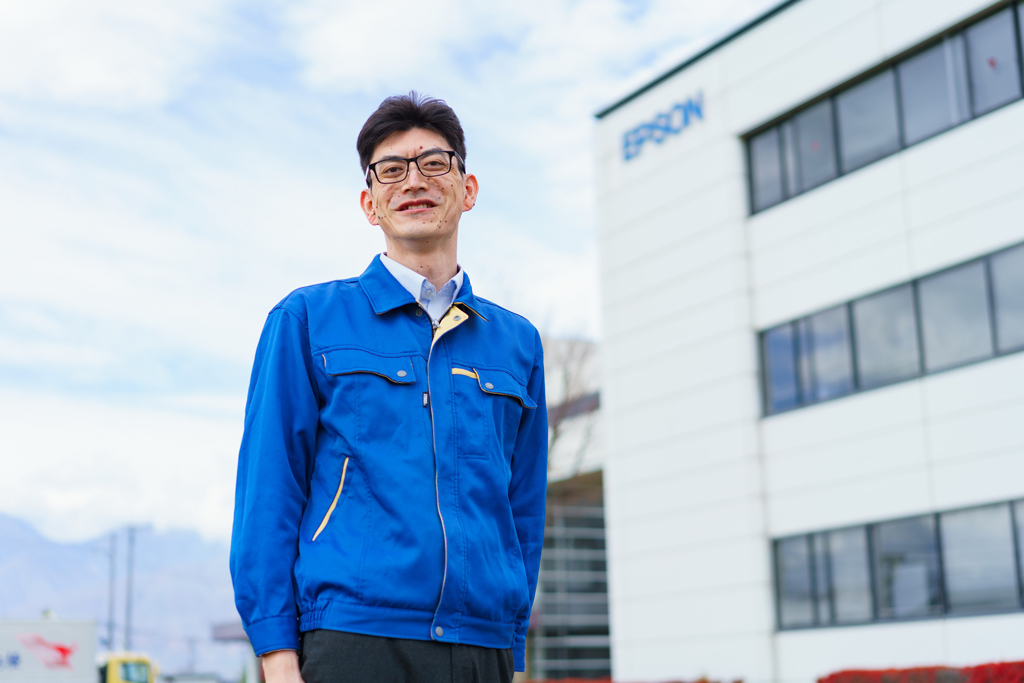
KawaiAlongside Epson's commitment to efficient, compact and precision technologies, our various businesses have amassed a smorgasbord of technologies and devices, including image processing technology and sensing technology. If we combine these assets with the expertise we have gained in automating production, then we can create peerless, inimitable robots that are fast, precise, compact, lightweight, slim, energy-efficient, and user-friendly. These robots will enable automation in the delicate and precise manufacturing processes once written off as impossible to automate. We will continue refining our technologies to enhance the value of the automation and manpower-saving solutions they support. In this way, we will continue contributing to the development of a range of industries.
The titles and positions are as of the time of interviews in November 2020.