Engineer Interviews
Inkjet Printhead Technology for a Sustainable Future
Epson's inkjet printheads enable fast, high image quality printing thanks to their superb ink-ejection performance, compatibility, and durability. Particularly impressive is PrecisionCore, which prints even faster and with even greater image quality. PrecisionCore achieves this feat by making full use of Epson's proprietary Micro Piezo technology and microelectro-mechanical systems (MEMS).
We interviewed Shunsuke Watanabe, who played a leading role in developing PrecisionCore. We talked about what makes this printhead so special and about its potential to serve in a wide range of applications across different business fields. We also discussed the inspiration behind the project and the project's future outlook.
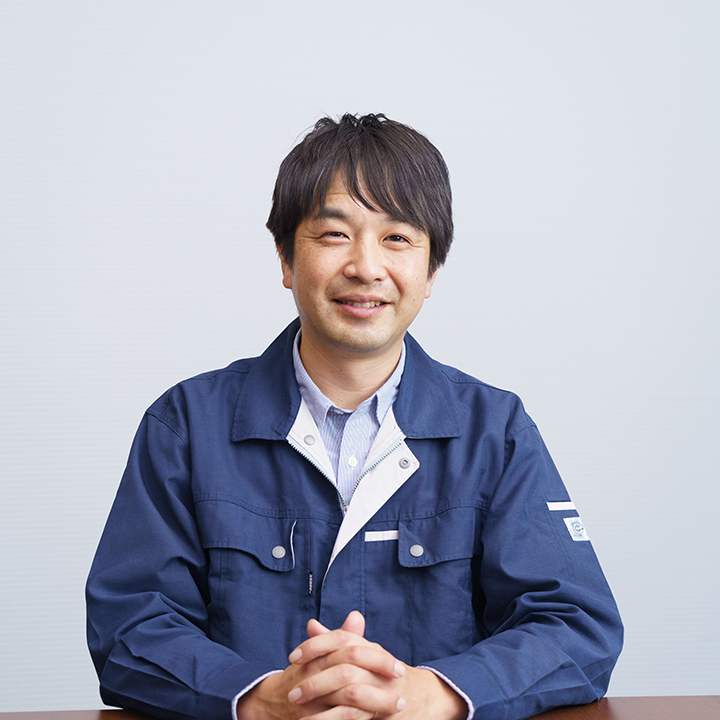
Watanabe
Epson's proprietary Micro Piezo technology
What's makes Epson's inkjet printheads so effective?
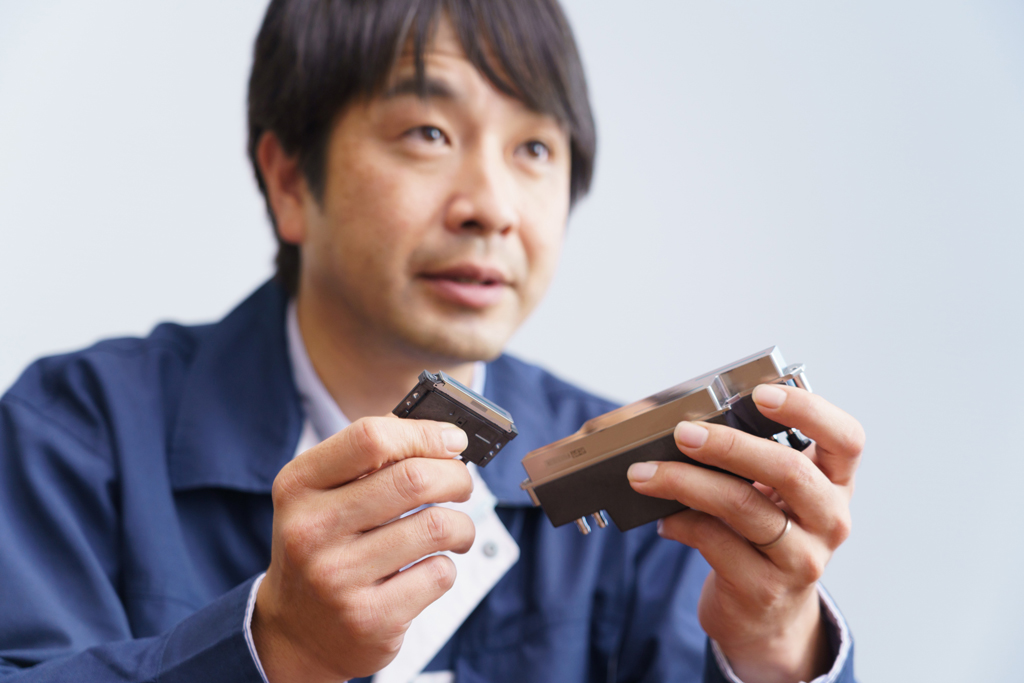
WatanabeEpson's inkjet printheads are piezoelectric. They use Epson's proprietary Micro Piezo technology to achieve superb ink ejection performance, compatibility, and durability.
With piezoelectric printing, you can eject the ink quickly and accurately. Piezoelectric elements change shape when a voltage is applied. Utilizing this phenomenon, you can apply a voltage to the elements to generate mechanical pressure and squeeze tiny droplets of ink out from nozzles. The piezoelectric elements must produce a high level of displacement to eject the necessary amount of ink. Therefore, the performance of a piezoelectric inkjet rests entirely upon the performance of the elements. If the printer has more nozzles, it will print at a higher resolution and speed. But if you want to make an inkjet with lots of high-res nozzles, your piezoelectric elements must produce a very high level of displacement. To meet this requirement, PrecisionCore printheads use Epson's Thin-Film Piezo (TFP) technology. The thinner a piezoelectric element is, the more it will deform when a given voltage is applied. But there is an issue: thinner piezoelectric elements are more fragile. Their fragility makes thin piezoelectric elements harder to produce and less durable. Fortunately, however, Epson had the technological clout to become the first in the industry to produce ultra-thin, high-displacement, highly reliable piezoelectric elements at high volume.
What advantages do PrecisionCore printheads offer?
WatanabeFirst, although PrecisionCore printheads are small, they have many more nozzles compared to conventional printheads. With more nozzles, the printheads eject more ink, enabling faster, higher image quality printing. Another major advantage lies in the scalability of PrecisionCore's print chips. These tiny chips are modular. That means you can easily arrange them in various configurations to suit different kinds of printheads.
I should also mention Epson's proprietary microelectro-mechanical systems (MEMS). The MEMS has enabled us to process the printhead's nozzles uniformly, minimizing variations in size and alignment. With uniform nozzles, the printheads eject ink accurately, resulting in photorealistic prints.
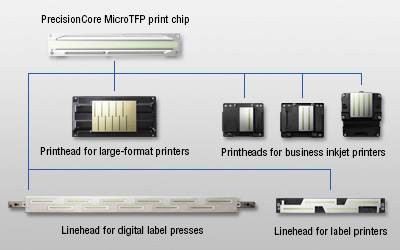
When you standardize the production of a product (as you would for microchips or memory chips, say), competitors can imitate you. However, Epson's TFPs and high-res nozzles are inimitable. These products embody our proprietary technology, which itself is the culmination of many years of painstaking research and development, from the design of materials to the minute production specifications. In other words, only Epson can produce these products. Epson derives its strength from the technological ability to produce such high-precision products in a stable, uniform manner.
Young leaders drive innovation
What was the inspiration behind PrecisionCore?
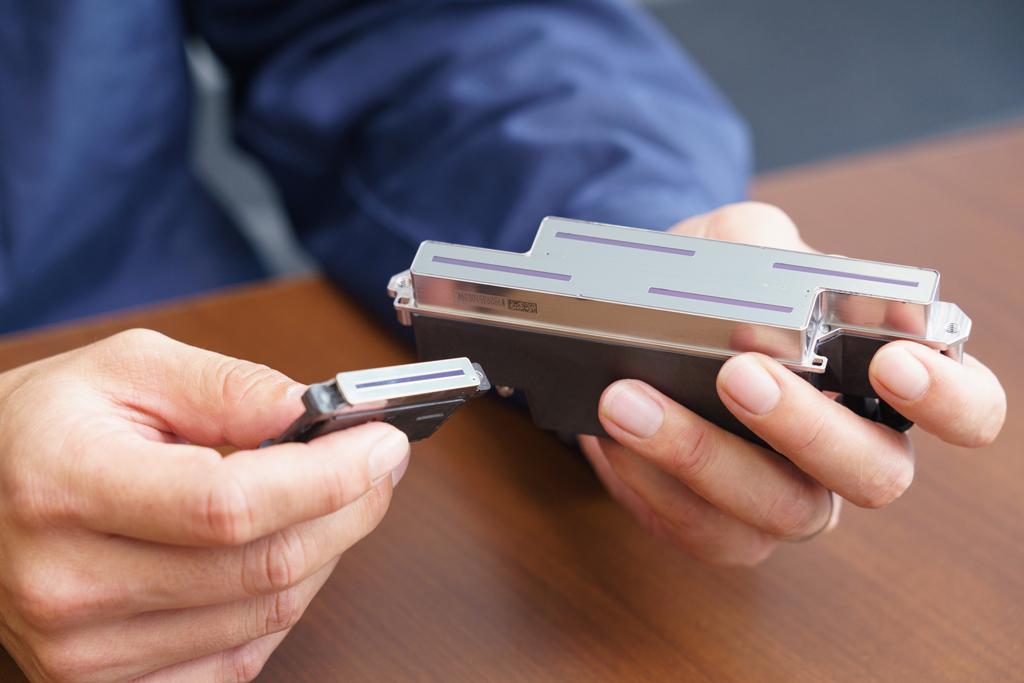
WatanabeBy the turn of the century, Epson' printing business had progressed significantly in consumer markets. Epson was looking to expand into a range of business markets, from offices to industrial applications. To that end, Minoru Usui (then President and Representative Director, now Chairman) issued a major directive to develop a printhead compatible with all printing markets. Accordingly, we started work on a new printhead that would raise the level of our core technology. That printhead was PrecisionCore MicroTFP. The ultimate purpose of the project was to take inkjet printing to the next level and forge new, broader business segments.
The person who managed the project at the time told us that we could only evolve technologically if we demolished our existing technology (in a good sense) and reassembled it. To that end, he said, young engineers needed to engage actively and bring fresh ideas. He assembled a group of young leaders aged around 30. Once these young engineers took charge, the project to develop PrecisionCore MicroTFP went into lightspeed.
What challenges did you face in developing PrecisionCore printheads?
WatanabeThe toughest challenge was to upgrade performance while also reducing size. We started to strip away all the redundant elements in the nozzles, ink channels, actuators, electronics, and so forth. From corner to corner, we removed everything unnecessary. Everyone, from designers to production engineers, played their part to satisfy all the task requirements, accepting no compromise. Time constraints made the project all the more challenging. In just a short space of time, we had to identify the steps toward the goal and envisage not just how the finished product would look but how it would be produced.
Going further with open innovation
Will there be even more applications for inkjet printing in the future?
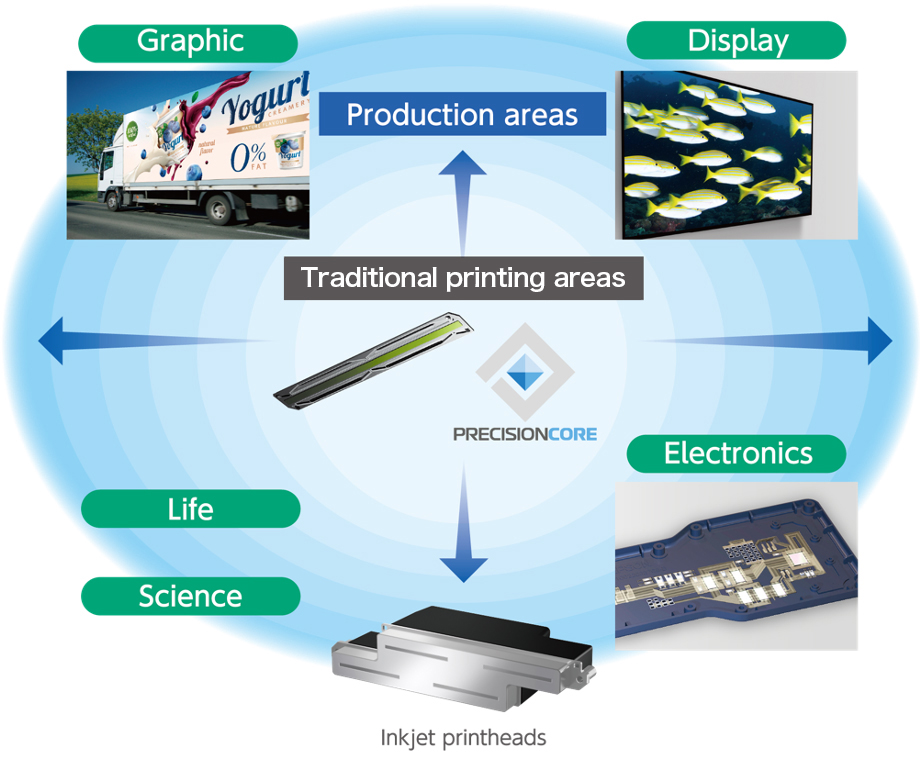
WatanabeOur inkjet printheads already serve in a wide range of fields. In addition to consumer use, the printheads serve in offices and in industrial applications such as signage, posters, and labeling. For each of these applications, we are working to further upgrade print quality and speed. Additionally, we offer these markets solutions that are more eco-friendly. Many conventional printers are not kind to the environment because, among other things, they produce waste fluid. By contrast, our inkjet printers use no more ink than is necessary. This no-waste technology reduces the printer's carbon footprint. Thus, by encouraging these markets to switch from analog to digital printing, we can promote a less wasteful, more energy-efficient form of printing for small-lot production.
Besides this, there remain many untapped possibilities. Epson's inkjet tech, with its ability to accurately place tiny ink droplets without contact, offers a digital solution to printing companies with cutting-edge large-volume printers. It can also help revolutionize printed electronics (such as printed circuits and microstrip antennas) and bioprinting.
As part of our effort to capture these new opportunities, we opened the Fujimi Inkjet Innovation Lab in 2019. This lab runs ejection testing using devices fitted with Epson's inkjet printheads. In this way, we explore many different potential applications. The lab is a collaborative venture. We invite our partners to visit the lab and collaborate with us in creating new markets and services. Our mission is to come up with not one or two, but 10 or 20 new ideas for manufacturing processes.
Contributing to a brighter, more sustainable future
What would you say to people who might have ideas for new applications?
WatanabeI'm excited about all the possibilities that still lie ahead. As Epson's inkjet technology continues to evolve, and as we continue collaborating with partners, you will see the emergence of many more applications. To give some everyday examples, printing is now used for textiles (t-shirts and other clothing), wallpaper, faux woodgrain finish for desks, exterior wall design, cardboard packaging for home deliveries, and edible souvenirs. In business and industry, printing is used for circuit boards, shop displays, and biotesting. As these examples illustrate, our inkjet technology can potentially meet a whole host of needs. To give these ideas shape, we'll keep working on innovative challenges in collaboration with a broad range of partners, never giving up until we reach the goal. If you have an innovative idea, if you think something could be done better, or if you want to try something new, we'd love to hear from you. Let's work together to make your idea a reality.
Epson certainly welcomes new challenges, as they bring opportunities for further growth. Ink and printhead technology still has plenty of scope to become more advanced. I want Epson to keep pushing the technological envelope so that, in five or ten years from now, the technology will have changed beyond recognition and be doing things we never thought possible. We have no-waste technology-technology that ensures that the printhead ejects no more ink than is necessary. We also have technology that saves energy in printing and production processes, and technology that ejects ink onto many kinds of materials without contact. If we use these technologies to the full, then we can both offer better value to the customer and solve societal and environmental issues, thus contributing to a brighter, more sustainable future.
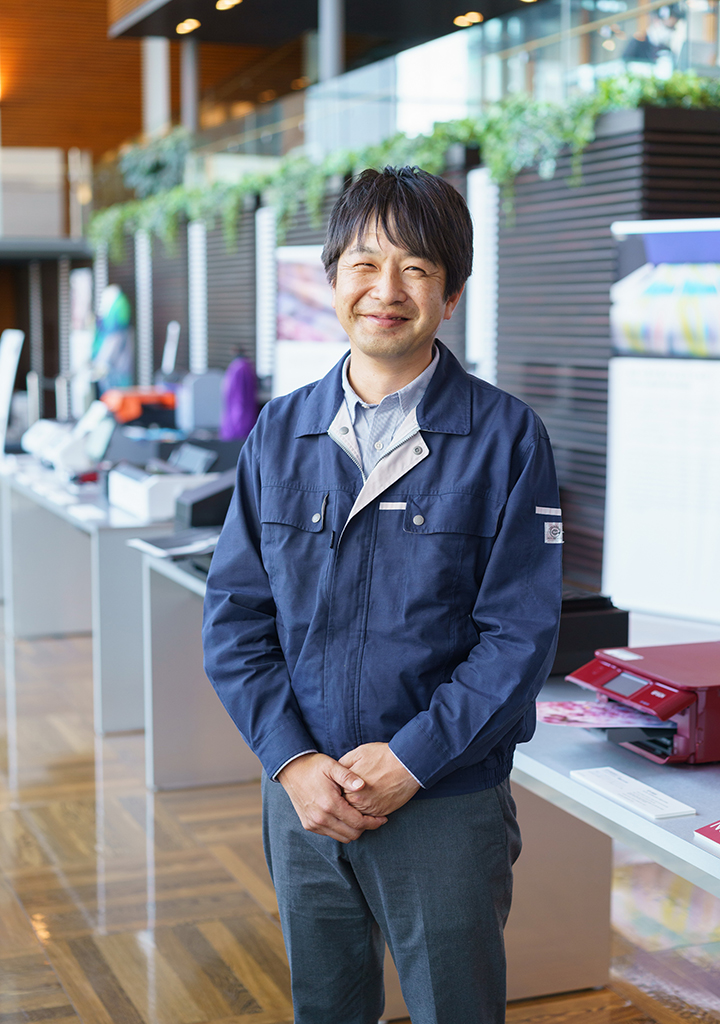
The titles and positions are as of the time of interviews in November 2020.