AE-M3 / M10 / M3V
Micro injection molding machine
2022
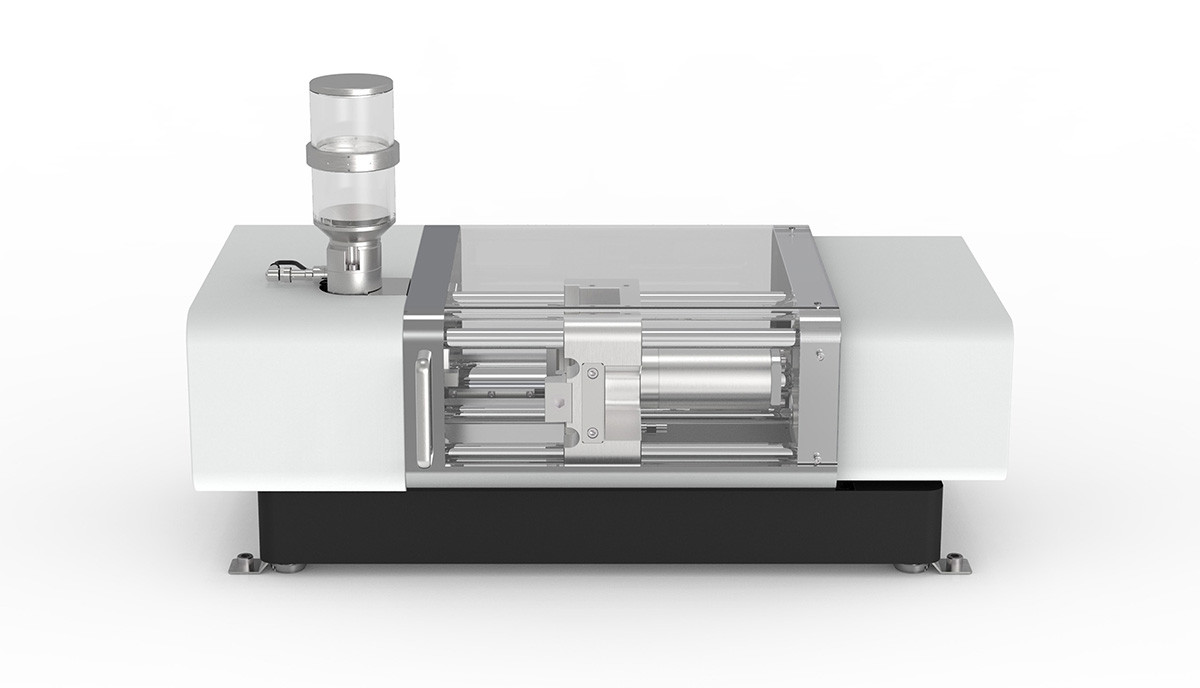
"Making Small Things Smaller" — Transforming Manufacturing with Injection Molding
The smaller the part, the more material and energy are wasted in production. Epson's solution to this problem is to make small things smaller. To create a micro injection molding machine that combines economic efficiency and environmental performance, we reimagined the conventional concept of injection molding machines. This machine enables precise injection with minimal energy and a beautifully refined molding process. The clear casing allows producers to witness the creation of the molded part, inspiring a sense of excitement for manufacturing.
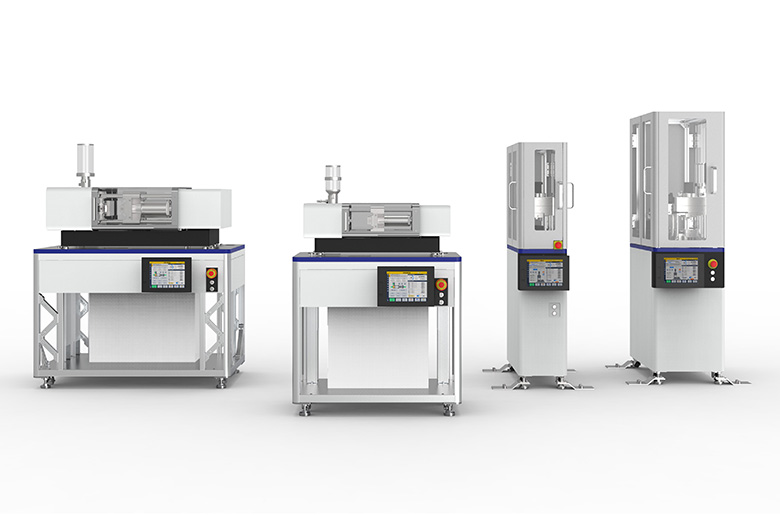
A Compact Capsule That Condenses the Molding Process
A clean, minimalist design with a compact form that embodies efficiency—this is epitomized by the clear central case. This transparent case not only integrates the internal structure's aesthetic into the overall design but also allows operators to quickly assess the mold status without frequently opening and adjusting the cover.
The color scheme, centered on metal and white, was chosen to ensure that the machine looks aesthetically pleasing both as a standalone unit and when multiple units are lined up. This unified lineup brings a fresh, modern image to the factory environment.
Precise Injection Molding With Minimal Energy and Zero Waste
Traditional large-scale plastic molding machines excel in mass production but often result in significant material waste. Optimized for low-volume, high-variety production, the AE-M3 / M10 / M3V models achieve compact, efficient injection molding through an innovative disk drive system. In addition to reducing the machine's size and enhancing energy efficiency, these models minimize waste from things like runners produced during the molding process, thereby reducing CO2 emissions and environmental impact.
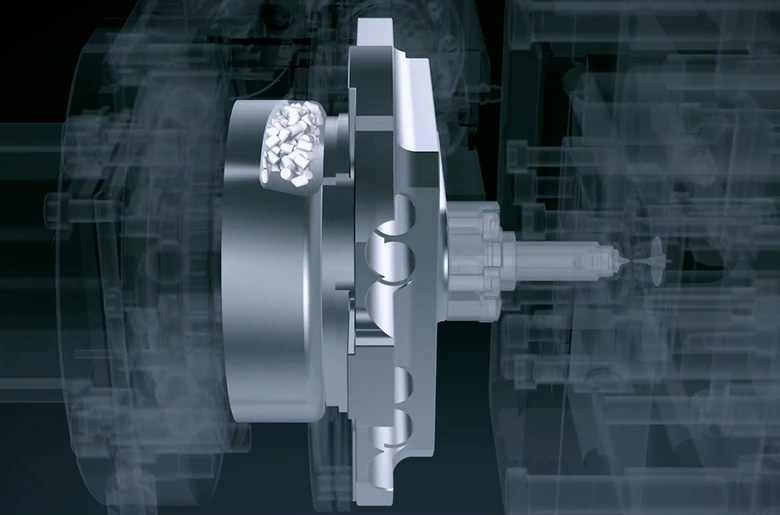
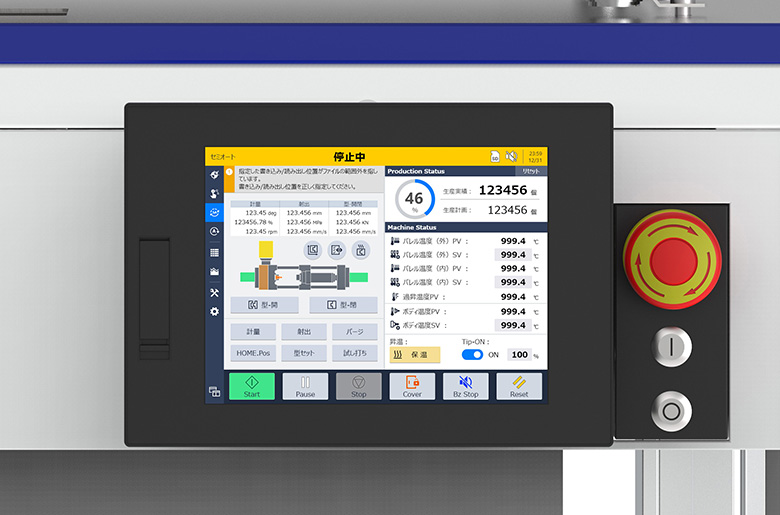
Precisely Controlling Molding Conditions
The control panel for precisely managing molding conditions is designed to prevent errors and avoid confusion, prioritizing the clear display of essential information for users. Functional zoning enables operators to instantly grasp the molding status. By glancing between the mold and the control panel, operators can set and monitor conditions like injection speed, pressure, and microprobe temperature with ease.