Engineer Interviews
Dry Fiber Technology and PaperLab: The World's First Dry Process Office Papermaking System
Epson's Dry Fiber Technology produces highly functional materials by defibrating, binding, and forming fibrous material as needed depending on the application. The hallmark of this technology is that it does not use water.1 Epson's PaperLab, the world's first dry process office papermaking system2, recycles used paper right in the office, so sensitive documents never leave the premises. The PaperLab was made possible by Dry Fiber Technology, which can reduce paper back to fibers without having to dissolve the paper in water. We spoke with one of the engineers on the development team about how the recycling of fibers creates a cycle that enhances value.
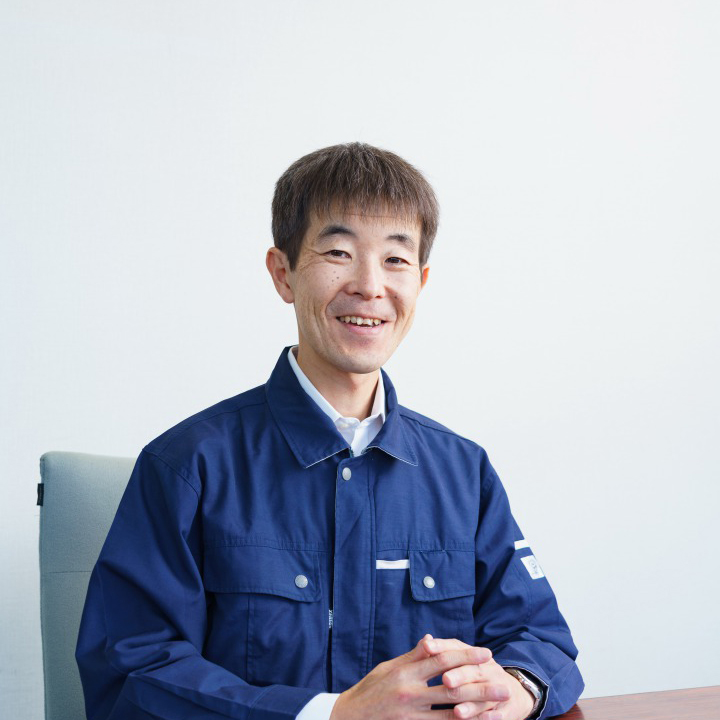
Gomi
The hopes of a printer maker
What prompted you to start research into what became Dry Fiber Technology?
GomiEpson had a huge volume of sensitive documents printed with inkjet printers. Disposing of such documents is bothersome, time-consuming, and expensive, and they inevitably accumulate as they wait to be picked up for disposal by an outside contractor. One day, seeing a mountain of paper, our global president asked the executive in charge of new business development to find some positive way to use all that paper. After all, as a printer company, we wanted our customers to be able to use paper without having to worry about environmental impacts.
We started our research by asking a fundamental question: How is paper made from paper? Since paper is made of fibers, we wondered if it would be possible to reduce paper to fibers and then use the fibers to make new paper.
Paper recycling generally relies on massive factory equipment and a large amount of water. The PaperLab, however, uses almost no water. How did you make it possible to recycle paper without using water?
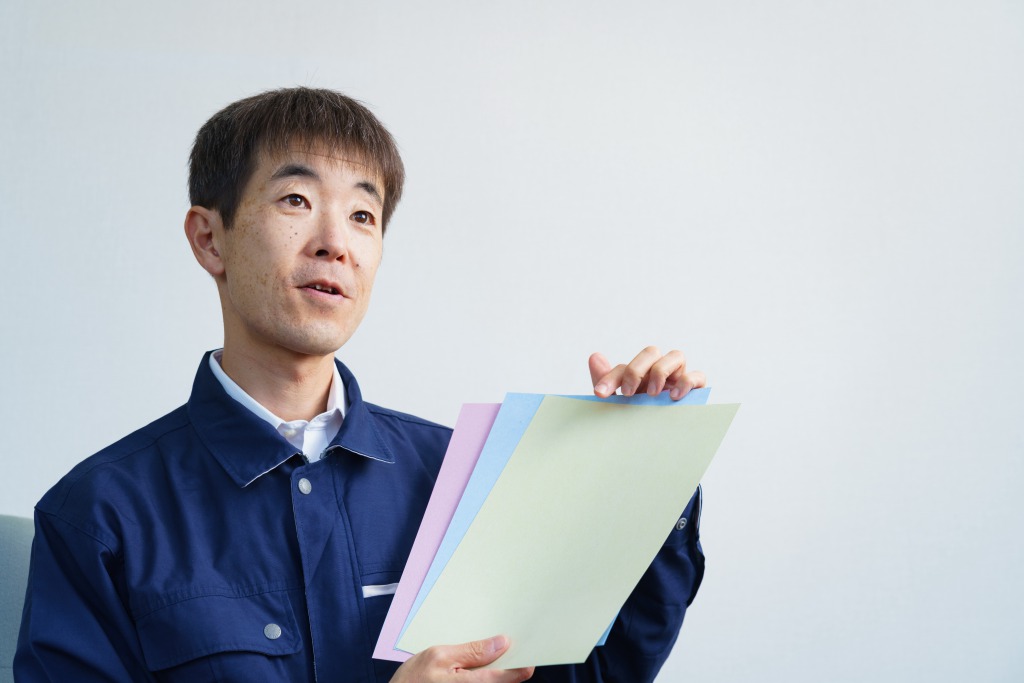
GomiTraditionally, if you wanted to recycle paper, you needed a water supply and a drainage system. We wondered if there was a way to recycle paper in a back office without having to install plumbing and other facilities, and without using water. To find out, we first needed to understand paper.
Washi, traditional Japanese paper, is easy to understand; if you rustle the paper, the fibers will separate. So, we thought it might be possible to reduce paper to fibers by somehow teasing out and separating the fibers without having to dissolve the paper in water. After trying various methods and failing, we finally came up with a technique for impacting and mechanically separating the fibers.
We often talk about paper as if it were a single standard entity, but, in reality, there are many different types of paper. We tried dozens of types of paper. We tried paper that easily picks up a charge and adheres to the surroundings when defiberized. We tried paper that has so many additives that the fibers become weak, and found that paper made from them lacks strength. We established a process for each type.
The ink on the printed matter must be cleaned before defiberization. In normal paper recycling, chemicals are used to wash the dissolved paper and remove the ink. This is not the case with the PaperLab. Instead of dissolving paper in water, it reduces paper to individual fibers by subjecting it to mechanical impacts. The inked fibers are then screened out and separated.
Is the process of remaking paper from these fibers also done with a PaperLab?
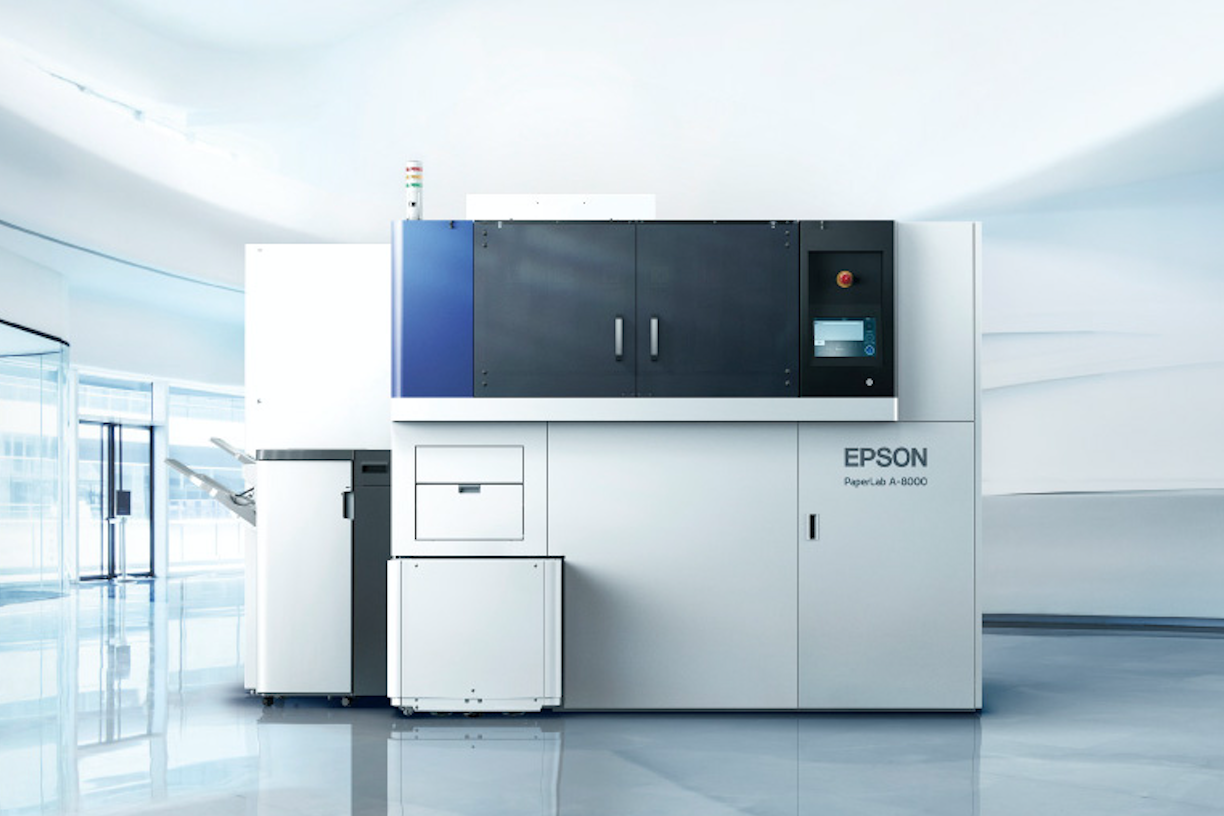
GomiYes. Paper is made by binding and molding fibers together. For this process, we applied technology that is mixed with the fiber to bond the fibers together. The fibers in ordinary paper adhere to each other primarily through the mechanism of hydrogen bonding, a type of electrostatic bond. This bonding mechanism is different from that used by a PaperLab.
Among the people who come to see Epson's PaperLabs are individuals who work for paper companies. The ability to make recycled paper in a virtually water-free process is invariably an eye-opener for them. They took it for granted that a huge amount of water had to be used to reduce paper to fibers, which then had to be dried and bonded. So, it created a sensation among people from the paper and other industries when the PaperLab won the Japanese Economy, Trade and Industry Minister's Prize in the 1st Eco Products Awards category.
Adding value to waste and reducing environmental impacts
The Dry Fiber Technology used in the PaperLab is a groundbreaking invention, but what applications outside of paper are you working on?
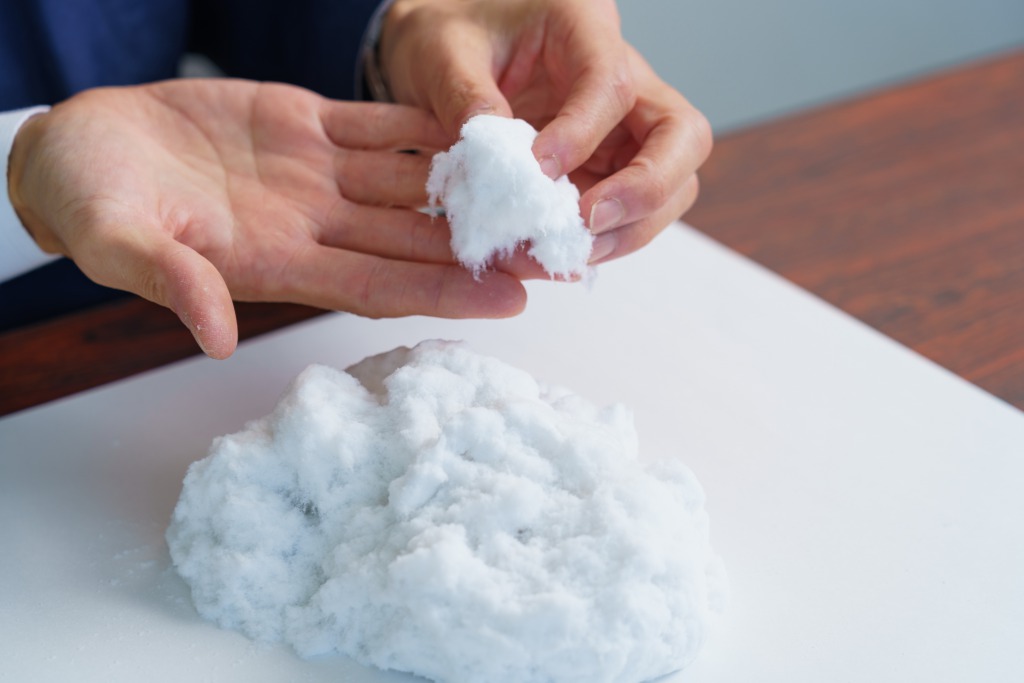
GomiWe're using Dry Fiber Technology to make absorbent ink pads for our printers. We load used paper collected in-house into a machine that defibrates the paper, add a bonding material, apply pressure to form sheets, and then cut the sheets into pads. This method of producing ink pads is being rolled out to Epson factories overseas around the world.
Recycling paper using Dry Fiber Technology produces a porous material that absorbs sound. We are taking advantage of this characteristic by using sheets of this material as sound absorbers in machinery. The material can also be molded into cushioning structures of varying thickness and hardness for Epson products. We continue to drive advances in manufacturing that uses Dry Fiber Technology to add value to what was once treated as waste and reduce environmental impacts. We have named this type of manufacturing SmartCycle.
So you're already using SmartCycle for things like sound absorbing materials and ink pads. What other kinds of projects are in the works?
GomiDry Fiber Technology can, in principle, extract fibers from anything made of fibers, such as lumber and bamboo. Moving forward, we will listen to the needs of our partners and use this technology to transform various types of wastes into valuable materials.
Recently, acting with previously unthinkable speed in response to the threat from COVID-19, we used Dry Fiber Technology to obtain functional fibers and produce intermediate layer filters for face masks.
We will make PaperLabs smaller in an effort to create a future in which a PaperLab is found in
every office, just as every office now has a printer.
It would be great if the dry fiber technology used to regenerate office paper could be applied to various
fiber materials other than paper to realize a "manufacturing the environmental burden" smart cycle. We will
work to solve social issues by focusing on the further evolution of dry fiber technology.
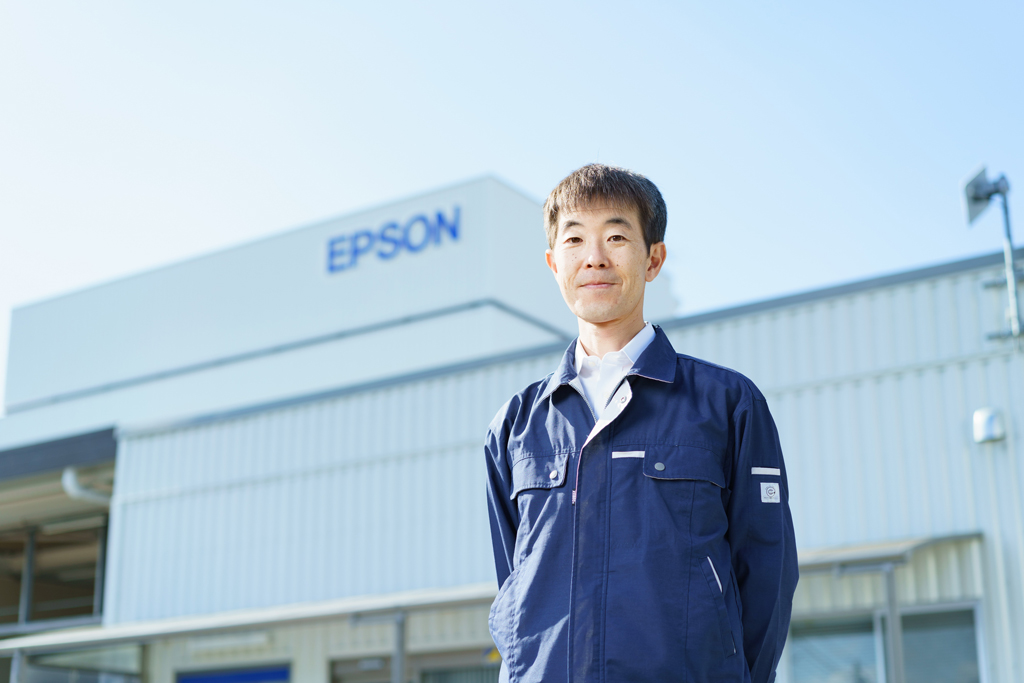
- 1 A small amount of water is used to maintain a certain level of humidity inside the system.
- 2 PaperLab is the first dry process office papermaking system, per Epson research conducted in November 2016.
The titles and positions are as of the time of interviews in November 2020.