C3 Series of Compact 6-Axis Robots
Product Features
June 2009
Specifications
Construction: Vertical articulated (six degrees of freedom)
Max. reach of P point (rotation centers of joints #4, #5, #6): 600 mm
Cycle time (1-kg payload): under 0.3 sec.
Maximum joint ranges
Joint #1 (rotates the robot): ±170 deg (±180 deg without mechanical stop)
Joint #2 (extends, retracts the lower arm): -160 deg to +65 deg
Joint #3 (extends the vertical reach): -225 deg to -51 deg
Joint #4 (wrist roll): ±200 deg
Joint #5 (wrist pitch & yaw): ±135 deg
Joint #6 (wrist twist): ±360 deg
Maximum joint speeds
Joint #1: 450 deg/s, Joint #2: 450 deg/s, Joint #3: 514 deg/s,
Joint #4: 553 deg/s, Joint #5: 553 deg/s, Joint #6: 720 deg/s
Allowable moment of inertia (GD2/4)
Joint #4: 0.15 kg·m2, Joint #5: 0.15 kg·m2, Joint #6: 0.1 kg·m2
Repeatability: ±0.02 mm
Payload: 1 kg (rated); 3 kg (max.); 5 kg (with arm downward positioning)
Weight: 26 kg
The C3 series was engineered for precision assembly of small parts. These robots were Epson's first 6-axis models to be equipped with Residual Vibration Control, Epson technology that enables Epson robots to move at high speeds with minimal vibration. These robots proved very effective in increasing the efficiency and productivity of users' floor space.
- Speed and precision
- Offered excellent production efficiency with a good balance between best-in-class speed and precision1.
- Standard cycle times in the 0.3-second range2, with repeatability of +/-0.02 mm - Slim body
- High space efficiency
- The manipulator is only 1/44th the size of its working envelope.
- An elbow area (joint #3) that is only half the size of that of the previous model, the PS3-AS003.
- A 42% narrower arm width than on previous models.
- Less interference with peripherals, walls, and ceiling permits more compact installation - Dexterous wrist
- Compact wrist (joint #5) with wide working envelope4 enables smooth movement and the ability to work from many angles
- Minimal interference with surroundings improves flexibility in hand design - Installation flexibility
- Can be mounted on a ceiling, wall, floor, tabletop, or at a skewed angle
- Provides layout freedom and high space efficiency
1 Best at the time the robots were released
2 With a 1-kg payload
3 The radius, from the center of the joint to the edge of the protruding part (figure 1)
4 See figures 2 & 3
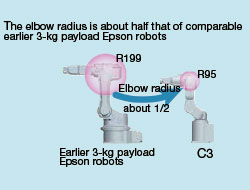
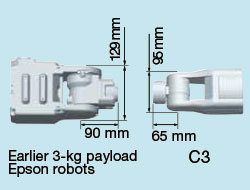
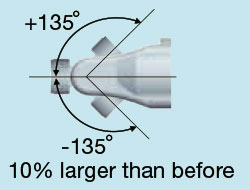
Story Behind the Creation
In around 2002, we started to see a rise in customer demand for robots that could perform assembly and other complicated tasks. At the time, however, Epson only had SCARA robots5.
To meet customer requirements, we needed a 6-axis robot that would be capable of more complex movements. We were able to commercially develop a 6-axis model with the help of some OEM mechanical parts. But this was still not enough to meet customer requirements. The biggest objective of our robot business was to develop and internally manufacture an Epson 6-axis robot. To do so, we knew we had to take maximum advantage of the strengths of our highly competitive SCARA robots.
We began by researching and learning about our customers, the majority of whom are in the electronics industry. We found that they were using 6-axis robots with large working envelopes6 of 700 mm or 900 mm for jobs that could have been accomplished easier with smaller robots. The fact was that 6-axis robots, which are generally larger and slower than SCARA robots, were hard to use. Customers in the electronics industry needed fast-moving, compact 6-axis robots. Other robot manufacturers were focusing on six-axis robots that could handle payloads of between 6 kg and 8 kg, but knowing that we could meet customer requirements with models that could handle payloads of 3 kg helped us to make our robots more compact. The design and development teams joined forces in the belief that they could meet customer requirements if they could commercially develop 6-axis products based on Epson's efficient, compact and precision technologies.
5 SCARA robots are robots whose arm moves horizontally.
6 The working envelope, also called a work area or workspace, is the area over which work can be performed when the arm is fully extended.
Reception and Market Impact
Given what we learned from further research, we articulated four product concepts7 that, if realized, would enable us to deliver products that customers wanted. The sales and marketing team found that potential customers responded extremely positively to the proposed concepts, cementing our belief that the robots we had in development would be accepted.
We were able to deploy the technology we had developed for SCARA robots in 6-axis products, and a prototype achieved movements of unprecedented speed.
Furthermore, the speeds far exceeded our own target thanks to the smaller, lighter wrist on the arm designed for 6-axis robots (figure 4). These features enabled our C3 robots to use space more efficiently than the products of competitors while also providing layout flexibility (figure 5).
Until the emergence of the C3 series, it was considered difficult to use both 6-axis robots, which were slow, and SCARA robots, which were fast, on the same production line, but the C3 changed all that.
7 The four concepts:
(1) Fastest-in-class cycle times
(2) Minimal interference with surroundings
(3) Dexterity
(4) Efficient use of space and layout flexibility
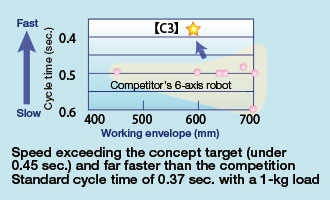
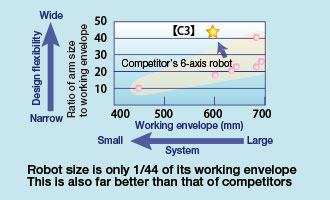