Engineer Interviews
The Future of Gyro Sensors in Applications
that Make the World Safer and Better
Epson is one of the world's biggest developers and manufacturers of crystal devices. We produce a variety of devices, such as timing devices used in clocks, communication equipment, computers, and smartphones. Other examples are gyro sensors that are used in vehicles and cameras to detect angular velocity, and inertial measurement units, to which the gyro sensor technology is applied. As these examples illustrate, crystal devices feature in products that we use in our daily lives.
We interviewed Norifumi Shimizu, who is responsible for the gyro sensors for vehicles (auto gyro sensors), including those that keep the car under control and those that control car safety features. We asked Shimizu about what makes the auto gyro sensors so special, what their future outlook is, and about his experience in developing the devices.
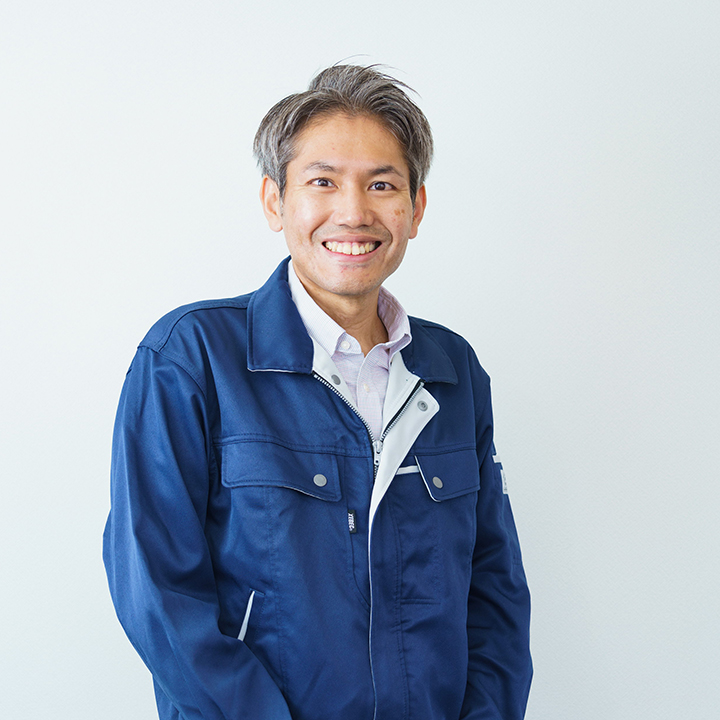
Shimizu
Gyro sensors make driving safer
Tell us about the products you work on and their characteristics.
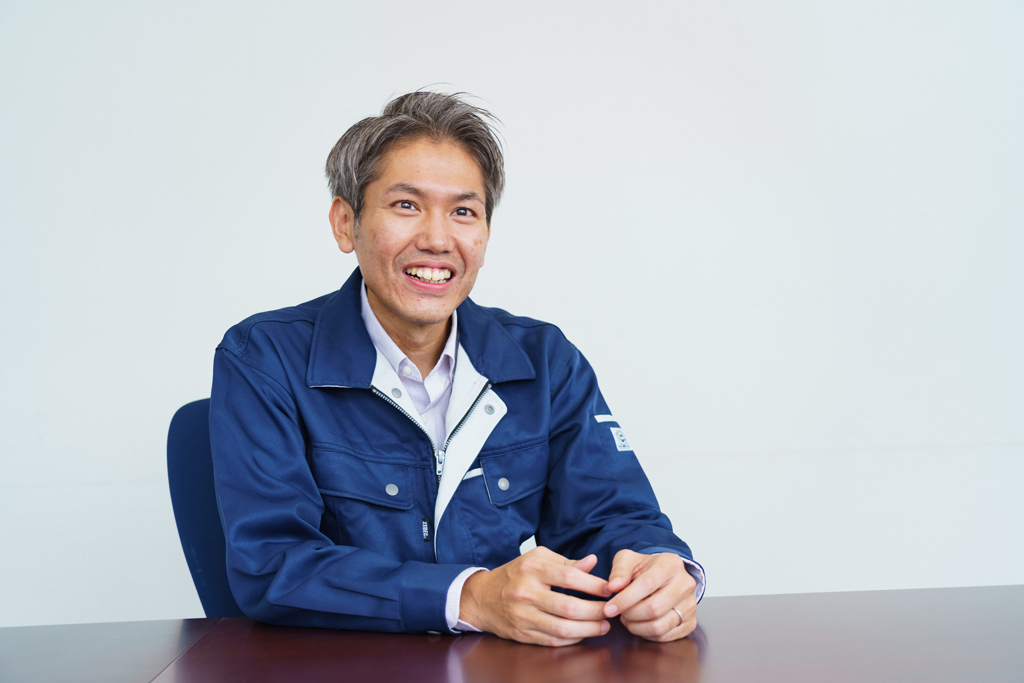
ShimizuGyro sensors are devices that sense angular velocity which is the speed at which the angular position of an object changes. They have many applications. Large gyro sensors are used in rockets, aircraft, satellites, and ships. Smaller ones serve in smartphones, game controllers, and digital cameras.
The gyro sensors I work on are for car safety features, including anti-skid braking systems and side-impact air bags. We get repeat orders for our gyro sensors because they demonstrate exceptional stability in all driving conditions.
For gyro sensors, stable operation is paramount, and this is especially true in vehicular applications. Auto gyro sensors are only worth having if they perform just as stably in adverse driving conditions as they do in favorable ones. Otherwise, the results really could be fatal. Suppose, for example, that you are driving along a rough road. Unless the sensor performs stably in these conditions, the jolts might cause the airbags to activate or cause the car to go out of control. We wanted to ensure that this would never happen with our gyro sensor. Using Epson's proprietary hammerhead-type crystal sensing element, we created a gyro sensor that performs stably even when subjected to vibrations. The gyro sensor uses quartz crystal. Because this material is stable under a range of temperatures, the gyro sensor can perform stably in both hot and cold driving conditions.
By providing gyro sensors that are resilient to environmental changes, we make driving safer and ultimately more comfortable.
From consumer markets to the auto market
What was the inspiration behind the auto gyro sensors?
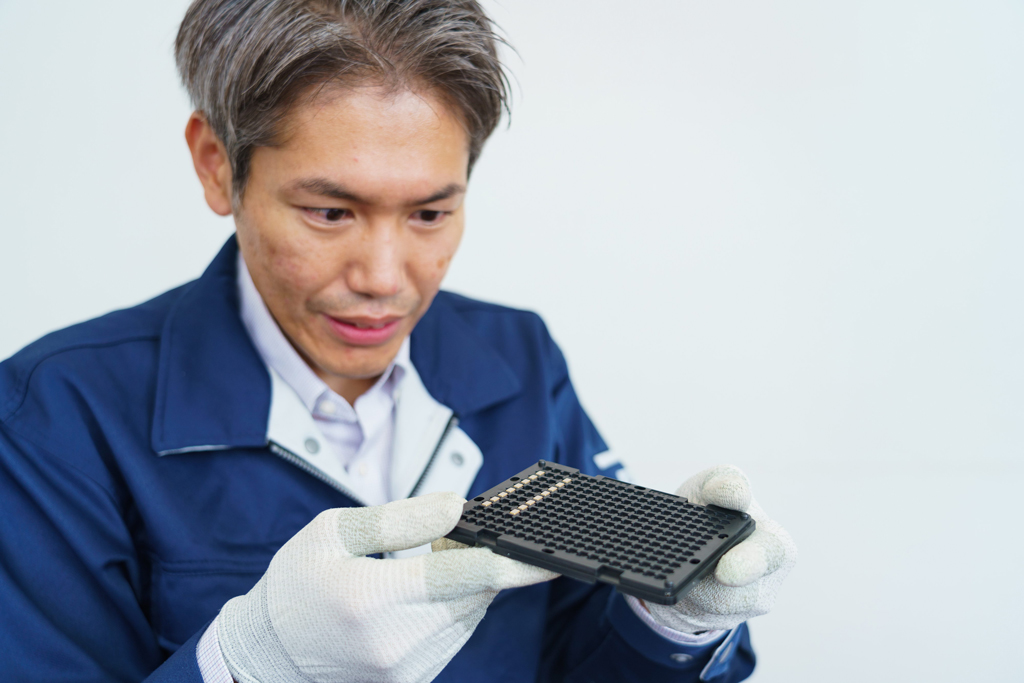
ShimizuWe have come very far in developing consumer applications for Epson's crystal devices. Starting from wristwatches, we later expanded to mobile phones and computers. The same goes for gyro sensors. We initially focused on camera-shake correction devices and game controllers and then expanded to car GPS navigation systems. Inbuilt car features was next on our list of target markets.
What challenges did you face in developing the product?
ShimizuOur lack of experience in car safety proved a hurdle at first. We had a decent track record in the GPS navigation systems market, having carved out a large share there. However, we had no experience in measuring the angular movement of cars, a task that required the gyro sensor to perform even more reliably. Consequently, our own evaluation environment was inadequate, and we struggled to get the business up and running.
We faced another challenge too. If we wanted the customer to use our gyro sensor for measuring the angular movement of cars, we would need to demonstrate that the sensor can withstand all kinds of driving conditions. We started by identifying the kinds of environmental stress the sensor is vulnerable to, the extent to which it can withstand these stresses, where breakage starts to occur, and what happens when it does occur. Next, we consolidated all this information and made improvements where necessary. Finally, we briefed our customers thoroughly to win their trust. The customers were convinced and decided to go with our product. To achieve the high standards that the customers expect, we have developed an in-house quality control system that spans departments including design, engineering, manufacturing, quality management, and sales. This system has become a most valuable asset for Epson.
Gyro sensors that contribute to society
What is the future outlook for gyro sensors?
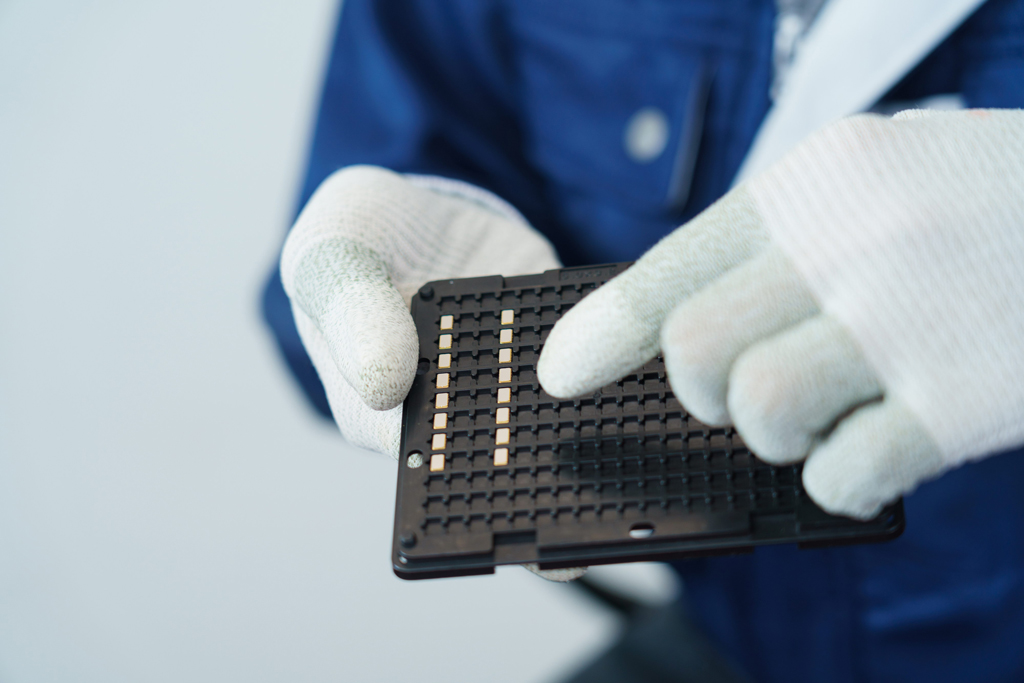
ShimizuEpson's gyro sensors are exceptionally accurate and stable, but we are still looking to improve.
The automotive sector is full of exciting possibilities. Automated driving and advanced drive-assistance systems (ADAS) are progressing, and these technologies are increasingly being installed in vehicles. Human-driven vehicles will soon be a thing of the past. Our business strategy has focused on the automotive sector, but only in terms of car safety features, such as side-impact airbags and anti-skid braking systems. For our next step, we will target advanced vehicle control. We have developed high-accuracy gyro sensors for consumer markets. If we extend this technology to applications related to automated driving and ADAS, we could produce sensors that detect subtle vehicular movements that conventional sensors would miss. In this way, we will enable stable vehicle control and thus contribute to safer and more comfortable driving.
There is another market we want to target in the future. Specifically, our sensors have potential to form part of an inertial measurement unit (IMU) for monitoring the state of large structures or machinery. Such an IMU could, for example, monitor the angular velocity of a structure and issue an alert when it detects an abnormality. It could also estimate the deterioration of machinery. Until now, the user has performed these tasks, but in the future we can envision device makers taking on these tasks.
End-to-end crystal device production
from raw crystal to the finished product
What would you say to people who use Epson's crystal devices?
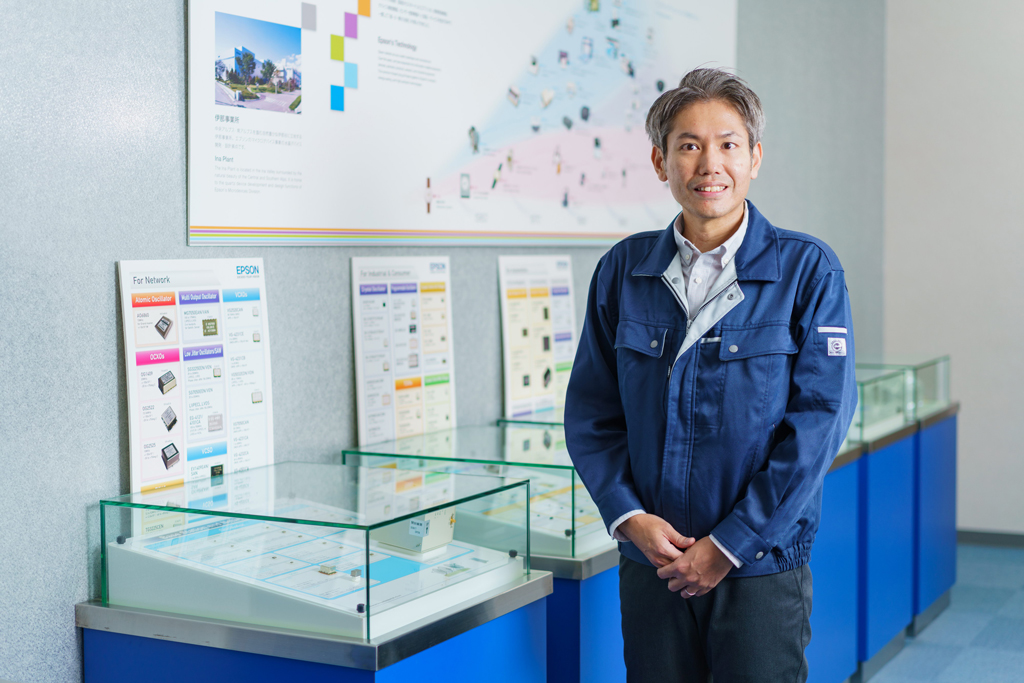
ShimizuAt Epson, the team that develops crystal elements works in the same development department as the team that leverages the potential of these crystals to develop ICs. This arrangement ensures close collaboration in the development of crystal devices. This in turn allows Epson to deliver efficient, compact and precision crystal devices to customers, and to do so in a timely fashion-which is one of Epson's great strengths. Another strength lies in Epson's in-house production system, which integrates all processes, including the process of producing synthetic crystals used in the devices.
Epson will continue to provide a stable supply of high-quality crystal devices that contribute to society.
The titles and positions are as of the time of interviews in November 2020.